[Image above] A lead-free piezoelectric part constructed with a direct-writing additive manufacturing method using water-based inks. Credit: Bo nan et al., Journal of the American Ceramic Society/Wiley
Lead has for years been “the linchpin of electronics manufacturing,” says Jack Geibig, president of Ecoform, in a 2005 article on the use of lead in electronics. “Without it, it’s difficult to achieve a proper electronic connection that is durable and reliable.”
Less than a year after that article’s publication, the Restriction of Hazardous Substances Directive (RoHS) took effect in 2006. This directive restricts the use of 10 hazardous substances in electronic and electrical equipment within member states of the European Union. Not surprisingly, one of those 10 substances is lead.
Even before RoHS came into effect, research into improving the performance and manufacture of lead-free electronic parts had already begun in the 1990s, in response to the increasing evidence of lead’s negative effects on the environment.
With the passage of RoHS in 2006, researchers now have many environmental and legal reasons to improve lead-free technology.
In recent years, the emergence of a new form of manufacturing—additive manufacturing—holds promise for being an effective way to create lead-free electronic parts, particularly for applications such as energy harvesting and ultrasonics that require complex geometries. Because additive manufacturing techniques build objects layer-by-layer, additive manufacturing can form complex shapes that are difficult or impossible to form using traditional manufacturing techniques.
In two recent articles appearing in the Journal of the American Ceramic Society, researchers used direct-writing additive manufacturing techniques to develop, test, and process inks containing barium titanate-based lead-free piezoelectric materials.
Getting the ink just right is critical to the success of direct-writing additive manufacturing techniques. Solids loading, binder/carrier type and formulation, and more, not only affect the viscoelastic properties of the ink, but also sintering parameters, along with density and performance of the sintered parts. Additionally, as in the case of the two recent papers, the binder system must not react with the barium titanate-based ceramic materials.
The first paper, published last November, is by researchers from the CICECO–Aveiro Institute of Materials at the University of Aveiro (Portugal) and a colleague from the University of Birmingham. They developed water-based inks by surface treating barium calcium zirconium titanate (BCZT) with aluminum dihydrogen phosphate (Al(H2PO4)3), a treatment method which has been demonstrated to reduce hydrolysis in water-based inks for aluminum nitride and magnesium alumina spinel.
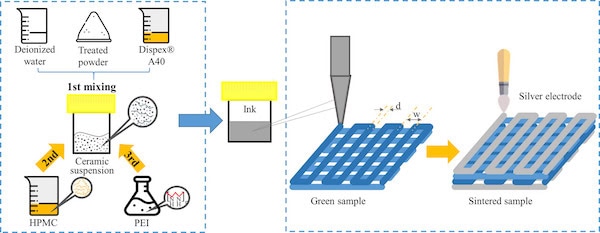
Schematic illustrating the formulation process of water-based ink and direct writing of macroporous ceramics. Credit: Bo nan et al., Journal of the American Ceramic Society/Wiley
The second paper, published in December, is by researchers from various departments at the University of Texas at El Paso. They used a mixed polymer/organic solvent system often employed for fabricating lithium-ion battery cathodes to prepare inks of barium titanate (BT).
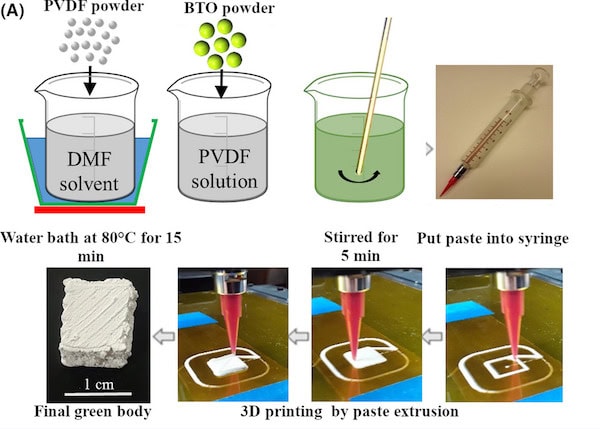
Schematic illustrating formulation process of polymer/solvent-based ink and direct writing of bulk piezoelectric parts. Credit: Hoejin Kim et al., Journal of the American Ceramic Society/Wiley
While the first paper explains in great detail the viscoelastic property development, the second paper focuses on the performance and properties during and after processing as a guide to the ink development.
The parts fabricated using the inks of these studies retained their shapes through the handling and firing stages, and they exhibited properties and performance on par with similar items fabricated using more traditional techniques.
Further possibilities of additive manufacturing and lead-free technologies will be discussed in more detail next week at Ceramics Expo, taking place April 30 and May 1 in Cleveland, Ohio.
The papers, published in Journal of the American Ceramic Society, are “Direct ink writing of macroporous lead‐free piezoelectric Ba0.85Ca0.15Zr0.1Ti0.9O3” (DOI: 10.1111/jace.16220) and “Fabrication of bulk piezoelectric and dielectric BaTiO3 ceramics using paste extrusion 3D printing technique” (DOI: 10.1111/jace.16242).
Membership has its privileges. ACerS members enjoy free access to all articles published in ACerS journals, so consider joining us today!
Author
Jonathon Foreman
CTT Categories
- Electronics
- Energy
- Manufacturing