[Image above] Both glass and ceramics can be quite brittle. How do we increase ductility so they do not break so easily? Credit: PxHere
Ceramics and glass share a lot in common. Both typically exhibit high strength, high hardness, high chemical inertness—and, unfortunately, brittleness.
Finding ways to increase the toughness of ceramics and glass is an ongoing and active field of research. In today’s CTT, we take a look at two recent studies investigating different solutions.
Consolidate glassy nanoparticles to achieve ductile glass
In the past few months, we discussed a couple of articles showing how to create tougher, more ductile glass. In July, we published a CTT on increasing microductility of oxide glass through aging in a humid atmosphere. Then in August, we showed how researchers from Denmark and the United States increased an oxide glass’s crack resistance by infusing the glass with nanoparticles.
Now, materials science and engineering researchers from Rensselaer Polytechnic Institute also report they investigated using nanoparticles to toughen an oxide glass.
Yanming Zhang (graduate student), Yunfeng Shi (associate professor), and Liping Huang (professor and ACerS member) looked at silica glass for their experiment because traditional methods for toughening oxide glass, such as thermal tempering and chemical tempering, do not work well for silica glass due to its low thermal expansion coefficient and lack of mobile ions.
In their study, the researchers compared molecular simulations for consolidated silica (silica glass consolidated from glassy nanoparticles) to compressed silica (silica glass compressed from bulk as-quenched sample).
“Surprisingly, consolidated silica from glassy nanoparticles displays exceptional ductility which reaches up to ~80% failure strain and increases as the nanoparticles size reduces,” they write in the paper. “In contrast, the compressed silica exhibits only marginally enhanced plasticity with a failure strain of ~29%.”
On further inspection, the researchers determined the enhanced ductility emerges when silicon bonds with five oxygen atoms instead of four, a structure known as five-fold silicon.
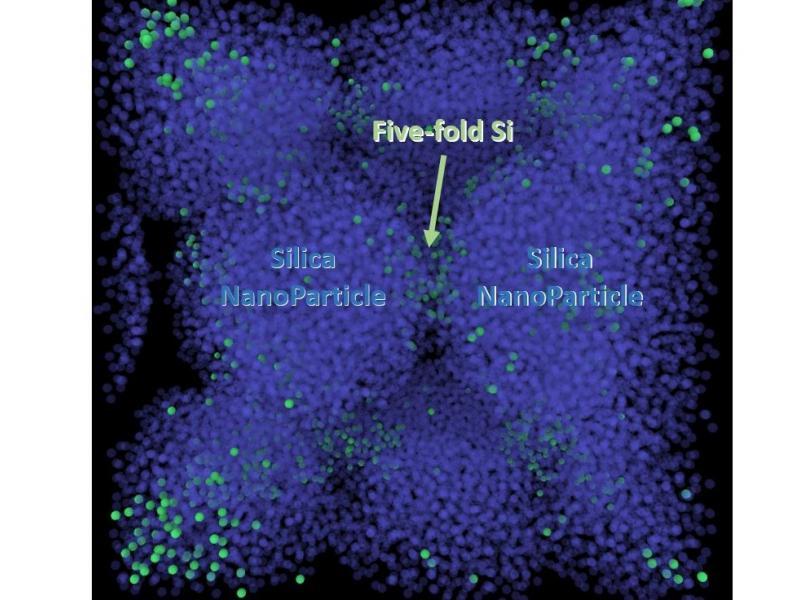
Plasticity-carriers (five-fold silicon shown here) form at the contact of silica nanoparticles under extreme pressure, in route to a fully dense ductile silica glass. Credit: Zhang et al., Rensselaer Polytechnic Institute
“The compression actually changes the material structure,” Shi says in a Rensselaer press release.
In the future, the researchers plan to test the glass in the lab.
The paper, published in Nano Letters, is “Silica glass toughened by consolidation of glassy nanoparticles” (DOI: 10.1021/acs.nanolett.9b01634).
Ceramic materials made ductile through flash sintering
In mid-September, a research collaboration published a “shocking” discovery concerning ceramics—by adding an electric field to the conventional sintering process, they could form bulk components from ceramics that are more ductile and durable than conventionally formed ceramics.
“We have been able to show that even at room temperatures, ceramics sintered with the electric field surprisingly deform plastically before fracture when compressed at high strain,” Haiyan Wang, ACerS Fellow and professor of materials engineering and electrical and computer engineering at Purdue University, says in a Purdue press release.
The researchers—from Purdue University, Rutgers University, Lawrence Berkeley National Laboratory, University of California, Davis, and the U.S. Naval Research Laboratory—explain that, in general, crystalline metallic materials deform plastically through dislocations at room temperature and/or diffusion creep at elevated temperatures. “In contrast, ceramics with ionic or covalent bonding are strong but mostly brittle at low temperatures due to the lack of dislocations to accommodate plasticity,” they write in the paper.
To increase room-temperature plasticity of ceramics, one approach is significant grain refinement, or keeping grain sizes in the range of a few nanometers. However, it is challenging to maintain small grain sizes while sintering because conventional sintering techniques typically require high temperatures and long sintering times, which lead to considerable grain coarsening.
Flash sintering, a newer sintering technique, offers an alternative to conventional techniques that can take place within a few seconds, without pressure, and at much lower furnace temperatures.
“During flash sintering, a ramp heating process and moderate electrical fields are applied. Once reaching the onset of the flash temperature, a densification process occurs nearly instantaneously, accompanied by a sudden increase in electrical conductivity,” the researchers explain in the paper.
Despite interest in flash sintering of ceramics, “investigations on the deformability of flash-sintered ceramics remain scarce,” the researchers add.
In their study, the researchers looked to see how flash sintering may increase the ductility of titanium dioxide (TiO2), a ceramic in which plastic deformation becomes feasible at test temperatures over 600°C.
When the researchers compared the ductility of their flash-sintered TiO2 to conventional TiO2 and other conventional ceramic systems, they discovered it exhibited significantly enhanced deformability even at room temperature.
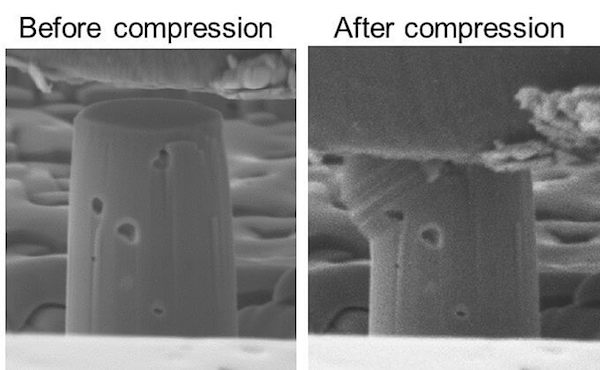
Researchers led by Purdue University discovered flashing sintering ceramics can increase the material’s ductility. Credit: Li et al., Purdue University
“For conventional sintered TiO2 tested at both RT [room temperature] and 400°C, all pillars experienced brittle catastrophic fractures at an average true strain of 2% for RT tests and 3% for 400°C tests,” the researchers write. In contrast, at room temperature the flash-sintered TiO2 showed work hardening to a maximum flow stress of 2–2.5 GPA, and no fracture was observed up to about 12% strain.
The researchers attribute the increased room-temperature ductility to unusually high-density defects—such as stacking faults, twins, and dislocations—caused by the flash-sintering process.
“The existence of these defects removes the need for defect nucleation in ceramics, which typically requires a large nucleation stress, greater than the fracture stress of ceramics,” Wang says in the press release.
In the conclusion, the researchers discuss possibilities of the technique for other ceramics. “This study strongly suggests that the flash-sintering method presents great potential in promoting plasticity in a broad range of ceramic materials,” they write.
The paper, published in Science Advances, is “Nanoscale stacking fault–assisted room temperature plasticity in flash-sintered TiO2” (DOI: 10.1126/sciadv.aaw5519).
Author
Lisa McDonald
CTT Categories
- Basic Science
- Modeling & Simulation