[Image above] Body armor plates made from silicon carbide that were manufactured by the company Temp-3000 in Ukraine. Credit: VictorAnyakin, Wikimedia (CC BY-SA 4.0)
As managing editor of the ACerS journals, I read the titles of many newly published articles. In recent months, I noticed a growing number of articles on high-strength carbides and borides. Because ceramic armor is an application for these materials, and with the recent events in Washington, D.C., and Myanmar, I was inspired to understand the issues explored in these articles.
First things first. What are the mechanical properties that lead to the best material for ceramic armor? One would think that the hardest, strongest, toughest materials would be ideal. But the answer is not that simple. According to a seminal paper by Shockey, Simons, and Curran (2010), “ballistic tests often show that the best performing armor material is not the hardest, nor the strongest, nor the toughest.” More recent articles appear to show correlation of hardness to ballistic resistance, though others have shown toughness to be a factor.
Another paper by Lankford (2005) provides some insight on this matter. The extremely high loading and strain rates on ceramic armor lead to very complicated damage mechanisms, including plastic deformation, microcrack initiation, growth and coalescence, and flow of pulverized materials away from the impact zone.
Designing better ballistic materials is more than a matter of finding the optimal combination of material properties. These damage mechanisms require a deep understanding of the microstructure–damage relationships, which is a rather complicated problem to solve. Thus, I decided to focus this CTT on efforts to improve processing methods for fabricating dense ceramic components.
Several recent papers published in ACerS journals focus on sintering boron carbide (B4C), titanium diboride (TiB2), and silicon carbide (SiC) as the major phase or largest second phase materials. These three materials have similar elastic moduli (~400–500 GPa) and hardness (~30–40 GPa). Boron carbide is attractive for its hardness (second only to diamond) and low density (2,500 kg/m3), though fully sintered boron carbide has very low toughness (2 MPa m½). Compared to B4C, SiC has a very low cost and is tougher (4 MPa m½) but is slightly more dense (3,200 kg/m3). TiB2 is the toughest, densest, and most expensive of these materials.
The bonding in these materials is highly covalent, leading to very high melting temperatures and minimal self-diffusion required for sintering. Parts are generally sintered at high temperatures, often over 2,000°C. Sintering can be at atmospheric pressure up to high pressures (e.g., 30 MPa). Hot-pressing at these high temperatures is rather expensive and can produce only a limited range of part shapes.
Many of the recent ACerS articles explore using combinations of B4C, TiB2, and SiC. As strong covalent materials, each material also bonds well to the others—and the differences in composition lead to increased diffusion, reducing the energy barrier of forming the new bonds. Additionally, TiB2 and other substances are added to B4C and SiC to improve the overall toughness and sinterability.
The following is a list that showcases a few of the recently published articles, including a brief summary of the processing conditions and key outcomes. Most of these articles use some form of chemical reaction to drive sintering while others use more traditional sintering aids.
The first two articles explore ways to reduce the sintering pressure. The following three explore lower processing temperatures. The final two are innovative methods for forming net-shaped parts at low temperatures and pressures.
Mechanical properties of SiC‐C‐B4C composites with different carbon additives produced by pressureless sintering (ACT)
The aim of this article is the exploration of the effects of additive composition and carbon source on the sintering and fracture behaviors and mechanical properties of silicon carbide.
The authors mixed silicon carbide with difference carbon sources and, in some experiments, a small amount of B4C. The authors used carbon to scavenge the oxygen from SiO2 that tends to form on the surface of SiC. Because SiO2 hinders sintering, removing the oxygen should improve the densification process. For reasons mentioned above, B4C reacting with the SiC should provide additional driving force for consolidation. The samples are sintered at high temperatures (2,150–2,200°C) in an argon atmosphere.
The sintered part densities ranged from 93.7–98.5% relative density, with the highest values at 2.5% added carbon. Samples without B4C exhibited generally lower density. Hardness, Young’s modulus, and fracture toughness increased with carbon content from 0.5 to 2.5% added carbon and dropped with higher amounts. The authors found small variations with carbon source, but little influence of B4C on the mechanical properties. The authors provide an in-depth analysis of the microstructure and relative strengths of grains and grain boundaries.
Microstructure and mechanical property of (TiB2‐SiC) agglomerate‐toughened B4C‐TiB2‐SiC composites (ACT)
In this study, the authors attempted to fabricate high‐performance B4C‐TiB2‐SiC composites with a special toughening structure by using a new reactive hot-pressing method.
The authors blended B4C and TiSi2 powders in a range of compositions. The powders were reacted in a vacuum hot-press at 2,050°C, resulting in composites of B4C, TiB2, and SiC.
The material properties varied with compositions. Notably, the composites were more than 99% dense and had relatively high toughness (4–6 MPa m½). The authors present comprehensive microstructural analysis to explain the mechanical performance, such as the figure below, which explains enhanced toughness.
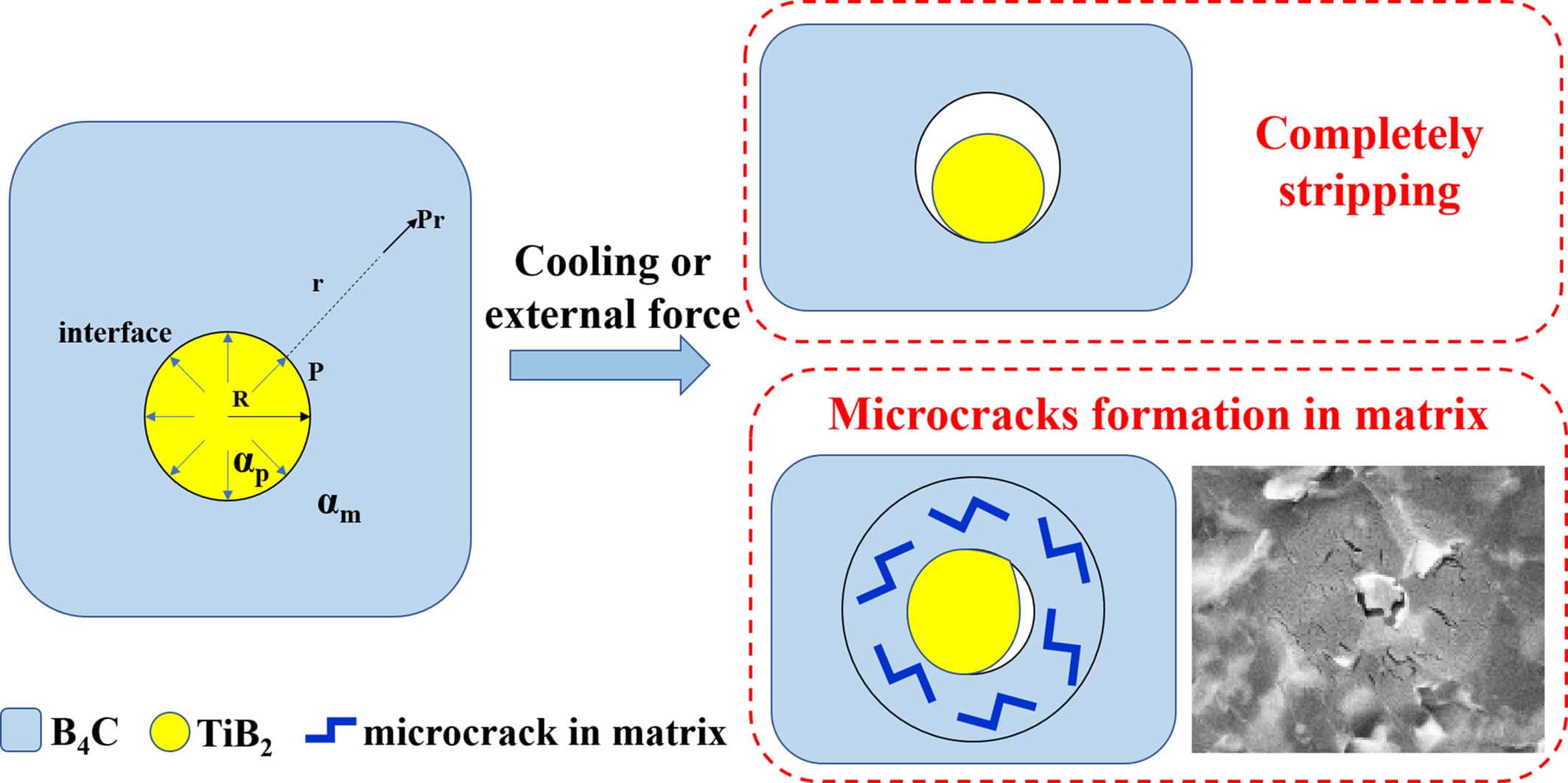
A schematic showing the formation process of microcrack regions. High induced stresses (e.g., from shrinkage or deformation) are relieved through “stripping” of the bonds between the inclusion and the matrix. Smaller stresses are relieved through microcracks in the matrix. Both mechanisms increase the toughness of the matrix material. Credit: Wang et al., International Journal of Applied Ceramic Technology
Dense and core‐rim structured B4C‐TiB2 ceramics with Mo‐Co‐WC additive (JACerS)
As the title suggests, the authors investigated the use of high-melting molybdenum and low-melting cobalt metals along with tungsten carbide as sintering aids, with the aim of improving the density of B4C-TiB2 composites while also reducing the sintering temperature.
In their studies, the ratio (%) of B4C:TiB2 varied from 95:4 to 30:69, while the molybdenum and cobalt were maintained at 0.5% each, all measured before milling. Because the tungsten carbide resulted from abrasion of milling balls, the amount of tungsten carbide was measured after milling. The milled and dried mixtures were spark plasma sintered at 1,900˚C and 30 MPa pressure.
As TiB2 content increased, the density decreased slightly (from 98.4 to 96.7%), hardness decreased significantly (from 30.7 to 16.5 GPa), while the toughness increased from 2.95 to 3.62 MPa·m½. The authors found tungsten and molybdenum in the grain boundaries of the sintered samples, with crack morphology depending on the TiB2 content.
Synthesis and performance of TiB2–B4C composites by high pressure of TiC–B mixture (ACT)
The authors of this study aimed to improve electrical and thermal conductivity of B4C (normally an insulator) so that it can be machined by electric discharge machining. As a result, toughness was not tested.
They mixed TiC and boron in stochiometric ratios (1:6 by mole) and then reacted the samples in a hot-press at 5 MPa and at temperatures ranging from 1,500°C to 1,900°C.
The parts sintered at 1,600°C and above were 97–98% dense. Those sintered at 1,700°C and higher had hardness values of 30–32 GPa. As with the prior article, the authors discuss the microstructure of the samples.
In situ reaction and solid solution induced hardening in (Ti,Zr)B2‐(Zr,Ti)C composites (JACerS)
Equimolar mixtures of ZrB2 and TiC were milled and hot-pressed at 30 MPa at various temperatures from 1,700 to 2,000°C in a fundamental study of in situ reaction and solid solution on microstructure and mechanical properties.
With similar ionic radii, zirconium and titanium have been shown to form solid solutions within both the carbide and boride phases. See, for example, Figures 14325 and 16880 of the ACerS-NIST Phase Equilibrium Diagram database. The authors of this study found no other phases using XRD or SEM. SEM also indicated more than 99% density with minimal visible porosity after sintering at temperatures as low as 1,750°C. The mechanical properties of hardness, strength, and toughness were relatively similar with high values at sintering temperatures from 1,800 to 1,900°C.
Synthesis, structure, and properties of polymer‐derived, metal‐reinforced boron carbide cermet composites (ACT)
In an effort to investigate methods of fabricating net-shaped boron carbide parts, the authors mixed boron with a cross-linkable pure hydrocarbon polymer as the carbon source and an array of metals to form B4C-cermet composites. Composites of B4C with SiC or WB2 were also fabricated and compared to cermets from silicon and tungsten.
Pressed disks of the precursor materials were heated to 1,450°C in a tube furnace (pressureless sintering). This sintering process nearly completed the reaction of boron with carbon—only small amounts of residual boron and carbon appeared in XRD patterns.
Though the resulting samples were highly porous (~75% dense) with low resulting hardness, the study demonstrated the feasibility of the method for low-temperature formation of net-shaped boron carbide-based cermets. Their future work will explore methods to improve the densification, such as higher reaction temperatures and polymer infiltration processing.
Fabrication of reaction bonded TiB2/Si/SiC composites for thermal applications (IJCES)
Like the previous article, the authors here investigated using in-situ reactions to form dense, net-shaped parts, though for electronics thermal management applications.
They mixed TiB2 with a polymeric carbon source, slip cast the slurries into rectangular shape molds, and pyrolyzed the green parts. These preforms were infiltrated with liquid silicon at 1,500°C, which reacted with the carbon to form SiC. The SiC bonded to the TiB2 with residual silicon in the interstices. A diagram of the infiltration process is below, along with a micrograph of one composition.
The resulting materials had high toughness, but hardness was not measured. They also showed thermal expansion and conductivity values that are attractive for electronics thermal management.
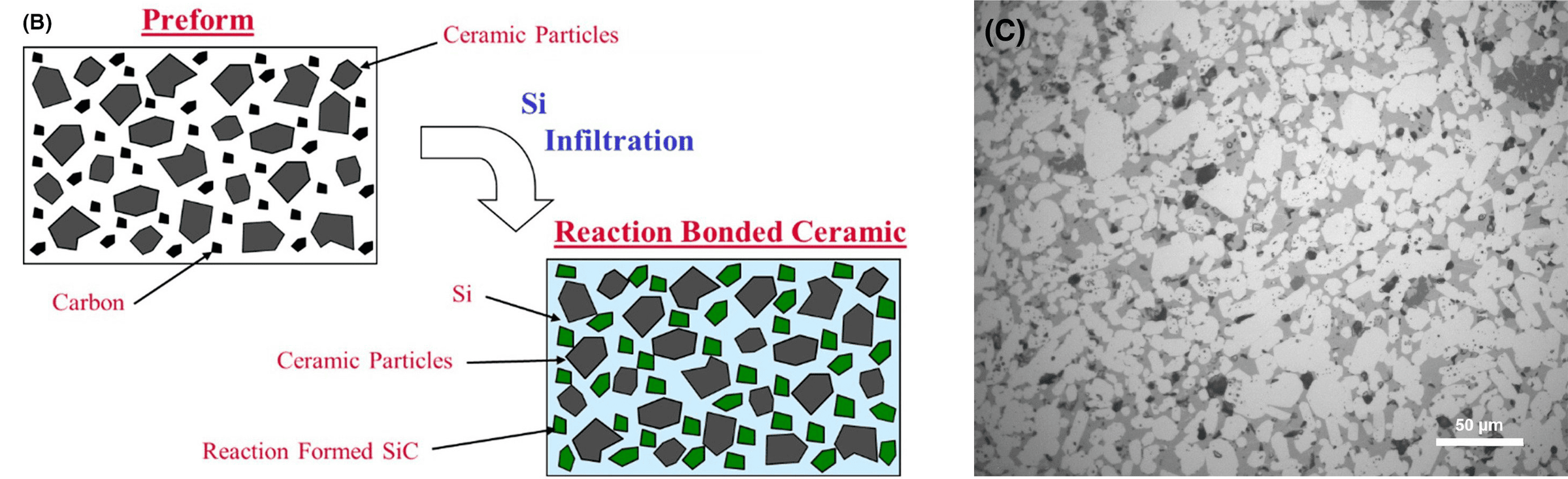
(Left) Diagram of reaction bonded ceramics. (Right) Micrograph of a ceramic composite. TiB2 particles are white; silicon is light grey; reaction formed SiC is dark grey; and infiltration defects are black. Credit: Wang et al., International Journal of Ceramic Engineering & Science
Clearly the sintering of borides and carbides for use in many applications is one of the hotter topics in ceramics research. Make sure you sign up for ACerS journal content alerts via your user account on https://ceramics.onlinelibrary.wiley.com. You can save your favorite searches and create alerts to send you updates on a regular (daily, weekly, or monthly) basis.
Author
Jonathon Foreman
CTT Categories
- Basic Science