[Image above] Credit: Nick Youngson, Alpha Stock Images (CC BY-SA 3.0)
In recent years, the U.S. government has taken steps, such as here and here, to phase out the use of toxic per- and poly-fluoroalkyl substances (PFAS) in industrial operations and consumer products. Yet PFAS are just the tip of a much larger iceberg of hazardous material synthesis practices that underly almost every industry, from pharmaceuticals to food to textiles.
In the mid- to late-1990s, a set of concepts coalesced to form the field of green chemistry, which focuses on minimizing or eliminating the use and generation of hazardous substances during materials processing. In 2005, this field gained a boost in recognition when the Nobel Prize in chemistry was awarded to researchers who pioneered metathesis, a technique that allows for more efficient and environmentally friendlier chemical reactions.
In the past few years, government policies and consumer advocacy have driven corporations to become more conscious of the impact their processes have on the environment. By using the 12 defined principles of green chemistry, these companies have implemented more sustainable practices in many sectors, including
- Pharmaceuticals and biotechnology,
- Fine and specialty chemicals,
- Polymers and plastics,
- Energy and fuels,
- Materials science,
- Personal care,
- Agriculture,
- Food and flavors, and
- Textiles and dyes.
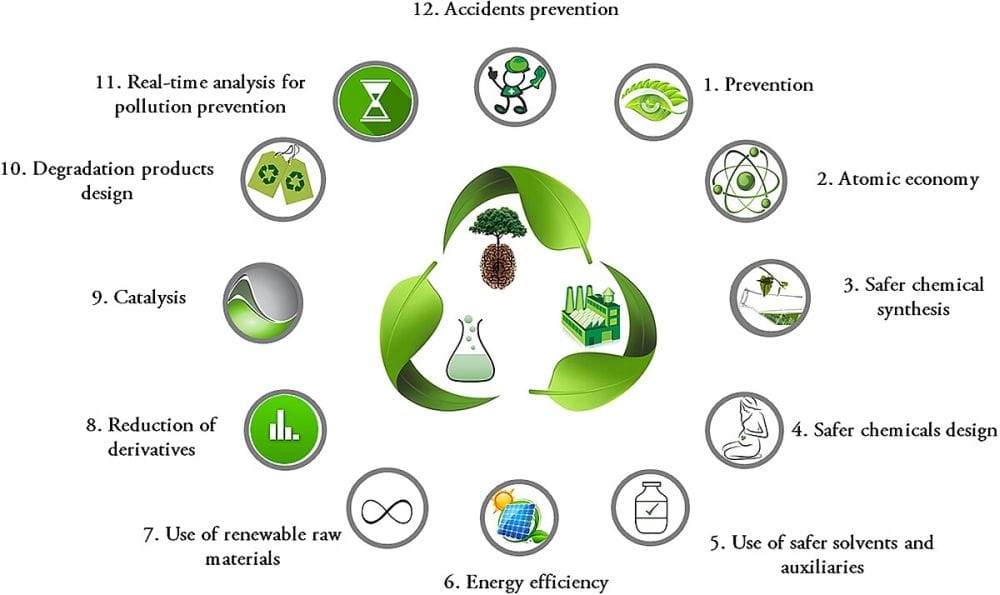
Twelve principles of green chemistry proposed by Paul Anastas and John Warner. Credit: Goyal et al., Wikimedia (CC BY 4.0)
Versatility and potential of ceramics in green chemistry applications
Ceramic production has also benefited from the adoption of green chemistry principles. For example, researchers have found that many ceramics can be produced from renewable, recyclable, or waste-derived feedstocks. On the processing side, supercritical fluids, which are less toxic that traditional solvents, can be used in ceramic production. Additionally, researchers are looking at ways to electrify cement production, which will dramatically reduce its environmental impact.
On the other hand, ceramic materials also contribute directly to many green chemistry processes by serving as catalysts, sorbents and separation membranes, energy storage and conversion materials, and composites and coatings, as described in more detail below. In each case, ceramic nanoparticles expand the range of applications with their improved mechanical strength, nontoxicity, and biocompatibility.
Ceramics as catalysts
Ceramic materials can be engineered to function as efficient and selective catalysts with high surface areas. Ceramic catalyst materials reduce the reliance on chemical catalysts, which vary in toxicity and may not be reusable.
The most well-known example of ceramic materials in catalysis involves the removal of harmful gases that result from combustion reactions. Specifically, catalytic converters, which were originally developed by Corning Incorporated, became standard in vehicles in the United States and eventually around the world after the U.S. Environmental Protection Agency introduced air-quality standards. Smokestack scrubbers are another pollution-control measure that contributes to improved air quality.
Modern automobile catalytic converters contain a reduction and an oxidation catalyst that remove nitrogen oxides, carbon monoxides, and unburned hydrocarbons. The high surface area created by a network of honeycomb-shaped chambers of cordierite created a stable and nonreactive surface for the coating of precious metal catalysts. Unfortunately, these precious metals, such as platinum, palladium, and rhodium, make the converters attractive targets of theft.
Ceramic materials are transparent to microwaves, making them excellent substrates for microwave-assisted solvent-free reactions, which can replace more energy-intensive forms of heating or drying. Additionally, the corrosion resistance of ceramic materials makes them ideal vessels for use in these reactions.
Cylinders of silicon carbide can be placed in vials with the compounds to be heated, and when subjected to microwaves they quickly heat up, allowing reaction temperatures of up to 300°C with no degradation of the cylinder. The cylinders do not react and can be washed and reused indefinitely. Some research has also been conducted using silicon carbide reaction vessels.
Ceramic materials have also shown promise as replacements for metal catalysts in the hydrogen evolution reaction. Scaling up of this application could lead to much greater use of hydrogen as a renewable energy source.
Ceramics in sorption and separation
Another green chemistry application of ceramics is their use as sorption and separation materials. In general, polymer membranes are the standard material used for water treatment and desalination. Fabricating polymer membranes often involves toxic solvents and solvent waste, however. Additionally, the harsh operating conditions require frequent replacement of the polymer membranes (every 3–10 years).
In contrast, ceramic membranes can tolerate repeated cleaning, higher fluxes, and higher operating temperatures. These materials are less susceptible to fouling and have longer lifespans of up to 20 years.
Researchers have explored using ceramic membranes made of graphene or boron nitride nanomaterials to treat semiconductor wastewater, which is a growing concern as governments around the world scramble to manufacture these electronic components domestically.
More recently, the presence of PFAS chemicals in drinking water has been a concern. Ceramic membranes and monoliths, such as this one recently described on CTT, can be used to absorb or adsorb these difficult-to-remove chemicals, increasing the possibility of successful remediation.
Additionally, ceramic nanoparticles are being investigated for use in pollution reduction, particularly for removing heavy metals, dyes, or other organic compounds from water. But it is currently difficult to scale up applications of nanoparticles, so this technology will take time to develop.
Ceramics in energy storage and conversion
As described in a CTT post last month, ceramic–polymer composites are attracting attention for energy storage and conversion. They are used as electrolytes in fuel cells and batteries and are widely used in solar energy production.
Also, ceramic membranes are not just useful for pollution reduction, as described in the section above. They can be used in the energy sector to separate hydrogen from natural gas so it can be used as fuel.
Sometimes, green chemistry is facilitated by changing the energy inputs to a more sustainable source. Sourcing renewable energy for heat or converting chemical energy to power are additional ways to bring green chemistry to manufacturing processes. Advanced ceramic materials, such as composites and coatings, have roles to play in these processes.
Ceramic composites and coatings
The mechanical strength, thermal stability, and chemical stability of ceramic-based composites and coatings are advantageous in chemical processes where extremely high temperatures and corrosive environments are common.
Recently, firing of ceramics using hydrogen fuel has gained attention in various sectors because its combustion only produces water vapor, among other environmental benefits. Hydrogen combustion for other purposes requires ceramic materials that can withstand the higher temperature compared to gasoline combustion.
The hydrophobic nature of ceramic coatings makes them resistant to dirt or chemical buildup, giving them antifouling capabilities. Today, ceramic coatings have consumer applications as clear coats for cars, in exterior paint, and as protective coatings for appliances and countertops. These coatings provide color stability, dirt and damage resistance, and insulation.
Advancing green chemistry with ceramics
Green chemistry approaches to industrial processing are becoming mainstream, and ceramics hold enormous potential for making these approaches practical and cost effective. The growing importance of ceramic materials in sustainable technologies, and the growing awareness that green chemistry is not only good for the Earth but also good for the bottom line, is exciting to me. Continued innovation in ceramic materials will only increase the ways in which green chemistry can flourish in all manufacturing fields.
If you are interested in learning more about this topic, please consider joining me next month at the Materials Science and Technology (MS&T) conference in Pittsburgh, Pa., to hear the plenary lecture by Julie Schoenung on “Saving the Planet through Sustainability-Informed Selection, Design and Discovery of Materials.” I hope to see you there!
Further reading
Keane, M.A., “Ceramics for catalysis,” Journal of Materials Science 2003, 38, 4661–4675.
Author
Becky Stewart
CTT Categories
- Education
- Environment