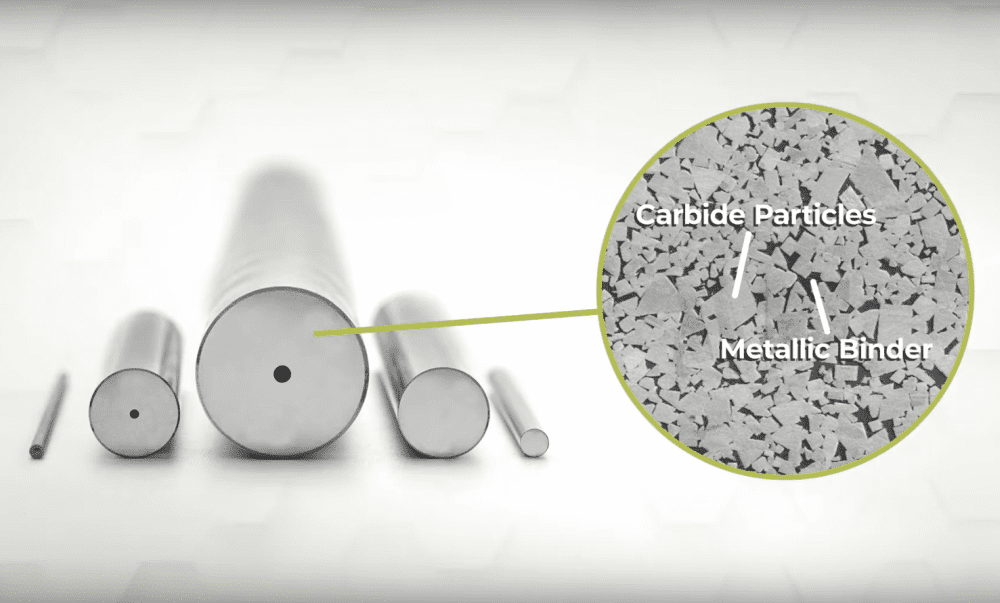
[Image above] Cemented carbides are metal matrix composites consisting of carbide particles held together with a metal binder. Credit: Hyperion Materials & Technologies, YouTube
The past few years have witnessed some significant milestones for materials.
In 2019, all chemicals got their due when the United Nations observed the International Year of the Periodic Table. In 2020, we recognized a revolutionary century of discovery for ferroelectricity, which was first reported in Rochelle salt in 1920. In 2022, we honored the historical significance of glass through the United Nations International Year of Glass and heralded the upcoming Age of Glass.
This year, manufacturers are celebrating the 100-year anniversary of the invention of cemented carbide.
Cemented carbides are metal matrix composites used extensively as cutting tool materials because of their high hardness, wear resistance, and fracture strength. Tungsten carbide, titanium carbide, and tantalum carbide are the most used carbides, with cobalt and nickel used as the binding metals to hold the carbide grains together.
In a blog post, Swedish metalworking company Sandvik Coromant explains that prior to the invention of cemented carbide, manufacturers relied on different steel alloys as cutting tool materials. But as demand for mass production increased, it became clear that materials with improved heat resistance needed to be developed to handle such ambitious processing conditions.
In March 1923, Karl Schröter, head of research & development at German electric light company Osram, filed the first patent for cemented carbide. He originally intended the material to be used for drawing dies in the light bulb industry, but it was later developed and tested for cutting tools.
The use of cemented carbide in cutting tools revolutionized the mass production process. As the Sandvik Coromant article explains, “Steel cutting speeds of up to 150 meters per minute became possible, almost four times faster than high-speed steel.”
In 1969, Sandvik Coromant became the first company to offer ceramic-coated cemented carbide inserts, and this coating increased metal-cutting performance by as much as 50%. Now, coated cemented carbides account for 80–90% of all cutting tool inserts.
The videos below provide more insight into cemented carbides and their wear properties.
As manufacturers look to the future of cemented carbide, a main concern is raw material availability. Some of the main metals used in cemented carbides, such as tungsten and cobalt, are in limited supply.
To proactively combat expected shortages, manufacturers are evaluating more efficient ways to fabricate cemented carbide tools, such as with 3D-printing methods. Additionally, they are looking to replace some of the metal binders with alternative materials, such as swapping cobalt for nanoceramics.