[Image above] A worker handles a magnesia carbon brick at a Zibo Jucos Co., Ltd. plant in China. MgO–C bricks can be fabricated using various carbon sources, and significant effort has gone into determining which source can best improve the brick’s thermal shock resistance. Credit: Jucos Refractory, YouTube
This past May, CTT brought attention to the often-overlooked impact that material source can have on a ceramic’s final properties.
Starting materials, or the substances used to produce a product, can often be derived from different sources. The specific chemical makeup and structure of the source material can influence how well it integrates with other components during the fabrication process.
For example, the May CTT profiled an International Journal of Applied Ceramic Technology paper that evaluated the effect of using three common sources of magnesium to create the refractory oxide magnesium aluminate spinel. The authors determined that the sample created from fused magnesia demonstrated the best properties for thermal storage applications.
Magnesia carbon (MgO–C) bricks are another refractory oxide whose final properties can be greatly influenced by material source. This refractory material is widely used in steelmaking because of its excellent thermal, chemical, and mechanical properties, which are due to the individual characteristics of magnesia and carbon as well as the synergy between them.
MgO–C bricks can be fabricated using various carbon sources, such as expanded graphite, carbon black, carbon nanotubes, carbon nanofibers, and graphene and its oxides. Among these, expanded graphite is particularly promising.
Expanded graphite has a layered structure that allows molecules to be intercalated in between the graphite layers. This modified graphite, which can be prepared from flaky graphite via an easily scalable industrial method, fills the gaps between magnesia particles and promotes the formation of beneficial high-temperature phases with different antioxidants, such as aluminum or silicon.
However, expanded graphite is more prone to oxidation than flaky graphite. This tendency may lead to iron contamination when present in large amounts or the release of carbon emissions, among other issues.
As such, studies must be done to determine the optimum amount of expanded graphite for MgO–C brick production.
In June 2023, researchers from Changwon National University in the Republic of Korea published a paper describing how they systematically investigated the effects of expanded graphite content (0−4 wt.%) on MgO–C bricks with a total graphite content of 15 wt.%.
They created the MgO–C bricks by combining magnesia particles, flaky and expanded graphite, aluminum and silicon (antioxidants), a phenolic resin (novolac; binder), and hexamethylenetetramine (curing agent). Subsequent analysis of the bricks focused on the relationship between microstructural changes (e.g., apparent density and porosity) and thermal and mechanical properties.
The researchers determined that expanded graphite efficiently absorbed and relieved thermal stress and suppressed thermal deformation. Therefore, thermal shock resistance increased as more expanded graphite was added.
On the other hand, when the quantity of expanded graphite reached 4 wt.%, the number of apparent pores increased, leading to a decrease in fracture strength and also thermal shock resistance.
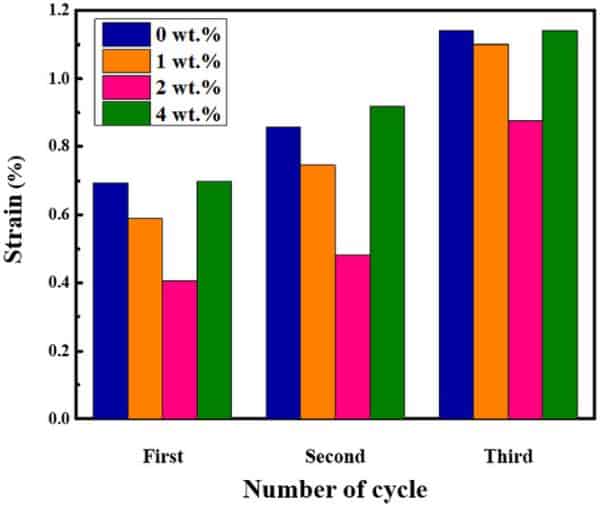
Graph showing the residual strain after repeated thermal shock experiments (up to four cycles). Bricks containing an expanded graphite content of 2 wt.% exhibited optimal performance. Credit: Kim et al., International Journal of Applied Ceramic Technology
Ultimately, the researchers determined an expanded graphite content of 2 wt.% provided optimal performance, which they attributed to the fine and uniformly distributed pores in that sample. They conclude that “future works should examine the performance of such optimal refractories in practical applications.”
The paper, published in International Journal of Applied Ceramic Technology, is “Effects of expanded graphite content on the performance of MgO–C refractories” (DOI: 10.1111/ijac.14464).
Author
Lisa McDonald
CTT Categories
- Refractories
- Thermal management