[Image above] Will all-solid-state batteries power our future? Credit: Peter Miller; Flickr (CC BY-NC-ND 2.0)
If I was a fossil fuel, I would be getting a little nervous about the competition right about now.
Renewable energy reached a new high last year, accounting for almost 75% of new electricity-generating capacity built in 2019. Solar power led the way, followed by wind—together accounting for almost 90% of the new total capacity.
In addition to the capacity to generate renewable energy, an often-overlooked component of our ability to transition to an all renewable-powered future is grid storage. That is important because natural energy sources, such as the sun and wind, are variable—they fluctuate up and down in their capacity, which limits their ability to meet energy demand at any given time.
Energy storage solves that problem by affording the ability to collect renewable energy and save it for later use. And while there are various forms of energy storage, batteries are perhaps one of the most familiar solutions, and they also offer some of the highest efficiencies.
Most commercially prevalent today are lithium-ion batteries, although they have their limits and drawbacks—which is precisely why many researchers are now investigating all-solid-state batteries instead to power our future.
All-solid-state batteries, as their name implies, feature a solid electrolyte—often made of ceramic materials—instead of the liquid electrolyte found in lithium-ions (the part of lithium-ion batteries that makes them prone to catch fire).
So all-solid-state batteries are safer than lithium-ions, but they also boast higher performance, longer lifecycles, and wide operating ranges. Plus, on a systems level, their ability to be easily stacked together means all-solid-state batteries offer higher potential capabilities than lithium-ions, despite the batteries’ materials having similar energy densities.
Together, these attributes put all-solid-state batteries in a leading position as the most promising technology to power our future energy needs, whether for electric vehicles or grid storage.
Much research and development on all-solid-state batteries happened in the past several years (see here and here, for example), steadily building momentum toward their commercialization. However—as detailed in the feature story from the September 2019 issue of the ACerS Bulletin—significant challenges remain, including developing more scalable manufacturing processes, before all-solid-state batteries can have their moment.
Similar sentiments are echoed in a review article published in Nature Nanotechnology, in which nanoengineers at the University of California, San Diego (UCSD) outline a research roadmap detailing four remaining challenges to address before all-solid-state batteries reach their commercial potential.
1. Create stable interfaces with solid electrolytes
2. Establish new tools to characterize solid-state batteries
3. Develop scalable and cost-effective manufacturing
4. Design batteries for recyclability
“It’s critical that we step back and think about how to address these challenges simultaneously because they are all interrelated,” Shirley Meng, nanoengineering professor at UCSD Jacobs School of Engineering, says in a UCSD press release. “If we are going to make good on the promise of all-solid-state batteries, we must find solutions that address all these challenges at the same time.”
Create stable interfaces with solid electrolytes
Although researchers have developed various battery materials with sufficiently high ionic conductivities, poor interfacial stability still limits their use in all-solid-state batteries.
“At this point, we should shift our focus away from chasing higher ionic conductivity. Instead, we should focus on stability between solid-state electrolytes and electrodes,” Meng says in the press release.
Particularly, that stability is challenged by reactions between both cathode and anode electrodes and the solid-state electrolyte, which cause voltage loss and reduce power-generating ability, leading to poor battery performance.
One potential solution to mitigate these interfacial reactions is to incorporate a thin coating material in between the electrodes and electrolyte, and various such strategies have shown some success in previous research. However, “Despite these results, there is still a lack of consensus on how to select protective coating materials,” the UCSD authors write in the paper.
Another potential solution is to go moderate—instead of opting for the electrolyte with the highest ionic conductivity, the researchers suggest electrolytes with more moderate ionic conductivities yet better interfacial stability can provide better battery performance overall.
Establish new tools to characterize solid-state batteries
Despite being beneficial for battery safety and performance, the solid electrolyte of all-solid-state batteries introduces a significant challenge when it comes to characterizing these batteries in operation—the methods traditionally used to probe the transparent electrolytes of lithium-ion batteries do not adequately visualize the solid and buried components in all-solid-state batteries. Plus, many of these solid electrolyte materials are sensitive to the energy sources of the testing methods, further complicating analysis.
Scientists currently use electrochemical methods, such as galvanostatic cycling or impedance spectroscopy, to probe all-solid-state batteries. “However, such techniques are limited, because they cannot provide elemental or morphological information that are vital to properly evaluate cell failure mechanisms,” the authors write in the paper.
In other words, because we cannot adequately see inside all-solid-state batteries during operation, it is difficult to analyze why they fail or understand what limits their performance.
Previous work showed some success in analysis with X-ray computed tomography, neutron-based techniques, nuclear magnetic resonance imaging, cryogenic focused ion beam techniques, and spectroscopy, but ability of these techniques to adequately characterize all-solid-state batteries highly depends on the individual battery materials, and all listed methods have certain drawback and limitations.
More sensitive, reliable strategies are still needed to adequately characterize all-solid-state batteries in operation—information that is essential to further improve this technology and bring it to commercial scale.
Develop scalable and cost-effective manufacturing
There have been no shortage of lab-scale battery developments over the past several decades of research, including for all-solid-state batteries. Yet the vast majority of these discoveries never move beyond the lab because they are too expensive or cannot be manufactured at scale, two components critical for commercial success.
That is particularly true for inorganic solid electrolytes like ceramics, which often lack the necessary mechanical stability in scale-up.
“For example, many become highly brittle when made thin enough for roll-to-roll manufacturing, which demands thicknesses of under 30 micrometers,” according to the UCSD press release.
“To overcome such limitations, researchers at UC San Diego are merging multiple fields of expertise,” the release continues. “They are combining ceramics used in traditional material sciences with polymers used in organic chemistry to develop flexible and stable solid electrolytes that are compatible with scalable manufacturing processes. To address problems of material synthesis, the team also reports how solid electrolyte materials can be scalably produced using single-step fabrication without the need for additional annealing steps.”
Design batteries for recyclability
When it comes to lithium-ion batteries, recyclability is not one of their strong suits. That is a problem from a sustainability perspective as well as a materials perspective because it represents a loss of valuable battery materials such as lithium, cobalt, and nickel.
Because all-solid-state batteries are just approaching the commercialization phase of their development, the UCSD researchers argue that an entire sustainable lifecycle approach is needed to prevent the same problems lithium-ion batteries suffer. In their paper, they write: “…it is prudent to design potential recycling strategies such that future [all-solid-state battery] manufacturers can consider it as part of a sustainable production-to-recycling manufacturing process.”
For instance, better regulation is needed to encourage and enable recycling efforts, both at the level of governments and regulating bodies as well as at the manufacturer level.
In addition, more complete recycling of the whole battery, rather than just the electrodes as is currently done, would prevent loss of material and waste. Improved processing techniques would also benefit both the product and cycle—instead of completely breaking down materials during recycling, techniques to reduce the required processing steps would also reduce energy and processing costs, better preserve material integrity, and prevent material loss.
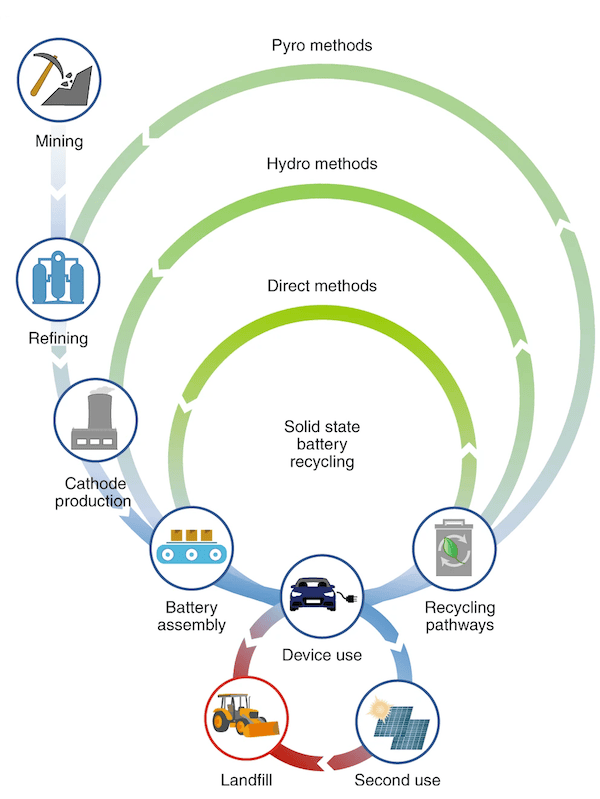
Lifecycle approach to recycling solid state batteries. Credit: Nature Nanotechnology
To improve the recyclability of all-solid-state batteries, multiple challenges remain to be addressed—similar to the situation in regard to current barriers to the batteries’ commercialization.
Together, however, solutions to these four challenges may provide the final push that all-solid-state batteries need to make our all-renewable energy future a reality.
As the authors conclude in the paper, “Nanotechnology itself may not be an all-encompassing silver bullet for every challenge faced by [all-solid-state batteries], however it is certainly becoming an enabler for deeper understanding of nanoscale phenomena, helping better design strategies that can translate into improvements in materials and cell level performance.”
The review paper, published in Nature Nanotechnology, is “From nanoscale interface characterization to sustainable energy storage using all-solid-state batteries” (DOI: 10.1038/s41565-020-0657-x).
Author
April Gocha
CTT Categories
- Energy
- Nanomaterials