[Image above] Example of a stretchable electronic consisting of etched silicon attached to a polymer backing. The ensemble minimizes silicon use and is quite flexible to survive inflation and deflation of the balloon. Credit: Steve Jurvetson, Flickr (CC BY 2.0)
I’ve seen quite a few articles pass through my newsfeed on the quickly advancing commercialization of printed electronics.
Printed electronics is an emerging technology under the umbrella of additive manufacturing that uses functional inks to print circuits and electrical components on various substrates. Manufacturers are excited by the technology because of the possibility to place electronics on flexible substrates, such as paper and clothes, which would open up a whole new way to monitor different systems, from industrial processes to the human body.
While printing on flexible substrates is moving swiftly toward commercialization, research on creating stretchable electronics has a bit further to go.
In contrast to flexible electronics, which generally refer to electronics that can bend, stretchable electronics are able to stretch, twist, and compress, providing a wider range of deformation capabilities. You can imagine flexible electronics like using paper to wrap a ball (it would wrinkle) versus stretchable electronics like using rubber to wrap a ball (it would conform to the surface).
There are two different but complementary strategies for fabricating stretchable electronics: 1) engineering new structural constructs from established materials, and 2) assembling a device directly from stretchable materials. Regardless of the strategy used for fabrication, the expanded range of motion available to the final stretchable electronic causes challenges for thermal management.
Just as you work up a sweat during yoga, the stretching, twisting, and bending of materials in stretchable electronics generates thermal energy that cannot be dissipated using the passive heat exchange methods used in traditional, rigid electronics. So, other methods of thermal management must be used.
In a recent open-access perspective paper published in npj Flexible Electronics, Qingdao University associate professor Bin Sun and Shanghai Jiao Tong University professor Xingyi Huang explore some of the current thermal management strategies being investigated for stretchable electronics.
They begin by discussing the types of materials and structures that do and do not work well for stretchable electronics. For example,
- Bulk polymers usually have low thermal conductivity due to the amorphous phase with defects, but thermal conductivity can be enhanced using the right fabricating process, such as electrospinning and mechanical stretching.
- Inorganic crystalline materials have high thermal conductivity but lack the necessary elasticity. Such materials can be tailored into configurations that are convenient for deformation, but the small stretching ratio and the high cost restrict the materials’ potential in real-world applications.
- Solution-casted composites, in which fillers are usually homogeneously dispersed in a polymer matrix, can achieve improved thermal conductivity via low-level stretching that aligns the fillers. However, high-level stretching can cause the fillers’ contact areas to decrease and sometimes even separate from each other, which negatively impacts the materials’ heat dissipation capabilities.
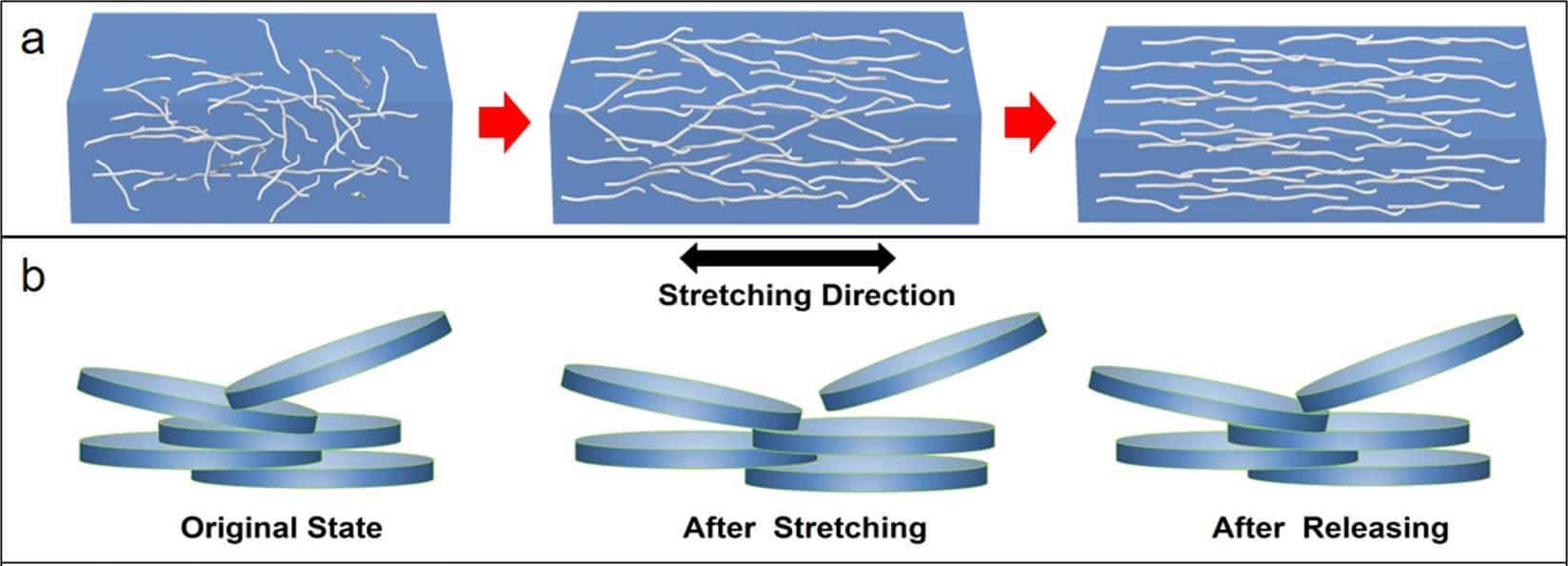
Examples of stretching in solution-casted composites. a) High thermally conductive nanofillers align under low-level stretching, improving thermal conductivity. Credit: Sun and Huang, npj Flexible Electronics (CC BY 4.0) b) Schematic diagram of the change in thermally conductive pathways during the high-level stretching–releasing process. Reprinted with permission from Tan et al., Nature Communications (CC BY 4.0)
Solution-casted composites have received some of the most attention in recent studies. When studying these materials, Sun and Huang describe several aspects in particular that must be considered and offer several possible solutions for each.
Mechanical mismatch between the polymer and active filters
During numerous stretching–releasing processes, mechanical mismatches can lead to small cracks occurring in the composite, which can ultimately cause structural deterioration.
Possible solution: “To prevent the thermally conductive pathways from damage, self-healing elastic materials are important in the future.”
Retention of thermally conductive pathways
Thermal conductivity is likely to drop during stretching due to the decrease or separation of contact areas between the conductive fillers.
Possible solution: “For solid composites, patterned deposition of highly thermally conductive fillers is helpful for maintaining the stable thermal conductivity … However, the mechanism of thermal conductance of solid composites under tensile stress remains unknown yet.”
Permeability of air, moisture, and liquid
Permeability of air, moisture, and liquid can help avoid serious health concerns during long-term wearing. However, permeability is usually obtained by the porosity of materials, while high thermal conductivity is normally acquired by a dense, impermeable architecture.
Possible solution: “The strategy of precise depositing highly thermally conductive fillers porous substrate is hoped as a good choice.”
Operating temperature
Compared with traditional electronics, stretchable electronics based on solution-casted composites are generally not suited to working at high temperatures because external heat can destroy the core components.
Possible solution: “Incorporation of phase change materials in the deformable substrate is capable of the control of heat dissipation direction … But it may not appropriate for the long period of time operation of electronic devices due to the certain contents of phase change materials in the composites. Also, there are publications on thermal rectifiers and thermal diodes, which proposed the possibility to manipulate the heat to flow preferentially in one direction.”
Sun and Huang conclude by stating that many challenges still lie ahead for the development of stretchable electronics with advanced thermal management. However, further research is expected to “greatly promote the development.”
The open-access paper, published in npj Flexible Electronics, is “Seeking advanced thermal management for stretchable electronics” (DOI: 10.1038/s41528-021-00109-9).
Author
Lisa McDonald
CTT Categories
- Basic Science
- Electronics
- Thermal management