[Image above] A drilling project at a marine structure in Portus Cosanus, Tuscany, in 2003 yielded Roman concrete samples that have revealed important insights into the durability of the ancient material. Credit: J.P. Oleson
For all our technological achievements and incredible advances, sometimes I wonder whether we’ve missed some important construction lessons from our ancestors.
Thousands of years ago, the Japanese already knew how to build structures that could withstand intense earthquakes.
And the Romans perfected concrete to allow them to build massive creations, such as the Pantheon or Colosseum. Considering how quickly modern concrete crumbles, cracks, and demands replacement, it’s impressive that so many Roman concrete structures still stand tall today.
The Romans weren’t just skilled at building concrete structures on land, however—they also excelled at building concrete harbor structures, such as piers and breakwaters.
While many of the concrete that shores up our shorelines rusts and crumbles in no time, some Roman concrete harbor structures still survive today, despite being steadily lapped by waves for the past 2,000 years.
Roman author and naturalist Pliny the Elder wrote in his book Naturalis Historia around A.D. 79 that concrete, “as soon as it comes into contact with the waves of the sea and is submerged, becomes a single stone mass, impregnable to the waves and every day stronger.”
So what did the Romans know about concrete that we don’t today?
The key, an international group of scientists recently found, is that Roman concrete evolves over time, actually getting stronger with age. That strength can be traced to the presence of a rare hydrothermal mineral—aluminous tobermorite (Al-tobermorite)—that forms as a result of complex chemical reactions within material.
As a result, Roman harbor concrete structures survive about two orders of magnitude longer than Portland-type cement seawater concrete structures, the authors write in their new paper, published in American Mineralogist.
“This paper is essentially a validation of Pliny’s observations,” Marie Jackson, a research associate professor of geology and geophysics at the University of Utah and author of the new paper, told me in a recent phone interview.
The key concrete-strengthening mineral, Al-tobermorite, forms crack-stopping fibers and plates within voids in the cement. Although Al-tobermorite isn’t found in conventional concrete, it occurs naturally in some volcanic rock and forms in materials that store nuclear and toxic wastes.
Al-tobermorite is rare because it normally forms at high temperatures—so how did it get into Roman concrete?
Using a suite of high-tech experimentation methods, including electron microscopy, X-ray microdiffraction, and Raman spectroscopy, the scientists revealed that the Romans didn’t initially put Al-tobermorite in their concrete—instead, the mineral formed over a slow and evolving timeline of chemical reactions with the seawater itself.
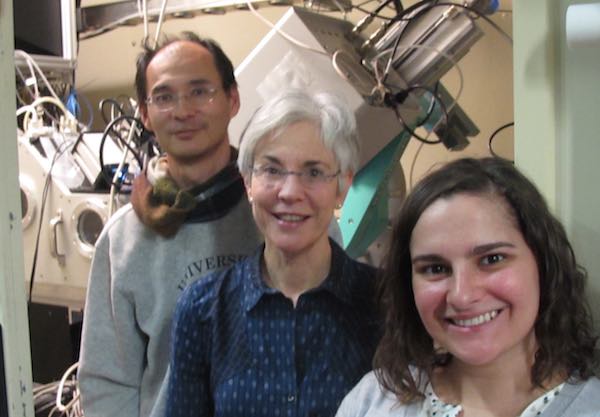
(Left to right) Nobumichi Tamura, Marie Jackson, and Camelia Stan at beamline 12.3.2 at the Advanced Light Source at Lawrence Berkeley National Laboratories in January 2017. Tamura and Stan are scientists at the Advanced Light Source. Credit: Marie Jackson
The Romans formed their concrete from a mixture of volcanic ash, lime, and seawater, which together form a mortar that they used to cement together larger chunks of volcanic rock. Initially, volcanic ash and lime mix together in what are called pozzolanic reactions, which form strong cementitious binding hydrates that hold the concrete together.
But lime is consumed in these reactions early on—previous research shows that lime is consumed within just a few decades for large concrete structures, and less time for smaller structures. And once the lime is gone, those pozzolanic reactions, which are thought to confer the strength to Roman concrete, cease.
So, at some point in the concrete’s timeline, a different process takes over.
“These materials have the ability to transform themselves over time at low temperature through a seawater corrosion process,” Jackson says.
The scientists’ new analyses indicate that as seawater infiltrates Roman concrete, it slowly dissolves small bits of minerals within the concrete. This dissolution makes this fluid more alkaline, allowing a shift in the types of reactions that occur within localized pockets within the concrete.
“My hypothesis is those fluids continue to percolate through the concrete, and when they come into very small areas, the fluids might get sealed in there as permeability decreases,” Jackson explains. “In those miniscule volumes, in situ reactions can generate very alkaline fluids—and that’s how the tobermorite might form.”
So instead of weakening the material, seawater dissolving minerals within the concrete actually strengthens it by allowing Al-tobermorite crystal plates and fibers to grow.
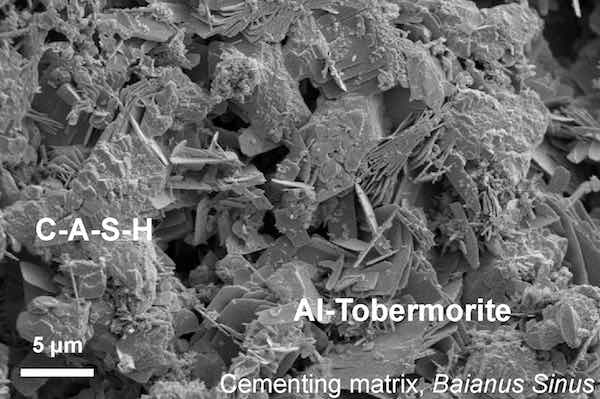
Micrograph showing the lumpy calcium-aluminum-silicate-hydrate (C-A-S-H) binder material that forms when volcanic ash, lime, and seawater mix. Platy crystals of Al-tobermorite have grown amongst the C-A-S-H in the cementing matrix. Credit: Marie Jackson
According to Jackson, the new work shows that different microenvironments form at very fine scales within the concrete—and these microenvironments have chemically dynamic histories that change over time.
Scientists can form Al-tobermorite relatively easily under high-temperature conditions in the lab—but the mineral evolves much more slowly at ambient temperatures, like what happens in Roman concrete.
So determining the details of those microenvironments’ histories is a challenging research problem to address.
The scientists don’t yet know how long it takes Al-tobermorite to form in Roman concrete. But they can’t simply mix up concrete formulations and wait for them to evolve over the next thousand years.
“These changes occur very quickly at elevated temperatures. So the question is what happens at lower temperatures? We can’t really do these experiments in the lab, so we’re going back to the geological record to better understand these processes,” Jackson says.
The team is turning to a geologic analogue where tobermorite naturally forms—the Surtsey underwater volcano in Iceland—to better understand the process of how these minerals evolve over time.
When I spoke with Jackson, she was in Iceland to lead a drilling project on the 50-year-old volcano, which is a UNESCO world heritage site. Scientists previously drilled cores from Surtsey when it was only 15 years old. Now, 35 years later, scientists including Jackson are back at the volcano to drill new cores.
Surtsey provides a unique natural laboratory for the scientists to study varying temperature scales and changes in fluids to analyze how these differences affect mineral evolution. By examining samples from Surtsey, the scientists can probe small-scale reactions within isolated geologic microenvironments to decipher the chronology of mineral growth.
By performing similar types of analyses as for the Roman concrete samples, the scientists hope that new cores from Surtsey will provide insight into how the alkaline reactions proceed and a better understanding of the timescale for Al-tobermorite formation at low temperatures.
And that will hopefully provide valuable insights that could be adapted to develop more durable concrete formulations for modern construction projects, which could become more important than ever considering the increasing threats of rising ocean levels.
And it all traces back to recipes and observations made thousands of years ago.
“It’s really been an inspiration for me—we have these records written down that have survived for 2,000 years, and we have these material records as well. And what they’re telling us is that these people were very good natural scientists,” Jackson says. “They had excellent capabilities for empirical observations—they were using a method based on science and knowledge, and it’s this careful observation and experimentation that led to these remarkably durable materials.”
The paper, published in American Mineralogist, is “Phillipsite and Al-tobermorite mineral cements produced through low-temperature water-rock reactions in Roman marine concrete” (DOI: 10.2138/am-2017-5993CCBY).
Author
April Gocha
CTT Categories
- Art & Archaeology
- Basic Science
- Cement
- Construction
- Material Innovations