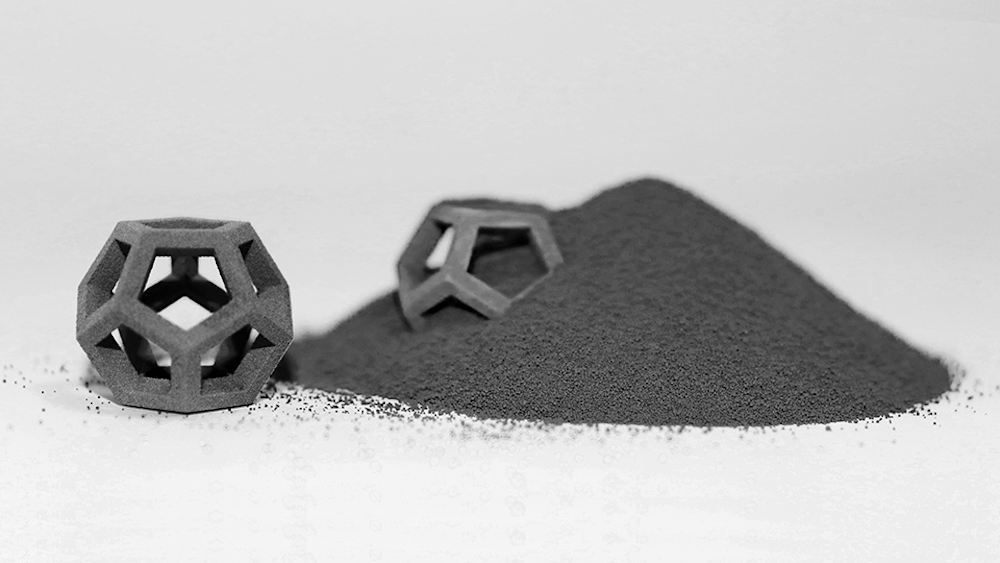
[Image above] Machining cemented carbide parts is difficult due to the high hardness of tungsten carbide. Additive manufacturing may be an easier way to manufacture the material. Credit: ExOne
In just under a week, the December issue of the ACerS Bulletin will arrive. In keeping with the last two December issues’ theme of ceramic and glass materials in everyday life (specifically in automobiles and smartphones), this December we look at ceramic and glass materials in a house.
Tungsten carbide is one ceramic that shows up in many homes in the form of cutting tools, like drill bits and saw blades.
To say the tools are “tungsten carbide cutting tools” is a bit of a misnomer, though, as the material that makes up the tools is actually a composite rather than pure tungsten carbide.
To create parts made from cemented carbide, the composite material used in cutting tools, small tungsten carbide particles are typically mixed with other carbides, such as titanium carbide, tantalum carbide, and niobium carbide. These carbide powders are mixed and compressed in a mold along with powdered cobalt metal, which acts as the “glue” to hold everything together once the mixed powder is heated in a furnace and the cobalt melts.
The next step of the process is where things can get difficult—shaping the part to achieve the correct dimensions and edges.
“Due to the high hardness of [tungsten carbide], machining of the densified material is very time and cost-intensive,” the United States Army Research Laboratory (ARL) states in a recent patent application. “Also, the subtractive nature of the machining process limits the complexity of part shapes.”
That is why the ARL decided to take an additive, rather than subtractive, approach to cemented carbide manufacturing.
In its 20-page patent application, the ARL proposes a cemented carbide additive manufacturing process based on powder bed fusion with selective laser melting, including a step of hot isostatic pressing to increase density of the part.
“Manufacturing parts with the methods disclosed herein will eliminate the necessity to machine the parts after sintering,” the ARL researchers write. “Furthermore, the methods disclosed herein allow for spatially controlling binder content through the part material, which provides for functionally graded mechanical, magnetic, electrical, and/or sonic properties.”
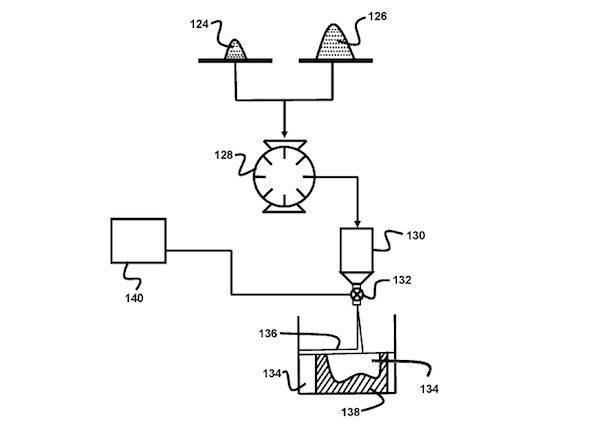
In addition to developing a way to more easily manufacture cemented carbide, ARL is interested in finding a replacement for cobalt (the “glue”) because it is expensive and reportedly carcinogenic.
Using their patent-pending process, ARL published an open-access paper investigating using an iron-nickel-zirconium binder with four commercially available tungsten carbide powder particle sizes.
“Even with the relatively low binder content [10 wt.% Fe-Ni-Zr], most of the samples possessed structural integrity, with theoretical skeletal densities as high as 95% with macroscale open porosity,” the researchers write in the conclusion.
The open-access paper, published in The Journal of The Minerals, Metals & Materials Society, is “Additive manufacturing of cemented tungsten carbide with a cobalt-free alloy binder by selective laser melting for high-hardness applications” (DOI: 10.1007/s11837-019-03366-2).
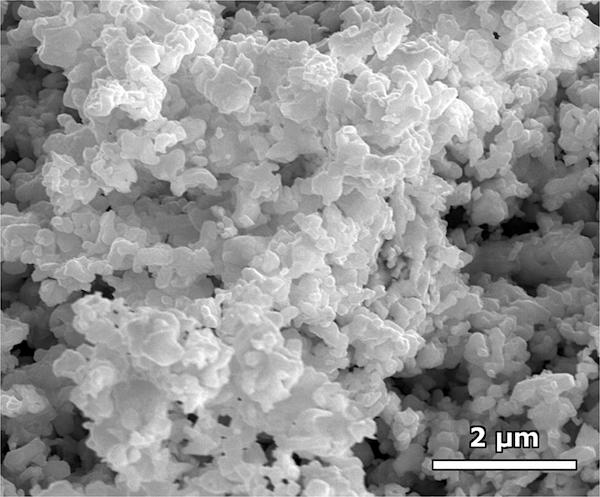
ARL is not the only group working on 3D printing cemented carbide.
Additive manufacturing company ExOne recently entered into a collaboration with Global Tungsten & Powders Corporation to advance tungsten-based metal 3D printing using binder jetting. They will focus on cemented carbide and copper-tungsten, a material used in high-voltage electrical applications.
The University of Pittsburgh and General Carbide Corporation are also collaborating on a binder jetting project thanks to an award that “will enable research into better base powders and 3D printing methods for more effective and economical use of tungsten carbide in additive manufacturing,” according to a December 2018 University of Pittsburgh press release.