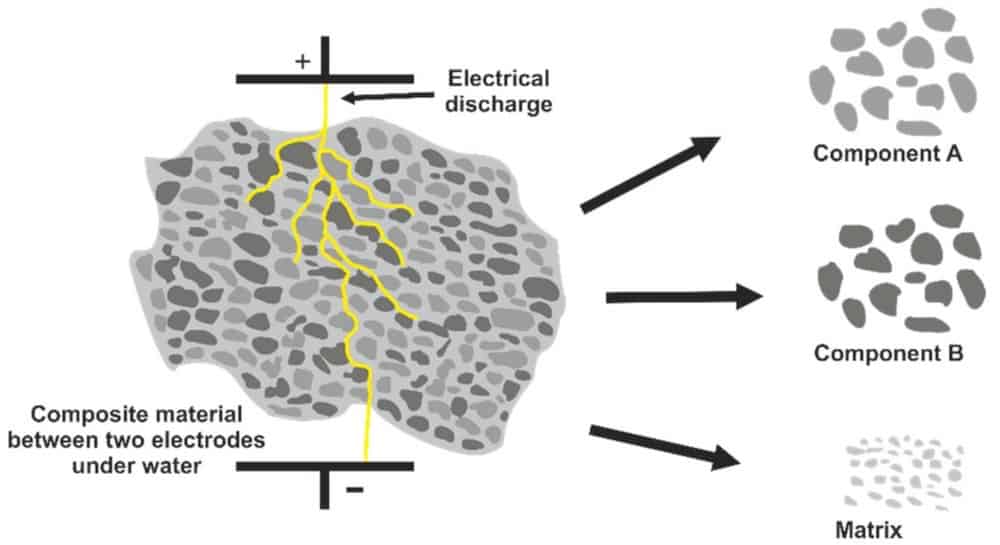
[Image above] Illustration showing electrodynamic fragmentation of a composite material. This process takes place underwater to enable pulsed high-voltage discharges to penetrate the composite, which then separates selectively along grain boundaries. Credit: Seifert et al., Processes (CC BY 4.0)
For those in the refractories industry, Chicago was the place to be this week—the Unified International Technical Conference on Refractories took place March 15–18 and welcomed professionals and students from around the world.
Sustainability was a big focus for presenters at the conference. Historically, high levels of energy consumption and carbon emissions have been defining features of the refractory material production process. However, as awareness of the impacts of climate change increases, so too do efforts by the refractories industry to decrease its environmental impact.
Reducing reliance on raw materials by recycling and reusing spent refractories is one approach the industry has considered. Yet producers must be careful of possible impurities, which could result in inadequate wear resistance of any new refractory products made from the recycled materials. So developing methods to clean impurities from the recycled refractories is essential to advancing this approach to sustainability.
Electrodynamic fragmentation is one method that could prove useful for refractory waste recovery. This method, which was first investigated and described by Russian scientists in the late 1940s, uses pulsed high-voltage discharges to separate bulky multiphase material selectively along grain boundaries. Compared to mechanical separation processes, electrodynamic fragmentation does not generate abrasion and thus no dust or other contamination.
Researchers at the Fraunhofer Institute for Building Physics in Germany have taken a particular interest in exploring the potential of electrodynamic fragmentation to recycle composites. Since 2012, Volker Thome, head of the Department of Inorganic Materials and Recycling at Fraunhofer IBP, has led experiments using this technique to recycle waste concrete, carbon fiber-reinforced polymers, and municipal waste incineration ash.
In a recent open-access paper, two of Thome’s frequent collaborators—Severin Seifert and Sebastian Dittrich of Fraunhofer IBP—conducted a new study with independent researcher Jürgen Bach on the applicability of electrodynamic fragmentation to refractory waste.
They chose refractory waste samples from three different fields of application for the experiment—highly sintered brick for sintering or rotary kilns (RefMat-1); corundum stone for melting tanks (RefMat-2); and functional refractory ceramic from the steel industry (RefMat-3).
These samples were selected to determine the effectiveness of electrodynamic fragmentation at separating materials exposed to different temperatures, as “higher temperatures lead to a stronger sintering of the individual components, which makes it considerably more difficult to process or cleanly separate,” they explain.
They began by crushing the samples into small pieces, about 4–5 cm each, and processed them to determine the optimal fragmentation parameters for each material. They then used these optimal parameters to fragment 20–32-kg batches of each of the three samples.
The researchers found they could use optical sorting to categorize the various materials separated out during the fragmentation process. Only the white corundum from sample material RefMat-3 could not be sorted out because the color differences compared to the matrix material were too small.
Analysis of the separated and sorted materials revealed a very clean surface that was almost completely free of binder residues and other adhesions. Additionally, comparison of the chemical composition with original raw materials showed almost no observable differences.
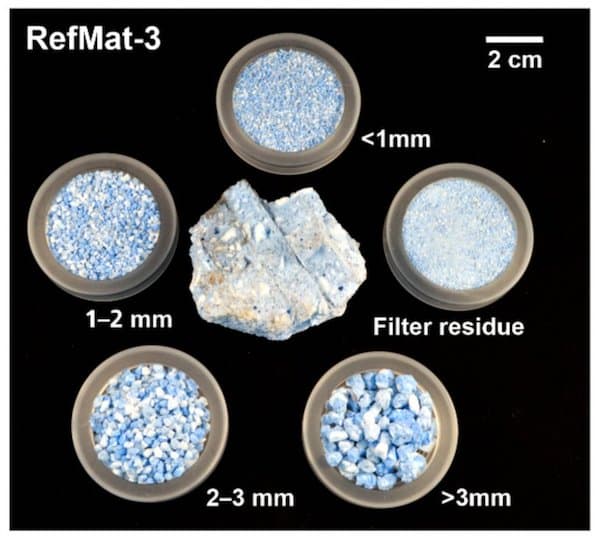
After confirming the chemical similarity, the researchers fabricated new refractory ceramics using the recovered materials. The processing properties and mechanical tests of the recycled refractories did not show any adverse effects.
“However, no testing of the newly developed refractory material under working conditions (e.g., lining in an aluminum melting furnace) has been taken place so far. Thus, the material must be checked for further aspects such as corrosion resistance, thermal shock resistance and abrasion resistance,” they write.
The researchers conclude that electrodynamic fragmentation may be a promising alternative to existing recycling technologies. “However, further research and development work is needed to make a recycling process for refractory materials economically realizable on an industrial scale,” they write.
Based on this study, the researchers applied for a patent titled “Method for recycling ceramics, regenerated materials obtained thereby, and use of the regenerated materials for manufacturing ceramics.”
The open-access paper, published in Processes, is “Recovery of raw materials from ceramic waste materials for the refractory industry” (DOI: 10.3390/pr9020228).