[Image above] Credit: yasin hm, Unsplash
Among the many things that COVID-19 revealed about how our society operates, the role of refractories as an essential industry is one that caught several governments off guard at the beginning of the pandemic.
Refractories are ceramic materials that are essential for all high-temperature industrial processes because they provide mechanical strength, protection against corrosion, and thermal insulation. Yet some governments did not initially designate refractory companies as essential businesses, and so the refractory industry quickly set about informing policymakers of their importance.
Researchers are constantly investigating ways to develop longer-lasting refractories to improve the industry’s sustainability and cost effectiveness. And one part of the manufacturing process that often receives attention is the binder.
Many monolithic refractories are created by mixing ceramic particles with a binder, or a material that holds other materials together to form a cohesive whole. Choosing a binder takes careful consideration because it can “decisively influence the chemical composition within the ceramic body composition during setting, aging and firing,” researchers explain in a recent open-access paper.
The researchers come from the University of Koblenz-Landau in Germany. In their paper, they evaluated the influence that several types of binders have on the mechanical, chemical, and thermal properties of monolithic refractories to develop “a fundamental understanding of bonding mechanism and a targeted use of binders.”
Bonding systems and binder types
They begin by explaining that bonding systems for refractory applications can be classified as either cold or hot bonding. In hot bonding, a bonding phase develops during the sintering processes of the ceramic particles at high temperatures—in other words, you do not need to add a binder into a hot bonding system. In contrast, cold bonding systems always require the addition of a binder.
Binders in cold bonding systems are classified as either organic, hydraulic, or chemical binders. Organic binders are mainly applied as temporary binders that decompose during the firing process, while the bonding effect of hydraulic binders is based on the formation of interlocking hydrate phases.
Inorganic binders are the ones most likely to influence the chemical composition within the ceramic body. Their bonding effect is based on chemical reactions either with ceramic particles or within the binder itself. Thus, the researchers focused on inorganic binders in the rest of the paper.
Inorganic binders: Phosphates and silicates
Phosphates and silicates are commonly used as inorganic binders because these materials are network formers, i.e., they are essential in facilitating the formation of a material’s structure.
The phosphate bonding mechanism generally consists of three reaction steps:
- Bonding is initiated by an acid–base reaction between the phosphates and ceramic oxides, which results in formation of network-forming phosphates.
- The bonding effect is increased by temperature treatment below 800°C due to condensation and polymerization reactions of the phosphates.
- High-temperature reactions above 800°C result in formation of sintered phosphates with higher crystallinity. Simultaneously, sintering of ceramic oxides takes places, causing the phosphate bonding to merge into the ceramic bond, thus achieving permanent bonding.
Only certain phosphates, such as aluminum phosphates, can generate the bonding effect. Inert phosphates such as calcium or magnesium phosphates do not react with the ceramic oxides and so cannot generate bonding networks.
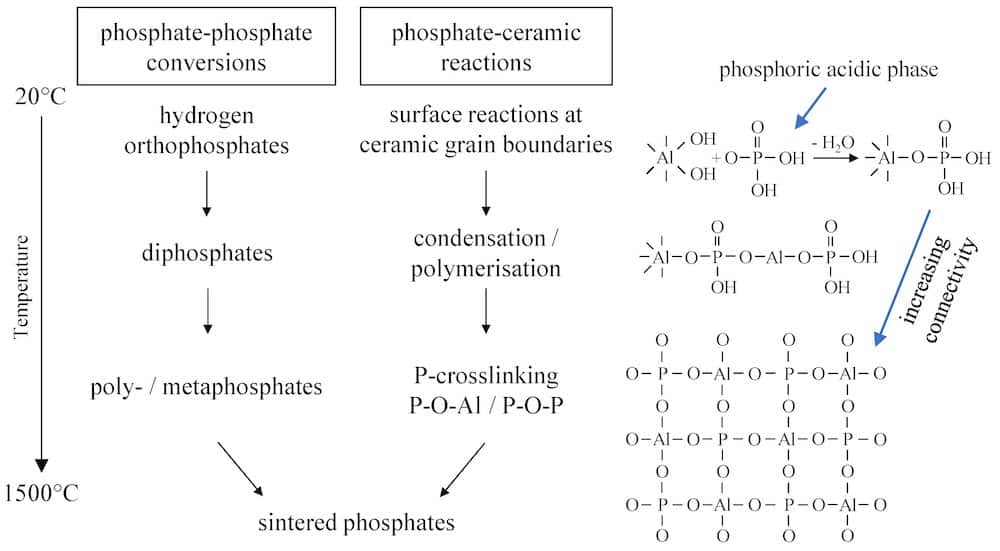
Overview of the bonding mechanism of inorganic phosphate binders in an alumina-based ceramic application as a function of temperature. Credit: Hopp et al., Materials (CC BY 4.0)
The main silicate inorganic binders used for refractory applications are water glasses, i.e., sodium or potassium silicates that are water-soluble. These water glasses are applied either as a colloidal solution or as a dry powder.
Setting of the water glass binders can be initiated by different reaction routes, but the simplest setting is activated by heat. In this case, thermal dehydration of the water glass system leads to polycondensation, which forms an amorphous 3D binder framework.
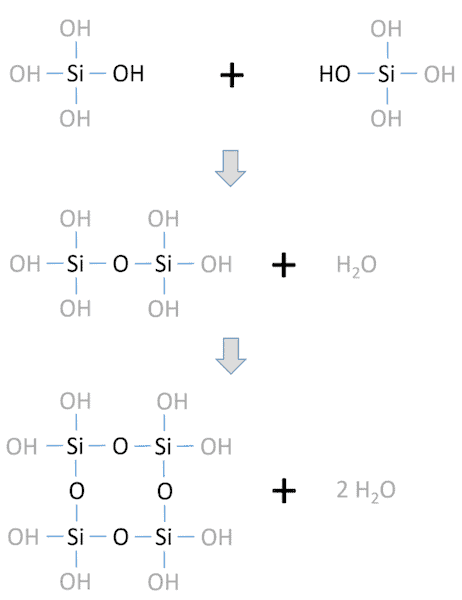
Overview of the network formation in silicate systems due to the polycondensation of silanol groups to siloxanes. Credit: Hopp et al., Materials (CC BY 4.0)
The researchers spend a significant portion of the paper looking deeply at how chemical setting and strength development occur during these bonding processes. They use a combination of complementary X-ray powder diffraction and nuclear magnetic resonance spectroscopy analyses along with macroscopic property investigations (e.g., cold bending strength measurements and acid resistance).
They conclude that the correlation they observed “allows extracting of the crucial steps for a selective and systematical range of raw material–binder combinations to adjust materials with tailored properties,” in contrast to the usual method of trial and error. Thus, this research “leads to a more efficient approach in material design,” they write.
The open-access paper, published in Materials, is “Structure–property functions of inorganic chemical binders for refractories” (DOI: 10.3390/ma14164636).
Author
Lisa McDonald
CTT Categories
- Basic Science
- Manufacturing
- Refractories