[Image above] Fully inkjet-printed rGO/α-Fe2O3 gas sensor array (scale bars: 100 μm). Researchers discovered a possible solution to uniformly deposit inks based on 2D materials in 2017, but only this year did they propose an explanation for the mechanism behind it. Credit: Guohua Hu, University of Cambridge and The Chinese University of Hong Kong; Science Advances (CC BY 4.0)
When scientists succeeded in isolating graphene—a single atomic layer of carbon—for the first time in 2004, the world had high hopes for the material in application. Yet in the past 15 years since its discovery, realizing graphene’s potential remains largely elusive.
One factor hindering development and commercialization of graphene-based products is the proliferation of poor quality and fake graphene being sold as commercial-grade.
“Whether producers of the counterfeit graphene are aware of the poor quality is unclear,” Antonio Castro Neto, senior researcher of a study examining this problem, explains in a press release on the study. “Regardless, the lack of standards for graphene production gives rise to bad quality of the material sold in the open market. This has been stalling the development of the future applications.”
Yet even when quality of graphene is assured, there are difficulties associated with incorporating graphene into devices that hinder commercialization as well—such as in next-generation printed electronics.
Printed electronics is a nascent branch of electronics manufacturing that offers a way to economically and conveniently produce electronic circuits and devices on flexible substrates. It involves using established printing techniques, such as screen printing, ink-jet printing, or gravure printing, to deposit conductive materials onto a given substrate in a predefined pattern.
Much research focuses on developing novel conductive materials that can be deposited using these printing methods. And graphene and related 2D materials have received a fair share of attention due to their unique electronic and optical properties.
But researchers have run into problems depositing inks based on 2D materials.
A common approach for creating inks based on 2D materials is to use liquid-phase exfoliation, a group of approaches that exfoliate 2D materials from bulk materials directly in a liquid media. These dispersions are then used for device fabrication.
“However, this direct adaption without elaborate ink formulation through control over composition, rheology, and fluidic properties presents challenges in achieving uniformly deposited functional structures and, hence, device reproducibility and scalability,” researchers write in a recent open-access paper.
The researchers are an international team led by Tawfique Hasan at the University of Cambridge. And they identify three critical parameters that hinder uniform deposition:
- Suboptimal droplet jetting
- Poor control over substrate wetting
- Drying of the inks
Researchers have proposed various strategies to address the first two challenges, but the third parameter—drying of the inks—continues to frustrate scientists.
When inks based on 2D materials dry, they exhibit the coffee-ring effect, a type of capillary flow. In particular, different evaporation rates across the droplet cause liquid evaporating from the edge to be replenished by liquid from the interior—leading to ring-shaped, non-uniform deposition of the ink.
“Although various strategies have been developed to suppress the [coffee-ring effect], none of these are generally applicable for 2D crystal inks due to problems of dispersion stability, postprocessing requirements, or the effect of ink additives on material functionality,” the researchers write.
In 2017, the researchers investigated black phosphorus ink formulation and made a surprising discovery—they achieved uniform ink deposition when using a mixture of isopropanol and 2-butanol for the solvent in the liquid-phase exfoliation process.
Isopropanol is widely used as a solvent for graphics inks. But traditionally, use of isopropanol solvent to process inks based on 2D materials led to nonuniform deposition. Why did mixing 2-butanol with isopropanol change the deposition outcome?
That question went unanswered in the 2017 paper. So the researchers looked to answer it in the recent study.
They observed that while droplets were “pinned” (the outer edge remained stationary) at the early stage of drying in the isopropanol case, droplets expanded at an almost constant speed and did not pin until later in the isopropanol/2-butanol case—thus suppressing the coffee-ring effect.
In the results section, the researchers propose Marangoni flows in the isopropanol/2-butanol mixture prevented the droplets from pinning.
The Marangoni effect describes how fluid flow along the interface of two fluids is affected by differences in the fluids’ surface tensions.
In the case of inks made using the isopropanol/2-butanol solvent, isopropanol evaporates faster than 2-butanol. So the isopropanol along the contact line (edge) of the droplet evaporates first, leaving mostly 2-butanol behind. This evaporation causes a difference in surface tension between the 2-butanol-rich edge and isopropanol-rich center of the droplet, “leading to a Marangoni flow from thicker areas to thinner areas” and uniform spreading of the 2D materials, the researchers write.
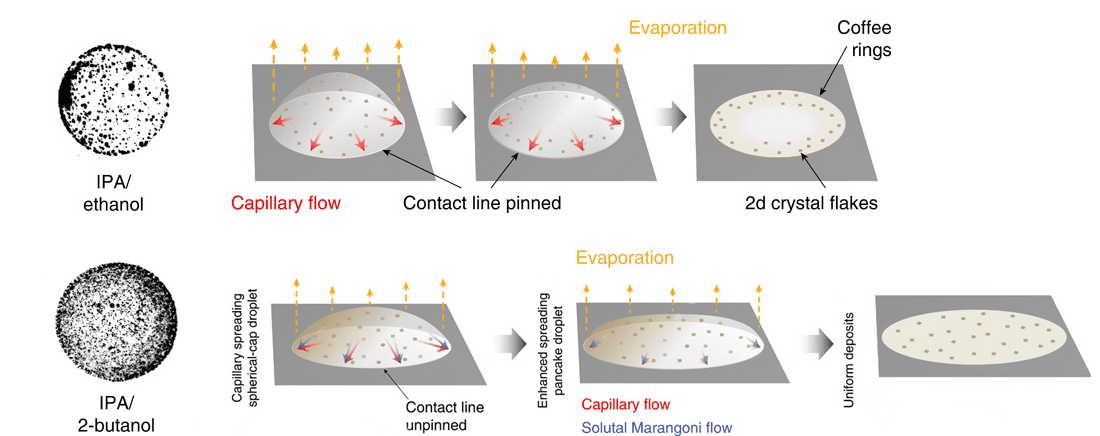
Inverted optical micrographs of dried isopropanol-based droplets (top) and isopropanol/2-butanol-based droplets (bottom). The accompanying illustrations show the differences between their drying mechanisms: coffee-ring effect (top) and Marangoni flow (bottom). Credit: Hu et al., Science Advances (CC BY 4.0)
The researchers printed arrays of nonlinear optical saturable absorbers, room temperature gas sensors, and photodetectors to demonstrate the potential of inks created using the isopropanol/2-butanol solvent. For all devices, the performances were “well within acceptable statistical variations for printed device manufacturing from 2D crystal inks, addressing one of the most challenging obstacles toward their additive manufacturability.”
In the paper’s conclusion, the researchers emphasize the importance of their findings.
“Our ink formulation with active [coffee-ring effect] suppression thus lays the foundation for high-speed additive manufacturing of all-printed sensors and systems with a high level of large-scale integration,” they write.
The 2017 open-access paper, published in Nature Communications, is “Black phosphorus ink formulation for inkjet printing of optoelectronics and photonics” (DOI: 10.1038/s41467-017-00358-1).
The 2020 open-access paper, published in Science Advances, is “A general ink formulation of 2D crystals for wafer-scale inkjet printing” (DOI: 10.1126/sciadv.aba5029).
Author
Lisa McDonald
CTT Categories
- Basic Science
- Electronics
- Nanomaterials