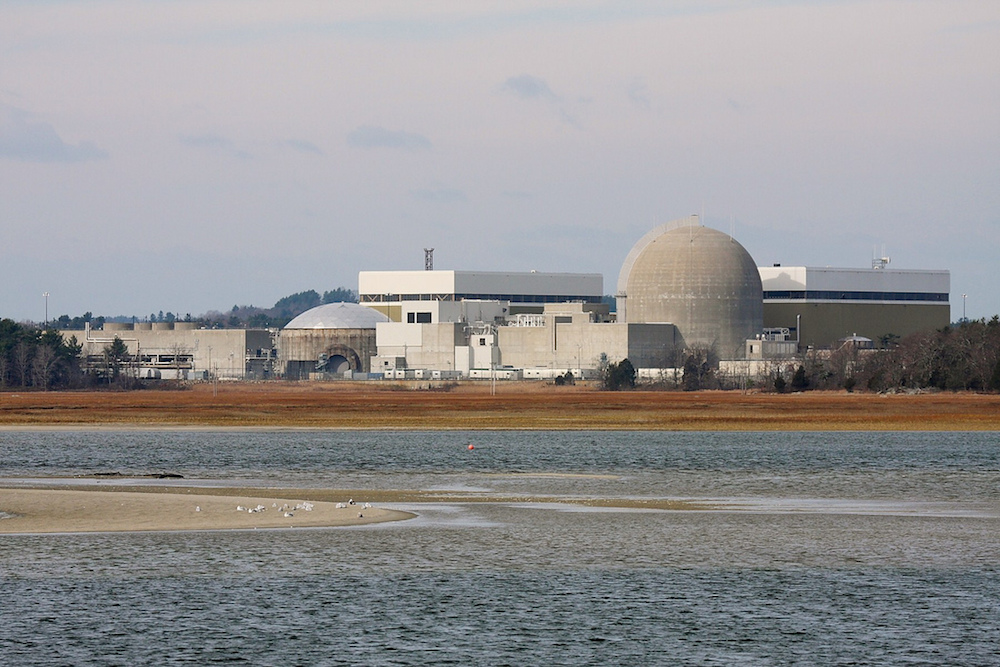
[Image above] The Seabrook Station Nuclear Power Plant is the only commercial nuclear plant known to suffer from an alkali-silica reaction in the United States. ASR prevention is an important concern when constructing nuclear plants. Credit: Jim Richmond, CC BY-SA 2.0
Though nuclear power currently faces an uncertain future in the United States, other countries—like China and Russia—are capitalizing on the growing global nuclear power market. As countries prepare for the construction of sophisticated nuclear reactors, plant designers turn to a familiar material to safeguard against failure: concrete.
Nuclear power reactors are typically lined with concrete, which in turn are housed in a larger steel containment vessel and then surrounded by an outer concrete structure. Unlike the concrete that makes up a sidewalk, concrete used in nuclear power plants uses high-density aggregates (coarse to medium grained particulate material) to shield effectively against radiation. However, this radiation shielding concrete, like average-density concrete, can be susceptible to alkali-silica reactions.
Alkali-silica reactions (ASR) occur when aggregates containing certain forms of silica react with hydroxyl ions in the alkaline cement pore solution. The reaction produces a gel, which absorbs water from the surrounding environment and expands. The expansion of the gel exerts pressure on the concrete and causes the concrete to crack and fail.
While nuclear power plant failure from ASR is uncommon—there is only one commercial nuclear plant in the United States known to suffer from ASR—ASR prevention is still an important concern for governments constructing new nuclear plants. This preemptive planning is pursued in a recent article from Poland.
In anticipation of Poland’s goal to start operating its first nuclear power plant after 2030, researchers from the Institute of Fundamental Technological Research and the Institute of Ceramics and Building Materials tested five high-density aggregate possibilities for reactor shielding concrete: three barites, a magnetite, and a hematite.
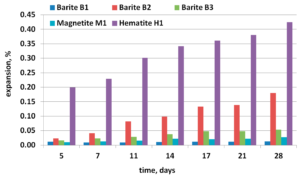
The hematite aggregate and second barite aggregate expanded more than the allowable 0.08 percent in 28 days. The magnetite aggregate and other two barite aggregates passed further testing. Credit: Daria Jóźwiak-Niedźwiedzka; Materials, CC BY 4.0
The researchers performed an Accelerated Mortar Bar Test on the aggregates according to the American Department of Defense specifications, a more stringent version of ASTM C1260. The researchers state that while ASTM C1260 considers aggregates non-reactive if they expand less than 0.10 percent in 14 days, the DOD specification sets the cutoff at 0.08 percent expansion in 28 days.
The hematite aggregate and second barite aggregate expanded beyond the allowable 0.08 percent after 28 days in 176°F (80°C), the hematite by a noticeable 0.43 percent. Post-mortem microstructure analysis on these aggregates using scanning electron microscopy confirmed the presence of alkali-silica gel. Further testing on the magnetite aggregate and first and third barite aggregates according to ASTM C1293 showed all three aggregates stayed under the 0.04 percent concrete prism expansion allowed after one year in 100°F (38°C) and high humidity.
In the article, the researchers attributed the expansion of the hematite aggregate and the second barite aggregate to the presence of microcrystalline quartz. All tested high-density aggregates contained SiO2 crystals, but only two of the aggregates—hematite and the second barite—had microcrystalline quartz. Microcrystalline quartz particles are 10–60 μm in diameter, while quartz over 60 μm is considered to have a negligible effect on expansion. Crystals over 130 μm are considered harmless.
A previous study stated that high specific weight aggregates—like barites—have almost null reactivity with alkalis in cement, yet the current researchers stressed it is important to consider not only the type of rock but also its mineralogical composition when assessing its potential for reactivity. “Aggregate reactivity depends not only on the type of silica mineral [an aggregate] contains, but also on the size and distribution of these minerals within the aggregate structure,” say the researchers in the article.
The researchers note that there were no high-alkali cements used in the research because none are available on the Polish market, but that likely did not affect the results. “According to ASTM C1260, the alkali content of the cement has a negligible or minor effect on the expansion in this test because the specimens are stored in a 1 M NaOH solution,” say the researchers.
The open-access paper, published in Materials, is “Alkali-Silica Reactivity of High Density Aggregates for Radiation Shielding Concrete” (DOI: 10.3390/ma11112284).