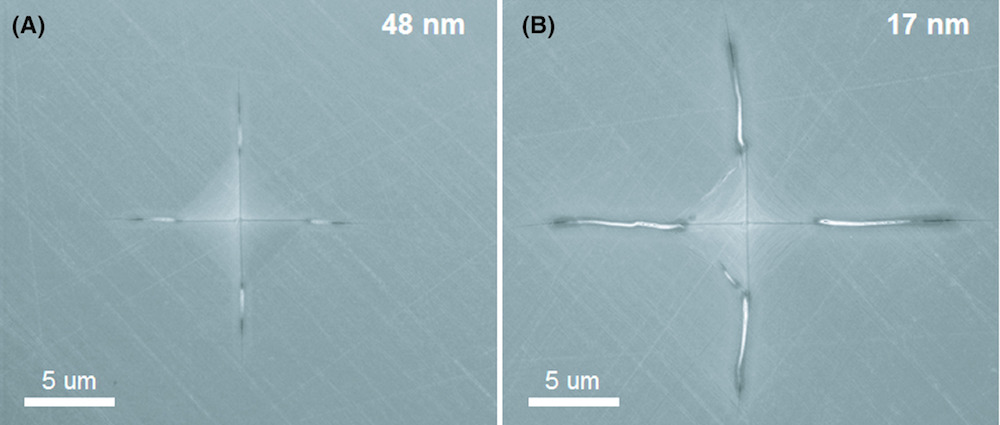
[Image above] For relatively large grains (48 nm), corner cracks are fairly short (about 4.5 µm), whereas their sizes roughly double up to 8 µm for small grains (17 nm). Generally, fracture toughness increases with decreasing grain size—what causes this inverse relation? Credit: Bokov et al., Journal of the American Ceramic Society
When I graduated from college and moved into my first real apartment, one of the first things I did was go out and buy some nice ceramic plates. Until then, I relied mostly on plastic dishes to avoid roommates breaking expensive dinnerware. But now that I was on my own, it was time to upgrade.
I love these plates for how smooth and solid they feel, compared to the flimsy plastic I used in college. However, a lot of that texture is based on the glaze. If I took one of those plates and looked at it under a microscope, I would see that behind its polished surface is a much-less-smooth structure.
Ceramics are made up of millions of small crystals, or grains, arranged in different orientations. And grain boundaries, where differently oriented grains meet, are one big reason ceramics are so brittle.
Cracks often form and propagate at grain boundaries, which can lead to material failure. However, grain boundaries also can absorb defects in the material by stopping short cracks from advancing further. If grain sizes are small enough—meaning there are a lot of boundaries—the ceramic gets harder and stronger.
Based on this knowledge, one may assume that the smaller the grain size, the harder the ceramic. And this relationship, called the Hall-Petch relation, holds true—to a point.
“In ceramics, this behavior [Hall-Petch] is more pronounced when grain sizes are below 100 nm,” researchers write in a recent paper, “but as grain sizes are further reduced, several studies also report, instead, the existence of an inverse relation as grains are refined below a critical size [hardness begins to decrease].”
The mechanisms behind this inverse Hall-Petch in ceramics are still under debate, and understanding these mechanisms are what the researchers of the recent paper looked to achieve.
The researchers are Arseniy Bokov (then Ph.D. student) and Ricardo Castro (professor) from the University of California, Davis, professor João B. Rodrigues Neto from the Federal University of Santa Catarina (Brazil), and professor Feng Lin from Sun Yat‐sen University (Zhuhai, China). In the paper, they explain that while grain boundary sliding appears to be the mechanism behind inverse Hall-Petch in metal alloys, the mechanism behind inverse Hall-Petch in ceramics appears to be cracking caused by “the activation of new energy dissipation modes.”
“When the grain size in a dense material is reduced to the nanoscale, geometrical constrains may significantly affect the structural nature of the grain‐grain interfaces due to a large population of triple junctions and high density of kinks—all potentially increasing the excess energy of the grain boundary,” they write. “Therefore, as the grain size is reduced, the value of the specific grain boundary energy may be increased … which could translate into reduced strength (or toughness, or stability), since the strength of boundaries has been directly related to its energy in previous works.”
To better understand how grain size affects grain boundary energy at the nanoscale (and therefore likelihood of cracking), the researchers used yttria‐stabilized cubic zirconia (10YSZ) as a model ceramic system.
They synthesized nanocrystalline powders of yttria-stabilized zirconia using the reverse precipitation route. Those nanopowders then underwent high-pressure spark plasma sintering before their thermodynamic and mechanical properties were analyzed.
The researchers found grain boundary energy values do not significantly change for relatively large grains, with an average value of 0.56 J/m2 for grains larger than 36 nm. Yet the situation changes when grain sizes are smaller than 36 nm, at which point a big increase in grain boundary energy is observed (up to 0.84 ± 0.4 J/m2 at 16 nm).
“This phenomenon can be attributed to a change in the grain boundary area and volume, with higher energy boundaries being more favorable to accommodate the geometry of such small grain sizes,” the authors write.
They note that another possible explanation for the observed grain boundary energy increase is the increase of triple joints and density of kinks, “assuming those increase the excess energy of the system.” However, they quickly discount this idea. “The fraction of triple junction is increased to 0.34% at 36 nm, and 1.62% at 16 nm. Despite the onset coincidence, the actual fraction of triple junctions is very small,” they explain.
They offer a final alternative explanation that the energy change could be attributed to a size-induced complexion transition, but “This is, of course, highly speculative at this point as it can also be related to impurities.”
How this increased grain boundary energy relates to hardness is discussed in the final part of their results and discussion section.
“As grain sizes decrease, hardness increases and reaches a maximum of 18.41 ± 0.26 GPa at the grain size of ~27 nm,” they write. “Below this critical size, … hardness decreases down to 16.36 ± 0.32 GPa at ~17 nm.”
When observed on the macroscale, the increased number of nanocracks can give the impression that the ceramic is softening. “But softening in a lay language would mean that the [ceramic] is actually more mobile at the atomic level,” Castro explains in an email, “and our data doesn’t show that.” Instead, “we notice the [ceramic] is always cracking underneath the indentation, be it with large grains or small ones.”
Now that the researchers established that cracking appears to be the mechanism behind inverse Hall-Petch in ceramics, Castro says the next step is to define a strategy to control cracking and thereby avoid the inverse Hall-Petch relation.
The paper, published in Journal of the American Ceramic Society, is “Size-induced grain boundary energy increase may cause softening of nanocrystalline yttria-stabilized zirconia” (DOI: 10.1111/jace.16886).