[Image above] In continuous steel casting, ceramic powders help keep the liquid metal from oxidizing. Could potassium carbonate serve as an alternative and less expensive material from which to make powders? Credit: Primetals Technologies, YouTube
If I could have a superpower, I think being able to read any language would be pretty darn cool. So much research is published every day in non-English journals, but because I am monolingual, I only cover research that is written about in English.
Imagine my excitement, then, when I got my hands on an issue of Taikabutsu Overseas, which is the English translation for the journal Taikabutsu (耐火物), or Journal of the Technical Association of Refractories, Japan. Charles Semler, an ACerS Fellow and founder of refractories consultant company Semler Materials Services, is the international adviser for the journal, which features translations of articles previously published in Taikabutsu.
The translated articles give me an opportunity to cover refractories research that I otherwise could not. So without further ado, today’s research comes from a translated article in Volume 40, Issue 2 of Taikabutsu Overseas (pages 72–75), which originally appeared in the January 2019 issue of Taikabutsu on page 9.
Ceramics in continuous steel casting
When we talk about ceramics used in steel production, we rarely take the time to explicitly emphasize that there are many methods for casting steel. Of these methods, continuous steel casting is used in about 55% of the world’s liquid steel production, according to the Encyclopædia Britannica.
In continuous steel casting, liquid steel is poured from a furnace ladle through a small, refractory-lined distributer called a tundish and into the mold, where the metal cools and solidifies into its final form.
Ceramics, unsurprisingly, are used to line the ladle, tundish, and mold to protect against corrosion and decomposition. However, ceramics also are used in the continuous casting process in the form of powders spread on top of the liquid metal.
“The liquid steel must be protected from exposure to air: if not, then oxygen will react to form detrimental oxide inclusions in the steel,” explains an article by TA Instruments. Thus, special powders are continuously fed on the surface of the liquid metal during casting to prevent this oxidation from occurring.
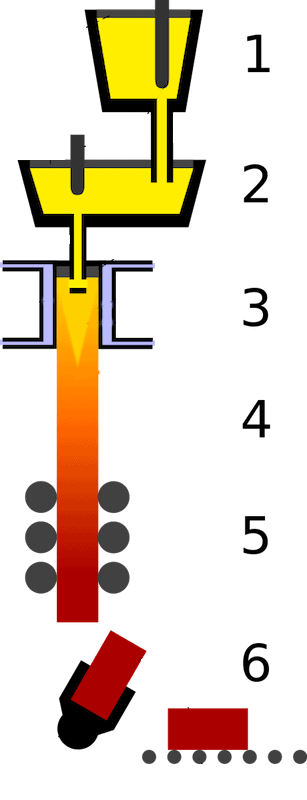
Illustration of the continuous steel casting process. 1) Ladle. 2) Tundish. 3) Casting mold. 4) Secondary cooling. 5) Rolling. 6) Cutting and transportation. Credit: Zielu20, Wikimedia (CC BY-SA 3.0)
These powders mainly consist of calcium oxide (CaO) and silicon dioxide (SiO2). The powder’s melting point and viscosity are adjusted using flux compositions such as sodium oxide, lithium oxide, and fluorine.
Unfortunately, “the choice of flux is narrow due to the soaring price of Li2O raw material,” two researchers write in a recent article. Their solution? To examine potassium oxide (K2O), another alkali metal oxide, as an alternative flux composition.
Exploring the potential of potassium carbonate as flux
The researchers are Masanori Okada and Junya Ito from Shinagawa Refractories Co. in Okayama, Japan. In their study, they chose to use potassium carbonate as a source of potassium oxide because it “is easy to use without limits for composition design.”
However, potassium carbonate is known for deliquescence, which is the tendency of a solid to absorb moisture from the air and dissolve in it. Such a property is detrimental in steel casting because “if the raw material absorbs moisture in the production process in the factory, it will solidify in the raw material hopper or adhere to production facilities such as mixers or belt conveyors, which impedes productivity.”
To prevent deliquescence, Okada and Ito investigated whether potassium carbonate could be converted to a stable mineral by mixing and heating it with other raw materials used in casting powder. Specifically, they investigated four commonly used casting powder materials—silica, calcium carbonate, Portland cement, and alumina—as possibilities.
They mixed the potassium carbonate with each raw material at a weight ratio of 1:1 and then heated the mixture in an electric furnace at 800°C for 30 minutes. After the samples were removed from the furnace and left in the atmosphere, the researchers measured weight change with elapsed time.
The samples mixed and heated with silica, Portland cement, and alumina all showed a large weight increase and were wet after nine days, indicating that deliquescence occurred. However, the sample mixed with calcium carbonate showed a small weight increase and stayed dry, so the researchers focused on this composition.
The researchers believe that deliquescence was prevented because a new crystal structure formed when the potassium carbonate and calcium carbonate combined, namely K2Ca(CO3)2—and they confirmed the existence of this crystal structure in the fired sample using XRD analysis.
The rest of the article mainly details their attempts to identify the best way to manufacture K2Ca(CO3)2, including by modifying melting temperature and weight ratio. They tested the resulting powder by throwing it on hot molten metal at 1,500°C, and the test showed “no problem of moisture absorption and exhibited good melt behavior.”
In the conclusion, they close by stating, “Since the only component other than K2O in this material is CaO, which is the main component of mold powder and tundish powder, K2Ca(CO3)2 is considered to be a solution for adding K2O to the composition of mold powder and tundish powder.”
The paper, published in Journal of the Technical Association of Refractories, Japan, is “Prevention of potassium carbonate deliquescence.” (Original title: 炭酸カリウムの潮解抑制. Translated from Taikabutsu, January 2019, pg. 9.)
Author
Lisa McDonald
CTT Categories
- Refractories