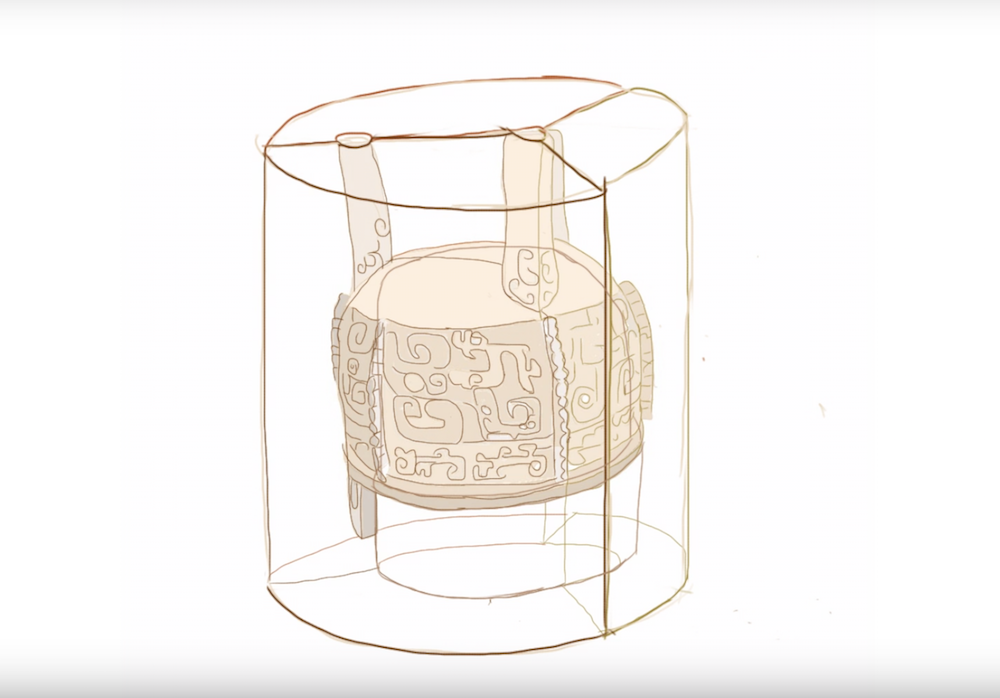
[Image above] Illustration showing how ceramic molds were used to cast bronze pieces during the Bronze Age. Credit: HarvardX, YouTube
Stone Age. Bronze Age. Iron Age. This three-part paradigm for classifying the prehistory and protohistory of humanity is used frequently in schools to help students learn about technological advances in weaponry and tools. However, the emphasis on the evolution of materials used for end-use products during each period, such as ritual bronze vessels and iron nails, means students often do not learn about the manufacturing processes used to fabricate these metal objects.
Ceramic molds were used throughout the world for casting bronze pieces during the Bronze Age, from Poland to Anatolia to China. Robert Mowry, Alan J. Dworsky Curator of Chinese Art Emeritus at the Arthur M. Sackler Museum of Harvard University, explains in general how these molds worked in the video below.
Researchers have increasingly focused on these ceramic molds in recent years as a way to understand diachronic change and regional variation in metallurgical industries during that period of history. However, investigating the ancient molds can be difficult, as with any ancient ceramic, due to the historical significance of the pieces, which often rules out use of destructive test methods.
Fortunately, researchers have any array of other testing methods available to analyze ancient ceramics, including sampling microscopic pieces from the historical object, modeling, and nondestructive imaging techniques.
Fourier transform infrared spectroscopy (FTIR) is one promising technique for investigating Bronze Age ceramic molds. Irreversible transformations that occur during the firing of clays and related silicate minerals can be identified in FTIR absorption spectra, making it possible to estimate firing temperatures of the ceramics.
Specifically, thermal alteration appears most clearly in three regions of the FTIR absorption spectra: the main Si–O–Si stretching vibration band (at wavenumbers around 1,000–1,100 cm−1), the Si–O–Al bending vibration band (510–580 cm−1), and the stretching vibration band of bound hydroxyl groups (3,600–3,700 cm−1). Shifts in peak position or changes in peak shape of these three absorption bands serve as qualitative criteria used to estimate firing temperature.
“Nonetheless, estimating firing temperatures in this manner is made difficult by the fact that the position of the main Si–O–Si absorption peak—the primary temperature indicator in most FTIR studies—does not always change continuously with increasing firing temperature,” researchers write in a recent open-access paper. “For many clays, the position of this peak (initially around 1030 cm−1) remains unaltered in the range of 500–800°C but shifts abruptly to higher wavenumbers (1080–1090 cm−1) once heated over 800°C.”
The researchers come from the University of Science and Technology Beijing, Peking University, and the Henan Provincial Institute of Cultural Heritage and Archaeology in China, in addition to a postdoctoral research fellow at the Stanford Archaeology Center in the United States. In their paper, they suggest this obstacle to estimating firing temperature can be overcome by measuring temperature-dependent changes to the strength of infrared absorption in the main Si–O–Si stretching band, “i.e., by measuring the height of the main Si–O–Si peak rather than its position.”
However, the intrinsic absorptivity of the sample material cannot be inferred directly from the peak height value measured in an absorption spectrum. So the researchers developed a novel FTIR-based approach for estimating ceramic firing temperature that they call the Absorptivity Ratio Method.
“The method involves (1) adding a standard compound (potassium ferricyanide) to archaeological samples and (2) using this internal standard to quantify the intrinsic absorptivity of each archaeological sample within the region of the infrared spectrum corresponding to the main Si–O–Si stretching band. Irreversible, temperature-dependent changes in absorptivity can thereby be detected accurately and used to infer firing temperature,” they explain.
The researchers used this method to estimate the firing temperature of bronze-casting ceramic molds excavated from the Nanguanwai bronze workshop at the Zhengzhou Shang City site, a capital city of the Early Shang dynasty. Mineralogical compositions of the ceramics, which date to the Early Shang period (sixteenth to fourteenth century BCE), were determined by X-ray powder diffraction.
They determined that, out of 10 total molds, seven were originally fired at 200–300°C and three at 300–400°C. They confirmed these estimates by comparing with independent estimates made via FTIR qualitative analysis, which compared favorably.
The researchers note that the estimated firing temperature values for the molds are lower than those reported by any previous study of ancient casting molds from China. This difference is likely due to the specific society from which the molds came, they state.
“It appears likely that deliberate low-temperature firing of moulds was also an essential part of the mould-making technological style of the Shang people. Evidence from bronze workshops at Anyang demonstrates the continuation and further development of this mould-making tradition into the Late Shang period,” they write.
Ultimately, “These results provide important new data for understanding the development and regional variability of Bronze Age mould-making technology in China,” they conclude.
The open-access paper, published in Scientific Reports, is “A new FTIR method for estimating the firing temperature of ceramic bronze-casting moulds from early China” (DOI: 10.1038/s41598-021-82806-z).