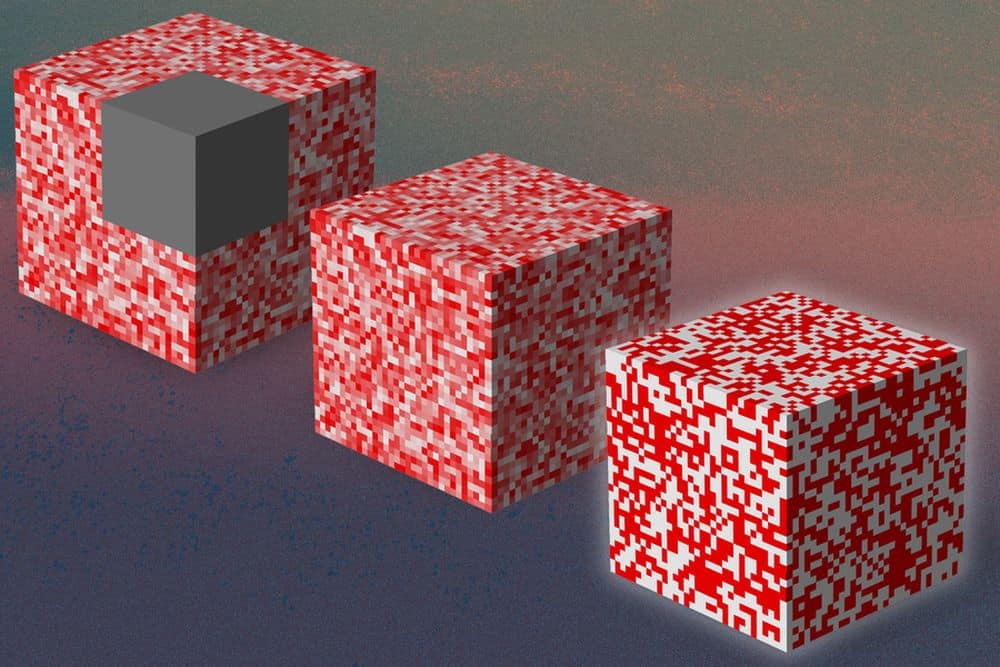
[Image above] Researchers at the Massachusetts Institute of Technology developed a deep learning method that can predict a material’s internal microstructure based solely on its external surface characteristics. Credit: Jose-Luis Olivares/MIT and the researchers
Imagine you stand in front of three doors, only one of which conceals a grand prize. After choosing a door, one of the other two doors opens to reveal it does not contain a prize. You now have the chance to stick with your original choice or switch to the other remaining door. Which do you choose?
This brain teaser is known as the Monty Hall problem, after the late Canadian television host Monty Hall. Hall famously hosted the television game show Let’s Make a Deal, which presented contestants with the exact dilemma presented above.
Many contestants stay with their original choice, believing that both doors have equal chances of presenting a prize. But this misconception was famously addressed in a 1990 letter to Marilyn vos Savant’s “Ask Marilyn” column, in which vos Savant explained that switching doors comes with a two-thirds probability of success compared to the one-third probability of staying with the original door.
This counter-intuitive answer is reached by accounting for specific assumptions about how the host and contestant choose their doors. Even though both choices ostensibly appear the same, considering surface-level information about the situation can provide probable information about what’s behind each door.
This approach to gaining knowledge about hidden information—by drawing conclusions based on what you can see—is the basis for a new deep learning method developed at Massachusetts Institute of Technology. It predicts the internal microstructure of a material based solely on data about the material’s exterior surface conditions.
Doctoral student Zhenze Yang and professor of civil and environmental engineering Markus Buehler developed the new method. In an MIT press release about the method, Buehler explains that materials engineering tasks are often hindered by limited information.
“If you have a piece of material—maybe it’s a door on a car or a piece of an airplane—and you want to know what’s inside that material, you might measure the strains on the surface by taking images and computing how much deformation you have. But you can’t really look inside the material. The only way you can do that is by cutting it and then looking inside and seeing if there’s any kind of damage in there,” he says.
Nondestructive analysis techniques, such as radiographic testing, can provide information about the internal microstructure. However, such techniques can be expensive and often require bulky equipment, limiting the use of these techniques to evaluate materials in the field.
In recent years, the development of deep learning methods to model materials systems provides new opportunities to perform materials analysis and characterization with limited information.
The new method developed at MIT generates internal microstructure predictions by combining multiple deep learning architectures. Specifically,
- An artificial intelligence model is first trained to “fill in the blank” (recover complete field information from a partial field) by using vast amounts of data about surface measurements and the interior properties associated with them.
- A second artificial intelligence model then “solves the puzzle,” i.e., uses the recovered complete field information as input to reversely obtain the corresponding microstructure.
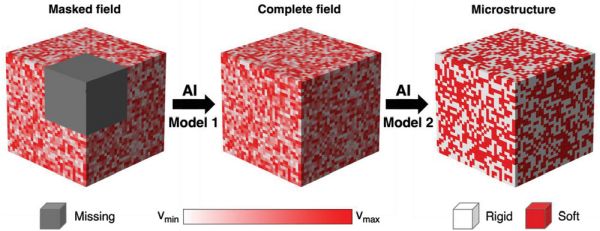
In an open-access paper describing the new model, Yang and Buehler showed it generated excellent predictions for heterogeneous composite microstructures under both 2D plane strain and 3D bulk cases.
In the MIT press release, Yang notes that the method is broadly applicable.
“It is not just limited to solid mechanics problems, but it can also be applied to different engineering disciplines, like fluid dynamics and other types,” he says.
Buehler adds that it can be applied to determining a variety of properties, not just stress and strain but fluid fields or magnetic fields as well.
“[The method is] very universal, not just for different materials, but also for different disciplines,” he says.
All data and codes used for this study are freely available for anyone to use through GitHub at https://github.com/lamm-mit/FieldCompleter.
The open-access paper, published in Advanced Materials, is “Fill in the blank: Transferrable deep learning approaches to recover missing physical field information” (DOI: 10.1002/adma.202301449).