[Image above] Credit: Walter, Flickr CC BY 2.0
It’s common knowledge that power plants are an ongoing source of pollution. A 2014 study found that power plants built in 2012 will spew out close to 19 billion tons of CO2 over their lifetimes, assuming an operating lifetime of 40 years. Called “commitment accounting,” the research, published in IOP Science, takes into account the entire total emissions of the plant’s life, rather than the annual emissions numbers typically reported.
That’s a lot of carbon dioxide.
Fortunately a research duo from Massachusetts Institute of Technology is thinking about all that CO2 as well. Postdoc Xiao-Yu Wu and Ronald C. Crane Professor of Mechanical Engineering Ahmed Ghoniem developed a method of passing carbon dioxide through a membrane made of lanthanum, calcium, and iron oxide. Only an oxygen molecule gets through, leaving carbon monoxide behind. This process could be used to convert CO2 emissions from power plants into fuel for vehicles, including planes, as well as chemical feedstocks for numerous products.
The carbon monoxide could be used as a fuel or as a component in liquid hydrocarbon fuels when combined with hydrogen and water, or other chemicals such as methanol, according to a news release on the MIT website.
The membrane’s unique crystalline perovskite structure lets only oxygen atoms through, says Wu in the release. And the process can only succeed if the oxygen flow through the membrane is continuous and temperatures are kept at up to 990o C (1,814o F).
To keep the oxygen flowing continuously, the duo used a stream of fuel such as hydrogen or methane—that draws oxygen atoms through the membrane without having to use pressure from a vacuum, which uses a lot of energy. But some energy is needed to keep the process going, and Wu suggests that could come from sources like solar energy or even from the power plant’s waste heat. And their process enables them to store heat as chemical energy for later use.
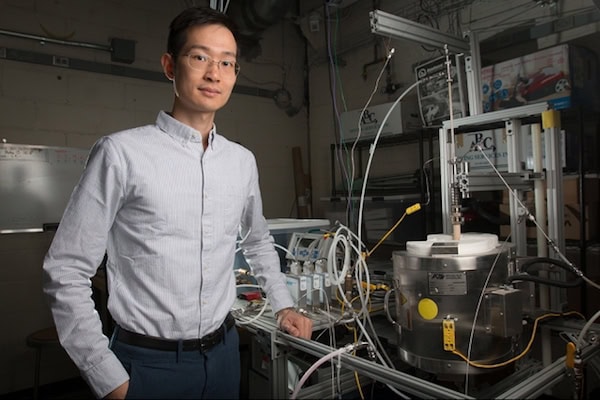
XiaoYu Wu pictured with the reactor his team used for the research. Credit: Tony Pulsone, MIT CC BY-NC-ND 3.0
Ghoniem and Wu say that the higher the CO2 concentration, the more efficient the process is—but it can work with virtually any level of CO2 concentration. Although they’ve already demonstrated success with their procedure, they note that they continue to explore ways of increasing oxygen flow rates, such as creating a membrane with different materials, adding a catalyst, or changing the surface geometry.
They are continuing to explore how to incorporate their membrane into reactors and tie it in to the fuel production system. Ghoniem and Wu are also looking at how to scale their process cost effectively.
Wu explains in the release that their method could be used in natural gas power plants where natural gas would play a dual role—one to generate electricity while capturing CO2, and the other for a fuel source from their membrane system. They would be able to mix hydrogen with carbon monoxide to make synthetic gas (syngas), such as methanol or ethylene—creating other products that would generate revenue for the plant.
Ultimately the process could eventually lower power plant emissions while saving energy and costs.
Their paper, published in ChemSusChem is “H2-assisted CO2 thermochemical reduction on La0.9Ca0.1FeO3-δ membranes: a kinetics study (DOI: 10.1002/cssc.201701372).
Did you find this article interesting? Subscribe to the Ceramic Tech Today newsletter to continue to read more articles about the latest news in the ceramic and glass industry! Visit this link to get started.
Author
Faye Oney
CTT Categories
- Basic Science
- Energy
- Environment
- Manufacturing
- Material Innovations
- Thermal management