[Image above] An artistic interpretation of cold sintering of ceramic particles (white) and polymer strands (green) using low heat to evaporate added water molecules (blue). Credit: Jennifer M. McCann, Materials Research Institute, The Pennsylvania State University
Decarbonizing manufacturing processes is the name of the game for industry in this day and age. On Tuesday, we looked at a possible way to do that in the cement industry using an electrolysis-based production process. Now, another paper brings attention to a method first reported about three years ago to decarbonize ceramic manufacturing—the cold sintering process (CSP).
CSP is a dual-process technology that significantly reduces energy use in ceramic manufacturing by combining heat, pressure, and water to lower temperatures required to produce ceramics from more than 1,000°C to less than 300°C.
CSP works by wetting ceramic powder with a few drops of water or acid solution to partially dissolve the powder particles’ solid surfaces, creating a liquid phase at particle interfaces. When temperature and pressure are applied, the solid particles rearrange and densify. Clusters of ions subsequently move away from where the particles are in contact, which aids diffusion, minimizes surface free energy, and allows the particles to pack tightly together.
The Pennsylvania State University researchers, led by ACerS Fellow Clive Randall, developed CSP in 2016. In a Penn State press release, Randall explains the benefits of the technology. “Not only is this a low temperature process (room temperature up to 200ºC), but we are also densifying some materials to over 95% of their theoretical density in 15 minutes,” he says.
Penn State researchers and other groups have continued to refine CSP over the past few years, including using the technology to create composites based on ceramic nanosheets.
In 2017, Randall coauthored an open-access article with more than three dozen other researchers on an NSF-sponsored workshop discussing the role of ceramic and glass science research in meeting societal challenges. In that paper, they mentioned CSP as a possible way to address ceramic processing challenges.
This year, Randall and other Penn State researchers coauthored another open-access article with researchers from the United Kingdom, Norway, and Malaysia focusing specifically on the advantages CSP offers to industry, both financially and environmentally.
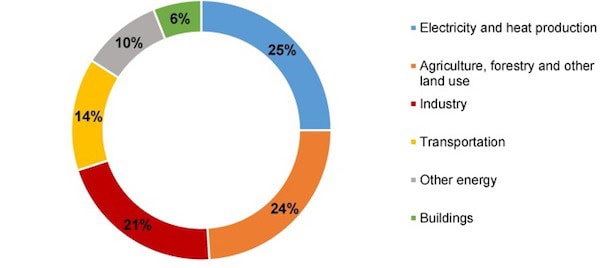
In 2010, 21% of economic activities that led to production of emissions and related pollutants was attributed to the industrial sector. CSP could help reduce the emissions in this sector. Credit: Ibn-Mohammed et al., Journal of the European Ceramic Society (CC BY 4.0)
“Despite the upsurge in research interests relating to developing low temperature sintering process, techno-economic analyses of CSP alongside existing sintering techniques such as traditional and spark plasma sintering (SPS) is lacking,” the researchers write in the paper. “Understanding the potential techno-economic impact of sintering techniques, manufacturing routes and materials composites is essential, … [and] This research need is addressed in this paper using a robust techno-economic analysis framework derived from ranking mechanisms of marginal abatement cost curve (MACC) and Pareto optimisation.”
The researchers considered three functional ceramics in their analysis: zinc oxide (ZnO), lead zirconate titanate (PZT), and barium titanate (BaTiO3). Data for the duration of sintering operations and manufacturing routes for each ceramic under different sintering techniques were obtained from published research articles; capital costs and power ratings of equipment for each sintering technique were estimated based on current market prices as well as a mix of literature and heuristic information.
“By using pounds per tonne of CO2 saved as a figure of merit to measure the cost-effectiveness of each sintering technique at the level of the laboratory, it was established that CSP is the most economically attractive sintering technique, indicating lower capital costs, best return on investment and a considerable reduction in CO2 emissions … even under projected mass production scenarios,” the researchers conclude.
The researchers do note that transitioning CSP from laboratory to industry faces some challenges, including requiring hugely different facilities and instrumentation as well as relevant property/performance validation. However, based on the results of this analysis, the researchers urge industry to consider adoption.
“We find that there are clear financial and environmental benefits if the ceramics industry was to take the cold sintering process out of labs and into commercial manufacturing,” Taofeeq Ibn-Mohammed, first author and assistant professor at the University of Warwick, says in a University of Warwick press release.
The open-access paper, published in Journal of the European Ceramic Society, is “Decarbonising ceramic manufacturing: A techno-economic analysis of energy efficient sintering technologies in the functional materials sector” (DOI: 10.1016/j.jeurceramsoc.2019.08.011).
Author
Lisa McDonald
CTT Categories
- Environment
- Manufacturing