[Image above] Electrolysis could offer a way to produce emissions-free cement. Credit: Felice Frankel, MIT
An increasingly negative public opinion of plastic showcases the fight against climate change these past few years. Bans of plastic straws, plastic bags, and other single-use plastics all take center stage in many environmental campaigns.
Yet for all the ire plastics garner, public outrage is relatively absent in relation to the most widely used man-made material in existence—concrete.
Concrete is second only to water as the most-consumed resource on the planet, and it boasts a significant carbon footprint because of cement, the key ingredient in concrete. The production of more than 4 billion tonnes of cement each year account for about 8% of the world’s carbon dioxide (CO2) emissions, according to a report by think tank Chatham House.
To tackle cement’s emission problem, many research groups investigate replacing cement with alternative supplementary cementitious materials, such as fly ash binder, or develop devices that capture the emitted CO2. However, gaining acceptance for cement that contains alternative cementitious materials could face an uphill battle from builders reluctant to try new, relatively untested materials. And CO2 emitted from conventional cement plants is highly contaminated with nitrogen oxides, sulfur oxides, carbon monoxide, and other materials, which makes cleaning and reusing the CO2 impractical.
Another way to tackle carbon emissions from cement production is to replace the emission-heavy steps of the manufacturing process with alternative techniques.
Ordinary Portland cement is made by grinding calcium carbonate (CaCO3, generally limestone) and then cooking it with sand and clay at high heat, produced by burning coal. The cooking process decarbonizes CaCO3 and produces calcium oxide (CaO) and CO2. The CaO is then reacted with silica (SiO2) to produce alite, the major mineral phase in Portland cement.
Two parts of the process are responsible for CO2 production: burning coal and heating CaCO3.
One way to reduce emissions is to replace coal with a lower-carbon fuel source to produce heat. For example, a large cement factory in Ras al-Khaimah in the United Arab Emirates burns camel dung to power cement ovens.
Another way to reduce emissions is to heat CaCO3 using renewable sources—and such a process is what Massachusetts Institute of Technology (MIT) researchers investigated in a recent paper.
“Our reactor takes advantage of the inherent pH gradients in an electrolysis cell to carry out CaCO3 decarbonation and Ca(OH)2 precipitation and collection,” the researchers write in the paper.
An electrolyzer is a basic water-splitting tool that consists of two electrodes connected to a battery. When the electrodes are placed in a glass of water, the electricity splits water molecules into their constituent atoms, which can be seen by the production of oxygen bubbles from one electrode and hydrogen bubbles from the other. Importantly, the oxygen-evolving electrode produces acid while the hydrogen-evolving electrode produces a base.
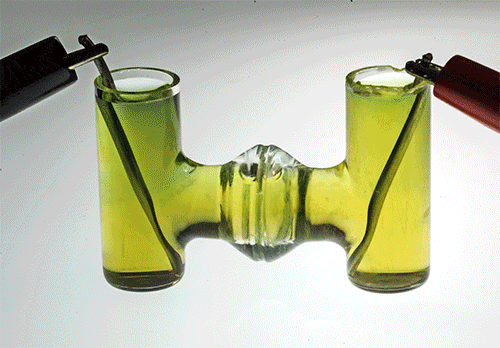
In a demonstration of the basic chemical reactions used in the new process, electrolysis takes place in neutral water. Dyes show how acid (pink) and base (purple) are produced at the positive and negative electrodes. A variation of this process can be used to convert calcium carbonate (CaCO3) into calcium hydroxide [Ca(OH)2]. Credit: Felice Frankel, MIT
The researchers, led by ACerS Fellow and Kyocera Professor of Materials Science and Engineering Yet-Ming Chiang and postdoc Leah Ellis, dissolved pulverized CaCO3 in the acid at one electrode and calcium hydroxide [Ca(OH)2] precipitated out as a solid at the other one. Though Ca(OH)2 is slightly different from CaO, the material produced in a conventional cement manufacturing process, Ca(OH)2 “readily reacts with silica to form alite while giving off only water,” Chiang explains in an email.
In addition to Ca(OH)2, dissolving CaCO3 in acid produced a stream of O2/CO2 gas at that electrode, while a concentrated hydrogen gas stream was released from the other one.
In the paper, the researchers explain how these gas streams could be harnessed for other applications. “Since here the CO2 is delivered in a highly concentrated form mixed only with O2 (and some H2O vapor), direct capture using the same simple compression processes now used for purified and concentrated CO2, could be used,” they explain. That means the CO2 could be economically captured and reused in various applications, including synthetic liquid fuel, enhanced oil recovery, and even carbonated beverages.
Additionally, the hydrogen could also be captured and reused to support the cement process. “It could be directly combusted to provide heat or electric power back to the cement operation, or the H2 and O2/CO2 gas streams could supply a fuel cell that generates on-site electricity to power the electrochemical reactor or other plant operations such as grinding, mixing, and handling,” the researchers write.
Ultimately, “These results suggest a pathway to cost-competitive emissionless cement manufacturing wherein all energy is supplied by renewable electricity,” they conclude.
Chiang says they are currently designing and testing a scalable version of the electrochemical reactor and studying the reaction product under various operating conditions. More broadly, they are analyzing the scalability of producing cement electrochemically.
“While the techno-economics may or may not favor large plants like today’s cement plants, which on average produces nearly a million tons of cement per year (in the U.S.), in aggregate the throughput of plants must reach similar scale in order to make an impact in decarbonizing this industry,” he says.
They are also considering other ways to use the Ca(OH)2 without further thermal processing, including emission-free pozzolanic cements, nonhydraulic lime-based cements, and supplementary cementitious materials.
The paper, published in Proceedings of the National Academy of Sciences of the United States of America, is “Toward electrochemical synthesis of cement—An electrolyzer-based process for decarbonating CaCO3 while producing useful gas streams” (DOI: 10.1073/pnas.1821673116).
Author
Lisa McDonald
CTT Categories
- Cement