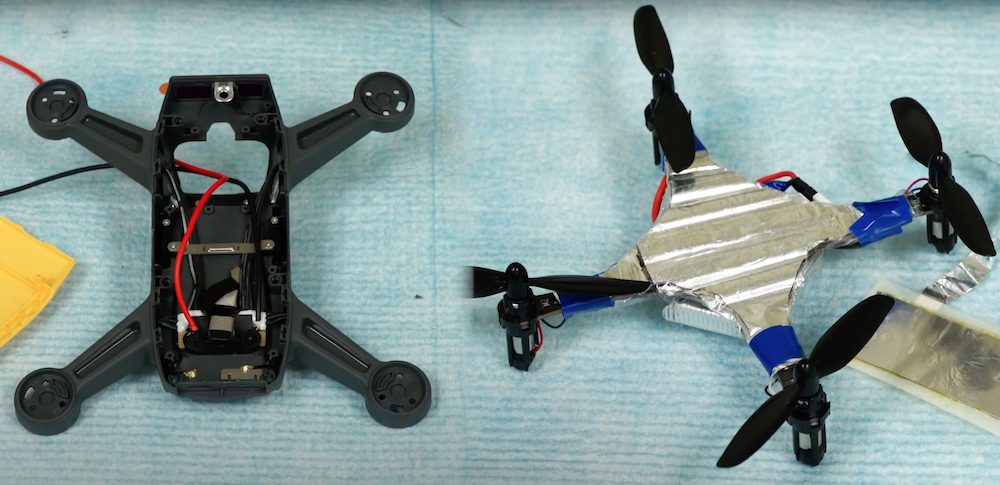
[Image above] University of Michigan researchers put their rechargeable zinc structural battery to the test as the top casing of a drone. Credit: Michigan Engineering, YouTube
You come home to a giant cardboard box waiting on your doorstep. You open it and dig through brown paper, another box, and a ton of bubble wrap to finally find…a single tube of shampoo.
Packages from Amazon are often an extreme example of wasted space, but in reality, we waste space every day without realizing it—until someone comes along and magically fits our last three shoes into carry-on luggage without sitting on the bag to zip it up. Just as Marie Kondo showed us how to maximize space in our closet, engineers also look for wasted space in current technologies to find ways to maximize a device’s design.
One device scientists are looking to redesign are batteries. As stated on MIT’s Deshpande Center webpage, 60 to 90 percent of the weight of an electric car’s battery package does not contribute to energy storage. That means 60 to 90 percent of the battery package does nothing but create additional weight in a vehicle, which causes the battery to lose charge more quickly because it must move more weight.
We could eliminate that extra bulk and design a sleek battery package that only contains parts necessary for energy storage. But why stop there? If we want to maximize design, why not completely eliminate the battery package—and turn the battery into the car itself?
That is the idea behind structural batteries, a concept that pictures batteries as both an energy source and a construction material. Instead of simply storing and releasing energy, structural batteries would serve as a vehicle’s body, whether the wing of a drone or an electric car bumper.
Of course, if a battery is going to serve as a car bumper, it needs to be able to handle some pretty hard hits (especially if it’s located on an autonomous vehicle, which tends to get rear-ended). According to new research at the University of Michigan, our own bodies may hold the answer to a perfect design.
“A battery that is also a structural component has to be light, strong, safe and have high [load-bearing] capacity,” says Nicholas Kotov, University of Michigan professor of materials science and engineering who led the research, in a university press release. “Unfortunately, these requirements are often mutually exclusive.”
Often exclusive—but not always. To get the best of both worlds, Kotov and his team designed a solid electrolyte modeled on cartilage, the white, flexible connective tissue that helps hold your joints together.
“Cartilage turned out to be a perfect prototype for an ion-transporting material in batteries,” says Kotov. “It has amazing mechanics, and it serves us for a very long time compared to how thin it is. The same qualities are needed from solid electrolytes separating cathodes and anodes in batteries.”
To create the cartilage-like solid electrolytes, the researchers used aramid nanofibers to stand in for collagen, while polyethylene oxide and a zinc salt replaced soft components of cartilage.
In today’s video, watch the researchers put their rechargeable zinc structural battery to the test as the top casing of a drone. And see them evaluate the battery’s safety—by stabbing it with a knife!
Credit: Michigan Engineering, YouTube