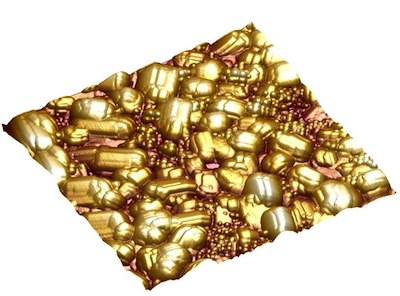
Atomic force microscope image of 50-nm diameter silica nanoparticles on PTFE surface. Researchers at the University of Arkansas found that relatively low concentrations of the particles greatly improved PTFE wear resistance. Credit: M. Zou, University of Arkansas
Well known as a nonstick surface in applications from kitchen tools to aerospace and medical components, polytetrafluoroethylene (Teflon) is getting a boost in wear resistance thanks to silica nanoparticles.
According to this press release, researchers at the University of Arkansas (Fayetteville) treated PTFE films with silica nanoparticles to significantly reduce wear while maintaining low friction in tests.
In a comparison of PTFE surfaces impregnated with silica nanoparticles versus pure PTFE films and bare stainless steel, the researchers found the composite films had greatly improved wear characteristics. All PTFE coatings were produced by dip coating type 316 stainless steel substrates.
According to researcher Min Zou, associate professor, director of the university’s Nano Mechanics and Tribology Laboratory (NMTL), and holder of the 21st Century Professorship in Mechanical Engineering, workers tested PTFE surfaces with two concentrations of 50-nm diameter silica nanoparticles—1.7 and 3.3 wt.%—against a conventional PTFE surface and bare stainless steel.
“Linear reciprocating wear tests were performed by repetitively rubbing the test samples against a chrome steel ball under an applied pressure up to 0.5 GPa,” Zou explained in an e-mail message. “The pure PTFE film failed immediately under 0.5 GPa pressure, while the composite film with 3.3 wt.% silica lasted 300 cycles.”
Results of the initial study were published in Tribology Transactions, a journal of the Society of Tribologists and Lubrication Engineers (Park Ridge, Ill.). The paper received the Society’s Al Sonntag Award for the best paper published on solid lubricants.
Zou and her team have continued their research with further development of the silica–PTFE composite material as well as testing of other types of nanoparticles in thin PTFE coatings, she reports. “The durability of the film has been increased four times compared to what we reported in this paper. If adding an adhesive layer, durability is increased 70 times. “
NMTL has developed a variety of nanoengineered surfaces (NESs), which are engineered with nanoscale topographies and chemistries to reduce friction and wear in tribological applications, change wetting properties of surfaces for anti-fogging and self-cleaning properties, and facilitate cell adhesion and growth in biomedical applications. Zou welcomes collaborative opportunities on novel methods of fabrication, characterization, and applications of NESs.