[Image above] Studies on reducing viscosity of silicon carbide slurries help manufacturers fabricate dense, complex-shaped items—imagine the benefits if such studies’ data was freely available and could be readily compared! Credit: Xu et al., International Journal of Applied Ceramic Technology
For those researching high temperature ceramics, particularly refractory ceramics and silicon carbides, the March/April issue of International Journal of Applied Ceramic Technology is a must read. From additive manufacturing to low-cost raw materials to in-situ performance measurements, all readers should be able to learn something new about this important class of materials.
Silicon carbide—with low-cost raw materials, high hardness, chemical inertness, oxidation and temperature resistance, electrical and thermal conductivities, and many other favorable properties—is used in many applications, including armor, filters, electrical components, and high-temperature structural and protection components. But some of these favorable properties lead to processing challenges, especially for fabricating dense, complex-shaped items.
One key to fabricating dense ceramics is producing dense green bodies prior to sintering. Silicon carbide is amenable to colloidal processing methods, such as net-shape casting. A significant challenge to colloidal processing is the preparation of slurries that have both high solids loading and low viscosity, which are seemingly contradictory parameters.
It is well documented that oxidation on the surface of SiC reduces agglomeration and thus helps reduce viscosity of highly loaded slurries. The pursuit of further improvement is the topic of two articles in the latest ACT issue, one from researchers in South Korea and the other from researchers in China.
The main pursuit of the paper by Vu et al. is net-shape processing using nanoscale SiC, both alone and in combination with micron-sized powders. All powders were oxidized in air at 800–850°C. Their work resulted in viscosities as low as 429 mPa*s for 68% (by volume) solids loading. The dried green test samples formed by this powder were 76% dense, which is significantly higher than the 58% density achieved through cold isostatic pressing of the same powder (75% nanoscale powder, 25% with a median particle size (d50) of 10 microns).
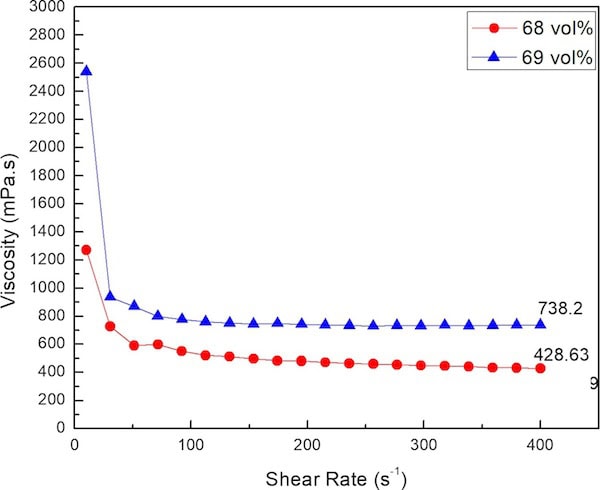
Viscosities of slurries containing different SiC (75% nanopowder/25% 10-micron powder) solid loadings. Credit: Vu et al., International Journal of Applied Ceramic Technology
These results are impressive. However, the researchers fabricated the nanoscale SiC particles from 99.4% pure silicon nanoscale powder, which is a much more expensive raw material than the silica used in commercial SiC processing. And low-cost commercial SiC powder (d50 2 microns) is the starting material for the paper by Gao et al.
Slurries made using untreated commercial SiC tend to have relatively high viscosities, even though the particle surfaces contain silica. The researchers found that oxidation by calcination in air (750°C) did not alter the viscosity, which is counter to other studies. These researchers found slurries made with the SiC washed in hydrofluoric acid (HF) have significantly lower viscosities. The HF, they determined, removes the silica coating along with surface impurities, such as aluminum, calcium, iron, manganese, and sodium.
Their research focused on determining whether the silica or the impurities were the greater influence on the slurry viscosity. They used hydrochloric acid washing and other methods to determine that removing impurities has the larger positive effect on viscosity. They also showed that oxidation does reduce the viscosity, though to a much smaller extent. In the end, they achieved viscosities as low as 16 mPa*s for a slurry with 43% solids loading.
These results leave me with many questions. Would acid-washing the lab-prepared SiC improve the performance of the slurries? Would milling or otherwise reducing the particle size of commercial SiC improve its performance? Can the treated commercial powder be used to make slurries with higher SiC loading? Deeper comparison of the results of the two articles might begin to answer some of these questions.
However, such comparison of these works is difficult. The researchers used rather different conditions, specifically solids loading and shear rate for viscosity measurements, which in turn resulted in vastly different axis scales for their viscosity measurement curves. One might argue that a researcher can estimate the data from the graphs. While true, how well can you estimate the data from Figure 6 of Vu et al. to be able to compare it to Figure 9 of Gao et al.?
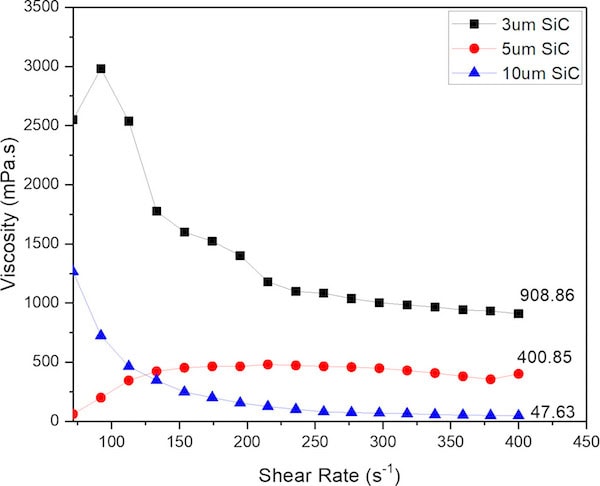
Figure 6 from Vu et al. Notice the minimum viscosity of the 10 um SiC (55% solids). Credit: Vu et al., International Journal of Applied Ceramic Technology
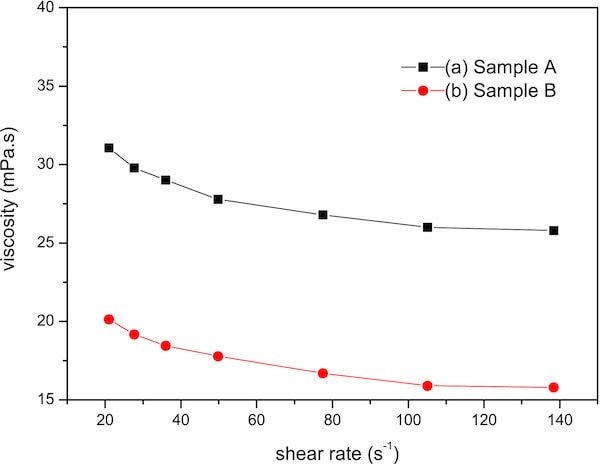
Figure 9 from Gao et al. Credit: Gao et al., International Journal of Applied Ceramic Technology
This problem is not a unique one, and the movement toward open science for scholarly publications aims to remedy such conundrums. Open science—with the goal of greater transparency, cooperation/collaboration, and validation of information in the scientific record—has many elements, such as open data and open access. Open data is the sharing of the underlying data of scientific reports via open repositories. In a world with open data, one of these researchers (or any other researcher for that matter) could download the datasets of these studies and create new graphs overlaying the pertinent data from each.
The American Ceramic Society and Wiley, its publishing partner, are committed to fostering open science initiatives. Our immediate focus is on open access, where anyone with an internet connection can read articles published under Creative Commons licensing and financially backed by the author, institution, consortium, or government agency.
International Journal of Ceramic Engineering and Science is a fully gold open-access journal and ACerS’ three other journals (including ACT) publish articles under open-access licensing when arrangements for it are made by the author. Additionally, Wiley is fostering open access through innovative pilot programs including Project DEAL, which provides open-access publishing and reading for the entire Wiley journal catalog to institutions in Germany. A similar program is in place with VIVA (Virginia) member institutions and others around the world.
You can find out the open-access arrangements between Wiley and your institution by clicking this link.
The first paper by Vu et al., published in International Journal of Applied Ceramic Technology, is “Highly concentrated aqueous SiC slurry containing fine SiC powder: A new approach for ultra‐dense green body” (DOI: 10.1111/ijac.13398).
The second paper by Gao et al., published in International Journal of Applied Ceramic Technology, is “Influence of surface oxide layer of SiC powder on the rheological properties of its slurry” (DOI: 10.1111/ijac.13385).
Author
Jonathon Foreman
CTT Categories
- Basic Science