[Image above] Credit: Travis Nep Smith, Flickr (CC BY-NC 2.0)
While increased adoption of electric and hydrogen-powered vehicles is an important part of decarbonizing the transportation sector, another component (often overlooked in the United States) is investment in public transportation infrastructure.
The use of public transportation such as buses, trains, and trams reduces the number of personal vehicles on the roads, which translates to reduced emissions. A National Academies report estimates that public transportation in the U.S. saved 63 million metric tons of carbon dioxide equivalent emissions in 2018. Additionally, public transportation substantially lowers crash rates and crash severity compared to personal automobile travel.
Rail travel is one form of public transportation that is expected to witness significant growth. An International Energy Agency report projects that passenger and freight activity will more than double by 2050.
In light of this expected growth, investment in fiber-reinforced composite parts is becoming a more profitable consideration for rail companies.
Glass and carbon fiber-reinforced polymers are used extensively in the aerospace industry to replace traditionally metal parts. This substitution allows a device to retain its strength while weighing considerably less.
However, the upfront cost of fiber-reinforced composites can be significantly more than for metal, so the investment traditionally was not worth it for the railway sector.
In the past decade, several notable studies have investigated creating railcar bogies out of fiber-reinforced composites. Bogies are the structure underneath a railway vehicle body to which axles and wheels are attached through bearings. Reducing the weight of this part could lower track wear and infrastructure maintenance costs.
Brake shoes are another component that may benefit from fiber-reinforced composites. Currently, most of the world’s trains are equipped with pneumatic braking systems that use compressed air to push a friction material (the brake shoe) onto the wheels to slow/stop their rotation (see an illustrated explanation of this process in the video below).
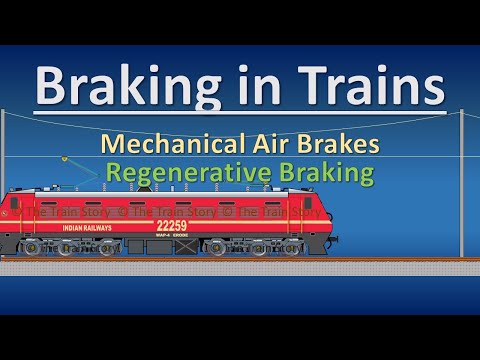
Credit: The Train Story, YouTube
Up until the mid-1980s, brake shoes (and other train components) typically contained asbestos. However, once asbestos-based friction materials were phased out due to health concerns, cast iron blocks and steel fibers were the dominant materials used for brake shoes. In addition, fibers made of mineral, glass, carbon, or aramid started being used more often as well.
Compared to the automotive field, there are far fewer research papers reporting on the effects of different fibers on the friction material’s properties in railway applications. In a recent paper, researchers in the R&D department at Knorr-Bremse Pamplona, a Spain-based manufacturer of friction materials for rail vehicles, investigated the effects of substituting glass fibers for steel fibers in a low-steel railway brake shoe formulation.
To prepare the samples for this study, the researchers used a 30% steel fiber formulation as the base brake shoe. They then replaced half of the steel fiber content with glass fibers featuring two different morphologies (chopped strands or pulp format).
The pulp glass fibers featured a similar morphology to the steel fibers, which allowed for the effect of each material to be evaluated. In contrast, the chopped glass fibers were ten times longer than the pulp glass fibers, which allowed for the effect of fiber length to be evaluated.
The resulting brake shoes were physically tested using methods reported in a previous paper by Knorr-Bremse and University of Zaragoza (Spain) researchers. A 30-ton MEGA hydraulic press equipped with a manometer was used to conduct shear force tests (i.e., determine the force needed to detach each friction material from its backing plate). Hardness of the friction materials was tested in a Centaur HR-150 Rockwell durometer (following ISO 2039–2), while density values were collected in an Alfa Mirage SD-200 L densimeter (following ISO 1183).
For friction tests, brake shoes were tested in a Schenk full-scale railway brake dynamometer, following settings described in another previously published paper. The rotating part was a CL60 steel wheel with a diameter of 840 mm, and the fixed part was the different brake shoes that fitted onto a brake block holder, connected to a pneumatic actuator or tread braking unit. Two brake shoes of each material were friction tested (250 mm x 80 mm x 60 mm, 1xBgu configuration).
Based on these tests, the researchers determined that the addition of glass fibers and their morphology had marked effects both on the friction performance and wear rate of railway brake shoes. Specifically,
- Effects on mechanical property. The use of chopped glass fiber strands decreased the shear strength, density, and Young’s modulus, and increased the maximum load at failure. Pulp fiber glass decreased the density and Young’s modulus.
- Friction effects. The all-steel-fiber brake shoe consistently showed a lower friction coefficient throughout the friction test, regardless of the testing conditions. In contrast, the glass fiber brake shoes showed higher friction, which was linked to the creation of more abrasive debris particles.
- Wear rates. The all-steel-fiber brake shoe showed the highest wear rate, which was attributed to the higher propensity of steel fibers to be pulled out from the composite. The glass fiber brake shoes showed lower wear rates, which was attributed to their brittle mode of failure. When these fibers broke, part of the fiber was left embedded in the friction material, enabling it to keep performing as a primary plateau while stabilizing the third body layer and preventing wear. Additionally, chopped glass fibers further prevented wear by collecting debris in the pores created around and within the fibers.
The researchers conclude the study by noting that these results will help manufacturers better adhere to region-specific standards and regulations for railway brake friction materials.
For example, the friction level is usually one of the most regulated properties of a brake shoe. With the knowledge gained from this study, “friction material designers can rely on one more tool when tuning friction levels, as adjusting the steel fibers–glass fibers’ proportions can have a significant effect on the final friction performance of the brake shoe,” they write.
The paper, published in Tribology International, is “The role of glass fiber morphology on the friction behavior and wear mechanism of low steel-NAO hybrid railway brake shoes” (DOI: 10.1016/j.triboint.2022.108079).
Author
Lisa McDonald
CTT Categories
- Material Innovations
- Transportation