[Image above] Mycelium, the root-like structure of most fungi, is a potential material for use in green construction. Credit: andersfloor, Pixabay
The construction industry has a major impact on the environment. It generates about 40% of the annual global CO2 emissions, and just three materials—concrete, steel, and aluminum—are responsible for 23% of total global emissions on their own.
To reduce this impact, researchers across industry, academia, and the government are investigating alternative low-carbon materials and processes, with some—such as mycelium—pulled directly from nature.
Mycelium is the root-like structure of most fungi. It consists of a network of tiny thread-like strands called hyphae that collect food, water, and nutrients as well as anchor the fungus.
Mycelium’s fast-growing nature and complex network allows it to act as a natural glue, which also happens to be water, mold, and fire-resistant. These properties, in addition to being biodegradable, give mycelium potential as a green construction material.
Mycelium has been used in medicinal industries and molecular compounds for a long time, but its use in construction can be traced to 2006. That year, Rensselaer Polytechnic Institute undergraduate students Eben Bayer and Gavin McIntyer developed an experimental mycelium composite as part of an Inventor’s Studio class. A year later they founded Ecovative, and today the company offers a variety of sustainable products based on its MycoComposite and AirMycelium technologies.
Several companies now offer mycelium-based products, such as MycoWorks, NEFFA, and Mogu. Other organizations are working to develop mycelium-based technologies as well. Several recent innovations in this area are spotlighted below.
Mycocrete: Knitting 3D structures and forms with no seams and no waste
In July 2023, members of the Living Textiles Research Group, which is part of the Hub for Biotechnology in the Built Environment at Newcastle University in England, published an open-access paper describing a new mycelium-based paste called mycocrete.
The Newcastle researchers developed this paste for use in textile-based formworks. Conventional mycelium composites are grown in rigid brick-shaped molds, but the need for oxygen to grow the mycelium limits how thick these molds can be. In contrast, textile-based formworks allow for mycelium composites to be grown in more complex and efficient geometries.
The researchers injected the mycocrete into flexible fabric tubes made from merino yarn. By growing mycelium in this knitted formwork, they successfully created a self-supporting arched dome consisting of very slender tubular arches. Notably, the formwork allowed for the structure to be cast continuously without any connecting joints, which can be weak points in a structure.
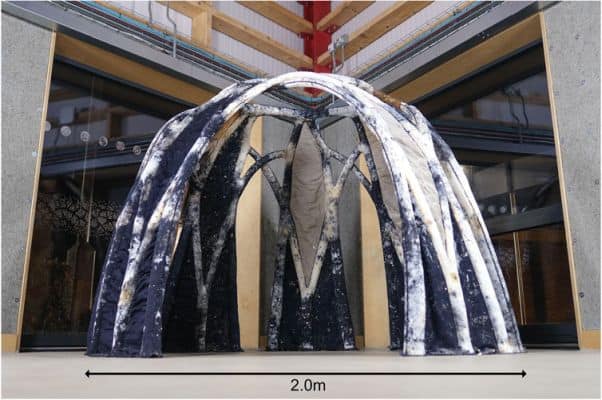
The self-supporting arched dome created using mycocrete and a knitted framework. This structure, which the researchers called BioKnit, was exhibited in the Hub for Biotechnology in the Built Environment at Newcastle University. Credit: Hub for Biotechnology in the Built Environment (CC BY 4.0)
In a Newcastle press release, academic track fellow Jane Scott says, “The mechanical performance of the mycocrete used in combination with permanent knitted formwork is a significant result, and a step toward the use of mycelium and textile biohybrids within construction.”
Installation showcases the building potential of mycelium
During the annual Clerkenwell Design Week in May 2023, London-based research group PLP Labs, founded by PLP Architecture, shared the results from a year-long study of mycelium composites through an installation called Symbiocene Living.
The study, which explored the building properties of mycelium biocomposites, resulted in the development of hybrid blocks that consisted of 3D-printed wood shells filled with a mycelium-based substrate. The substrate consisted of agricultural waste, such as straw, wood chips, and sawdust, injected with mycelium. The substrate was allowed to grow over several weeks before being dried under intense heat to prevent any further growth.
PLP Labs created 84 hexagonal blocks using this mycelium composite, and these blocks were arranged to form a partition, table, seating, and planters for the Symbiocene Living installation.
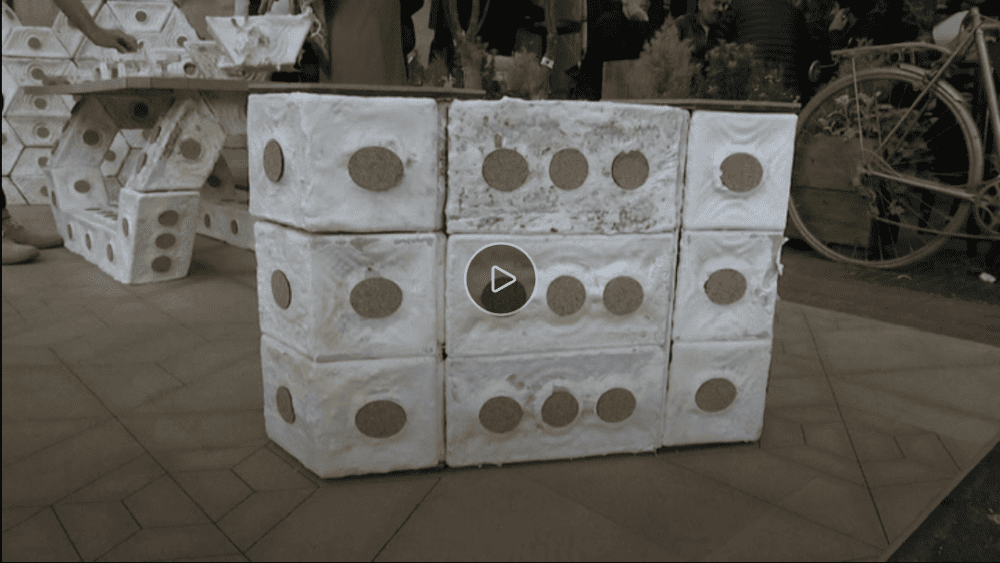
This video cannot be embedded on external sites. Click the image above or this link to view the video on the original website. Credit: World Economic Forum
Mycelium technology rejuvenates low-income neighborhoods
In Cleveland, Ohio, architectural firm redhouse studio is planning to use mycelium technology to renovate blighted homes and buildings found in the city’s low-income areas, as described in RuMoer (pp. 74–79), the official periodical of the BouT study association at the TU Delft Faculty of Architecture and Built Environment.
The company’s Biocycler process, which is used to create so-called Mycoterials, involves
- Collecting construction and demolition waste containing organic and cellulosic material.
- Grinding the waste into a fine substrate, which is then injected with mycelium to bind the waste at a cellular level.
- Pressing the mycelium-injected substrate into any shape, resulting in a strong, lightweight, and biodegradable material that is also insulative, fire resistant, and sound attenuating.
When paired with a weather-proof barrier, redhouse believes these mycelium composites can replace almost all standard construction materials at a fraction of the cost and with a lower embodied footprint.
Table 1. A comparison between redhouse’s Mycoterials and conventional concrete.
Property | Mycoterials (redhouse) | Concrete |
Ultimate compression | 26 MPa | 24 MPa |
Modulus of elasticity | 206 MPa | 25 MPa |
R-value | 3.8/inch | 0.8/inch |
Processing temperature | 15–30°C | 1,400°C |
Embodied carbon footprint | -15 (kgCO2/block) | 3.5 (kgCO2/block) |
In a demonstration project described in the RuMoer article, redhouse used Mycoterials to create insulation panels for the outer shell of a bee barn at Ohio City Farm in Cleveland.
Additionally, redhouse collaborated with Standard Bank Group and the Massachusetts Institute of Technology’s Center for Bits and Atoms on a pilot project to turn an invasive plant in Namibia, Africa, called the encroacher bush into Mycoterial bricks. An independently operating African start-up called MycoHab is now scaling the process developed during the pilot project.
Author
Laurel Sheppard
CTT Categories
- Construction
- Material Innovations