[Image above] Thin (left) and thick films made of porous nanoparticles of calcium and silicate reacted differently under pressure as tested in a Rice University lab. Credit: Multiscale Materials Laboratory; Rice University
Porous particles are important in a host of materials and applications, including drug delivery, insulation, catalysis, chromatography, filler materials, construction materials, and—our favorite—ceramics. But, despite their importance and potential applications, the mechanical properties of such porous particles are often ignored.
Now, after collecting extensive data, researchers at Rice University (Houston, Texas) can definitively say that, when it comes to porous nanoparticles, size matters—and, in the process, they’re made some surprising discoveries about how size affects the materials’ intrinsic properties.
Using uniformly porous calcium-silicate nanoparticles with diameters ranging 150–550 nm and pore sizes of 2–4 nm, the scientists found that larger particles behave differently under pressure than smaller ones. Using a nanoindenter, they tested how assembled films and compacted pellets of the various-diameter nanoparticles held up under pressure.
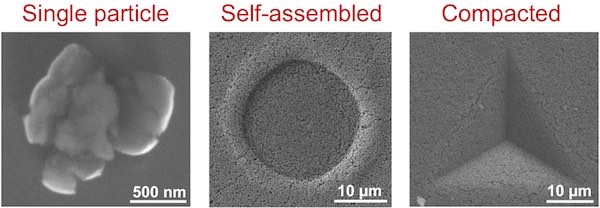
Rice University materials scientists tested structures made of calcium-silicate nanoparticles and found that particles go from brittle to ductile as they increase in size. The compressed single particle at left deformed under the pressure of a nanoindenter. At center and right, large particles did not crack under pressure. Credit: Multiscale Materials Laboratory; Rice University
The data, the result of more than 900 nanoindentation experiments, shows that self-assembled films of larger calcium-silicate nanoparticles are 120% tougher than those assembled from smaller particles of the same composition and porousness.
“This means that larger submicron calcium-silicate particles are tougher and more flexible compared with smaller ones, making them more damage-tolerant,” senior researcher Rouzbeh Shahsavari says in a Rice University news release.
Rouzbeh completed the study with graduate student Sung Hoon Hwang, who together also recently wrote an interesting article about innovative concretes in the most recent January/February 2018 issue of the ACerS Bulletin.
But hold up—when contemplating particle size, wouldn’t you expect that a material made up of smaller particles would actually be more ductile than one with a larger nanoparticle composition?
“Usually the common perception in nanomaterials is that smaller is better (such as in metallic systems), but our results were the opposite,” Shahsavari explains in an email. “This new knowledge can help to better create and use either individual version of these particles, for example for drug delivery—or their collected behavior, such as in self-healing applications and bone-tissue engineering.”
In addition to size, however, the scientists also showed that assembly of those nanoparticles matters, too.
The nanoparticle size effect they measured with self-assembled films disappeared when the researchers tested compacted samples of the nanoparticles, highlighting important intrinsic differences depending on how a material is prepared—even when it’s prepared from the same starting nanomaterial. That’s an important point for ceramic materials, which are often compacted from small, porous, particles.
Although the scientists only performed extensive experimentation on calcium-silicate nanoparticles, they think that the results are generalizable to other nanoparticles as well.
“The results can be helpful in generalizing to any porous particles materials where the relationship between three factors—particle size, pore size, and mechanical properties—are often not intuitive but very important,” Shahsavari writes in an email. “This interrelationship we found is akin to the role of ‘structure–property’ design maps in metallic systems or other material classes. Overall, what we found paves the path for discovering composition–structure–property design maps for porous inorganic materials and ceramics.”
Of course, all you need to add is water to get cement hydrate, aka calcium-silicate-hydrate (C-S-H)—the hydrated product largely responsible for concrete’s strength, and an area of expertise for Shahsavari and his lab—from calcium calcium-silicate particles. So these results might also have important implications for engineering stronger concretes, in addition to many other porous materials.
The paper, published in ACS Applied Materials & Interfaces, is “Intrinsic size effect in scaffolded porous calcium silicate particles and mechanical behavior of their self-assembled ensembles” (DOI: 10.1021/acsami.7b15803).
Did you find this article interesting? Subscribe to the Ceramic Tech Today newsletter to continue to read more articles about the latest news in the ceramic and glass industry! Visit this link to get started.
Author
April Gocha
CTT Categories
- Basic Science
- Nanomaterials