[Image above] By treating wood using atomic layer deposition, Georgia Tech researchers found they could manage moisture content, mold growth, and thermal conductivity. Credit: Georgia Tech, YouTube
Last Friday, we discussed a few ways that different industries proactively counter material changes expected in application, for example, by preshrinking cotton or prestressing concrete. Another industry that proactively counters expected material changes on a daily basis is the lumber industry, with pressure-treated wood.
Wood has many desirable qualities that make it a great building material, including being strong, lightweight, and easily shaped with tools. However, wood has a major weakness—moisture.
“Virtually all problems with wood-based building materials are moisture problems,” a University of Massachusetts Amherst article on wood myths explains. “Peeling paint, rot, warp, cracks and general shrinkage are all related to water in wood.”
To proactively counter moisture-related problems, lumber suppliers put wood through a pressure treatment process, which involves forcing chemical preservatives into the wood to protect it against rot and attack by wood ingesting insects.
But rot-resistant does not necessarily mean water-resistant.
“Pressure treated wood still soaks and loses moisture,” the UMass Amherst article says. “And as a result, the wood moves, cracks, twists, bends, cups and virtually tears itself apart.”
There are a few other inconveniences to pressure treatment as well. Chromated copper arsenate (CCA) was the main chemical preservative used before 2003, the year the U.S. Environmental Protection Agency and lumber industry agreed to discontinue use of CCA in most residential construction because of potential exposure to arsenic. Since then, copper-based compounds such as alkaline copper quaternary, copper azole, and micronized copper azole are used more commonly, but the copper can lead to corrosion of screws and nails.
Additionally, because the pressure treatment process involves wetting the lumber, it must properly dry before use or risk warping—which can be a lengthy process. “In the winter time, we’re here in the Northwest, it gets pretty wet, it gets pretty cold, [the curing and drying] can take anywhere between one to two weeks,” Dennis McWhirter, sales manager at Exterior Wood, says in a video on the pressure treatment process.
Alternative wood treatment techniques, such as thermally modified wood, look to bypass some of the downsides to pressure treatment (e.g., they use no chemicals except water), but currently these techniques are more expensive. However, a new approach suggested by researchers at the Georgia Institute of Technology that addresses some of the downsides to pressure treatment could possibly scale to commodity goods manufacturing without a need for complicated engineering solutions.
Atomic layer deposition—from microelectronics to bulk wood
Atomic layer deposition (ALD) is a vapor phase technique for depositing a thin film onto a surface through self-limiting chemical reactions. Chemicals called precursors (or “reactants”) are deposited one at a time onto a surface, where they react—forming a monolayer of material—before the next precursor is deposited and reacts. In this way, a thin film forms layer by layer.
One of the biggest adopters of ALD is the microelectronics industry, especially since the transition to using high-k dielectrics for the transistor gate stack (Intel in particular introduced ALD into their mass production line in 2007). However, as the Georgia Tech researchers note, this technique could be useful in fields far different from microelectronics.
“For wood-based products, a single-cycle ALD process is in fact very similar to current pressure treatments that are carried out in high pressure or vacuum chambers,” the Georgia Tech researchers write in a paper on their research.
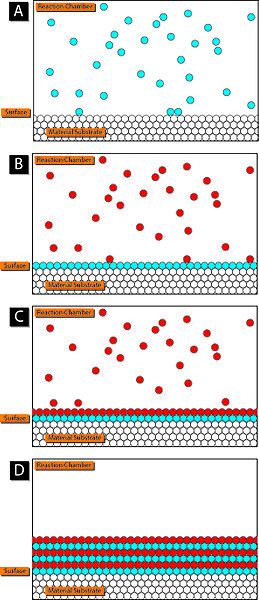
A schematic of the ALD process, in which two precursor chemicals are deposited sequentially layer by layer. Credit: Mcat chem446, Wikimedia (CC BY-SA 3.0)
However, unlike pressure treatment, the ALD process never requires wetting the wood (everything is in the gas phase), which means an extended drying period would not be required.
Georgia Tech assistant professor of materials science and engineering Mark Losego explains in an email that it is “pretty well known” that ALD of metal oxides on cellulosic materials leads to hydrophobicity, i.e., the property of being water repellant. So they were pretty sure the ALD process would make bulk wood lumber hydrophobic as well, “at least to some extent.”
Managing moisture content, mold growth, and thermal conductivity with ALD
The researchers used a single-cycle ALD process (1cy-ALD) to infuse blocks of pine, cedar, or poplar with subnanometer layers of three fairly benign metal oxides:
- Aluminum oxide (precursor: trimethylaluminum)
- Zinc oxide (precursor: diethylzinc)
- Titanium oxide (precursor: titanium tetrachloride)
Only one type of metal oxide was deposited on each block, so the efficacies could be tested separately.
To evaluate hydrophobicity, the researchers collected water contact angle measurements on the three types of wood species. Despite initial differences in hydrophilicity (attraction to water), “all lumber varieties show an increase in hydrophobicity after 1cy-ALD treatments, likely due to the metal oxide surface’s increased attraction of adventitious carbon, consistent with prior reports of other cellulosic materials,” the researchers write.
However, water contact angle measurements only really test the blocks’ surface properties. To more directly evaluate water repellency in the bulk of the wood, the researchers fully submerged the pine blocks in water to gravimetrically measure water uptake over time.
Of the three metal oxides, only titanium oxide prevented bulk uptake of water. “Hydrophobicity is especially notable in the 10 min timescale; untreated pine sorbs 40−50 wt% water, while the TiCl4-treated wood [titanium oxide coated] only gains 5−10 wt% water by mass,” they observe.
In a Georgia Tech press release, graduate student and lead author Shawn Gregory explains why the titanium oxide provided the best water resistance. “We hypothesize that this is likely because of how the precursor chemicals for titanium dioxide react less readily with the pore surfaces and therefore have an easier time penetrating deep within the pores of the wood,” he says.
Losego says they were also surprised to find the TiO2-coated pine demonstrated rot resistance. They realized this fact after leaving the blocks sitting in a humid environment for several months and witnessed no evidence of mold growth (in contrast to the untreated lumber, which developed significant green-black mold).
In the press release, Gregory says, “We suspect that this has something to do with its hydrophobic nature, although there could be other chemical effects associated with the new treatment process that could also be responsible. That’s something we would want to investigate in future research.”
There was one more important finding from the study—the treated wood blocks showed decreased thermal conductivity.
Perhaps surprisingly, Losego says thermal conductivity was the initial reason they were driven to investigate ALD of bulk wood. “We knew the thermal conductivity is affected by moisture content, so we thought that the ALD could help reduce thermal bridging in wood studs,” he says.
In home building, a lot of attention is given to insulating the cavities between structural components. However, a massive amount of thermal losses is caused by the wood studs themselves.
“Lumber treated with this new process [ALD] can be up to 30 percent less conductive, which could translate to a savings of as much as 2 million BTUs of energy per dwelling per year,” Shannon Yee, Georgia Tech associate professor in mechanical engineering and study co-author, says in the press release.
Losego says they plan to expand on this study in several ways, including trying to understand degradation better and determining whether the metal oxide plays a functional role in mold prevention. They also want to investigate the processing kinetics more to understand better the time and coating depth necessary to achieve desirable properties while minimizing precursor usage to optimize cost.
“Of course, this understanding of processing kinetics exists in the ALD microelectronic literature, but we are seeing the same behavior here in the wood, which is really elegant from a scientific perspective,” Losego adds.
The paper, published in Langmuir, is “Single-cycle atomic layer deposition on bulk wood lumber for managing moisture content, mold growth, and thermal conductivity” (DOI: 10.1021/acs.langmuir.9b03273).
Author
Lisa McDonald
CTT Categories
- Basic Science
- Construction
- Environment