[Image above] Credit: U.S. Department of Energy; YouTube
I must have military on the mind this week. Yesterday I wrote about what the U.S. Army Research Lab is up to. Today we look at what the U.S. Navy is doing in the way of research. And it’s quite huge—literally.
We’ve reported on 3-D printing, or additive manufacturing, many times on Ceramic Tech Today. Many of the 3-D printing processes we’ve written about are conducted in small research labs using sample sizes that are no bigger than the average laboratory table (except for maybe this or this).
However, the U.S. Navy never does anything small. In a collaboration between Oak Ridge National Laboratory (ORNL) and the Navy’s Disruptive Technology Lab, researchers created a prototype of a submersible hull on a giant 3-D printer. Measuring 30 feet long and 4.5 feet in diameter, the hull is made up of six carbon fiber composite sections.
According to a Department of Energy article, the research team had a timeline of four weeks to complete the project after a week of training on a humongous 3-D printer called the Big Area Additive Manufacturing, or BAAM. BAAM is an industrial-sized printer developed by ORNL and Cincinnati Incorporated, which manufactures the printer.
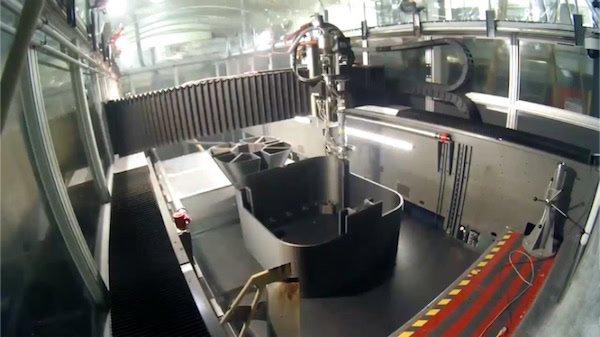
BAAM printer in action. Credit: U.S. Department of Energy
And a 3-D printing machine this size was just what the Navy needed to build its Optionally Manned Technology Demonstrator (OMTD) prototype. Because BAAM doesn’t need to take lunch, coffee, or smoke breaks, it can work 24/7 and has already saved the Navy 90% in production costs.
The DOE says it normally takes 3–5 months to build a submarine hull, at a cost of $600,000–$800,000. But the team built the OMTD prototype in just a few days, at a cost of around $60,000—saving not only time and money, but energy required to create it. The submersible hull currently represents the Navy’s largest 3-D printed asset.
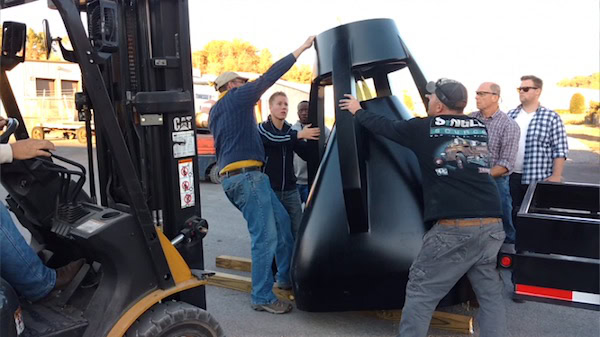
Credit: U.S. Department of Energy
“ORNL and the Navy saw this is as an opportunity to bring together their resources and expertise in a partnership with the potential to revolutionize manufacturing in the defense sector,” the DOE article says.
Another OMTD on the horizon
The next step for the project is to build a waterproof submersible and test it at the Navy’s research facility at Carderock, in the same harsh conditions that a submarine would normally encounter in the ocean. According to the DOE article, the Navy plans to create a fleet of prototypes in 2019.
Watch the video below to see how BAAM prints a submersible hull.
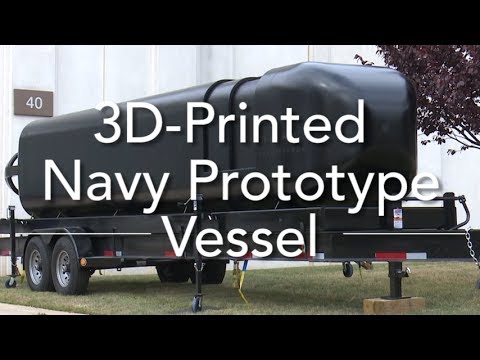
Credit: U.S. Department of Energy; YouTube
Author
Faye Oney
CTT Categories
- Manufacturing
- Market Insights
- Transportation
Spotlight Categories
- Member Highlights