
I just got back from the 49th Annual Symposium on Refractories that was held Wednesday and Thursday at the combined St. Louis Section and Refractory Ceramics Division meeting. The theme of this year’s meeting was “Refractory Challenges in the Chemical and Petro-Chemical Industries.”
To open the symposium, Ed Linck (Linck Refractory Services) provided an overview of refractories challenges and technologies in the refining industry, particularly as they are used in fluid catalytic cracking units (FCCUs). In the 1950s when he began working in the industry, FCCUs ran 6-9 months before needing repair. Today, FCCUs run five years continuously, and new technologies are driving the life cycle toward seven years.
Linck noted that good materials are important, but installation is critical. “You can have the best material in the world, but if you don’t put it in right, it won’t work right,” he says. Downtime costs a refiner about $1 million per day, according to another speaker, Richard Parkinson of UOP LLC/Honeywell. Even though it takes about 100-150 tons of refractory material to line a FCCU, the refining industry accounts for only about 5-10 percent of the overall refractories market, with the majority of refractories going to the steel, metals, glass, and cements industries.
According to Parkinson, there are about 500 FCCUs worldwide that account for about 40 percent of the global gasoline production. A FCCU can process 20,000-200,000 barrels of oil per day. The catalytic cracking reaction occurs at about 500-550°C, and the catalysts are primarily zeolite and aluminosilicate fine powders. Consequently, many of the talks discussed challenges relating to corrosion, heat, and abrasion.
John Hellman, from Pennsylvania State University, is working on proppant technology, which are at the vortex of current events relating to hydrofracturing. He says that the Marcellus Shale reserve alone has enough natural gas reserves to supply the US energy needs for the next 150 years, which he describes as “the Saudi Arabia of natural gas.”
“This is an industry that is going to be large,” Hellman says, “and we have to do it right.” According to him, an important part of “doing it right” is advancing the proppant technology. The numbers are compelling. Each lateral well (12-20 come off each vertical wellhead) calls for 3,000 tons of proppant. The present market is in the neighborhood of 100 billion tons per year, up from 12 billion tons only seven years ago. At those volumes, proppants need to be available locally and cheap. His group is looking at ways to use discarded materials—such as glass cullet, slags, wrong-size roofing shingle minerals, and even the drill cuttings pulled from the wells—to make high-quality, inexpensive proppants, while solving some other industrial disposal problems. He also offered some intriguing ideas for “smart proppants” based on magnetic particles with piezoelectric outer shells that could provide in situ monitoring of the wells.
The RCD regulars like to characterize themselves as a “family.” To my delight, this family welcomed me into the clan by singing “Happy Birthday” to me yesterday to celebrate my Nth 39th birthday!

Paul Schlett of Valero Energy Corp. introduces the first speaker, Ed Linck of Linck Refractory Services. Between them they have over 100 years experience meeting the refractory needs of the refining industry. Credit: ACerS.

Wagner Silva of Magnesita Refractories presents the work that was the basis on his Allen Award-winning JACerS paper. Credit: ACerS.

ACerS president, Richard Brow, reports on ACerS activities and new initiatives to promote ceramic engineering education. Credit: ACerS.
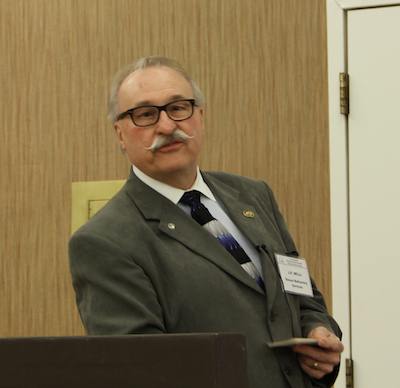
J.P. Willi, the 2013 Planje Award recipient, regaled the audience with highlights from the many “new opportunities” that his career in refractories afforded him. Credit: ACerS.

Vendors and attendees had plenty of opportunity to talk shop at the expo and reception. Credit: ACerS.
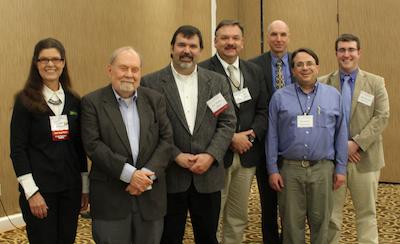
The RCD leadership. From left: Lora Cooper Rothen, ACerS RCD board liaison; Lou Trostel, counselor; Bill Headrick, immediate past chair, Dave Tucker, chair; Jens Decker, secretary; Ben Markel, vice chair; and Josh Pelletier, member-at-large. Credit: ACerS.