Wednesday, May 6
Keynote #1
Testing, Quality, and Health & Safety
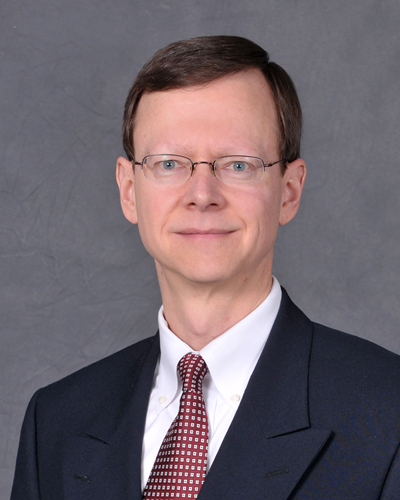
J. Douglas Jeter, Harrop Industries
OSHA’s Top 10 Citations in 2019 and How You Can Avoid Them in 2020
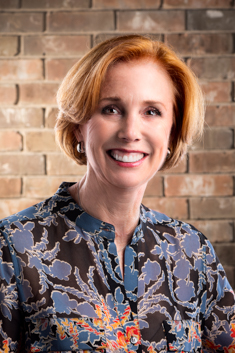
Mary Ann Keon, Acme Brick
Ergonomics in a Heavy Manufacturing Environment
In a typical heavy manufacturing environment, strains and sprains account for over 40% of most injuries. These musculoskeletal injuries are typically a result ergonomic factors arising from heavy manual labor and older, improperly designed work stations. Replacement of equipment or wholesale re-design is not always technically or economically feasible. It can also be challenging to identify which job tasks have the highest likelihood of causing a musculoskeletal disorder (MSD). In this presentation, you will learn how one company developed an easy to use numerical scoring tool that uses standard ergonomic principles as applied to an individual job task. By scoring multiple tasks, it is possible to prioritize the tasks and, therefore, work more effectively in mitigating specific risk factors to reduce the likelihood of an MSD. Using this tool, these evaluations and resulting risk reductions can be applied in any situation by plant level personnel, not trained ergonomists.

William Walker, Tenneco Powertrain
Making Sense of Failure Modes and Effects Analysis
Failure Modes and Effects Analysis (FMEA) is a structured approach used by the automotive industry for identifying potential failure modes that may exist in the design of a product or process. Two common types of FMEAs are for the design of a product (D-FMEA) and the process for producing the product (P-FEMA). The objective of an FMEA is to identify all possible modes by which a product of process might fail, and then to prioritize and limit these failure modes.
For ceramic materials performance, properties and processing are closely connected. FMEA is an ideal tool to systematically evaluate the interacting effects of processing and materials characteristics on the properties of the material and the performance of components made form the material. FMEAs developed for automotive spark plug insulators following current AIAG and VDA guidelines for the North American and European automotive industries is used to illustrate how this methodology can be used to improve the quality of ceramic components.
Bio

Beau Billet, Edward Orton Jr. Ceramic Foundation
Non-Destructive Techniques to Determine Young's Modulus for Ceramics
Bio
Thursday, May 7
Keynote #2
Ceramic Processing: Advanced Ceramics
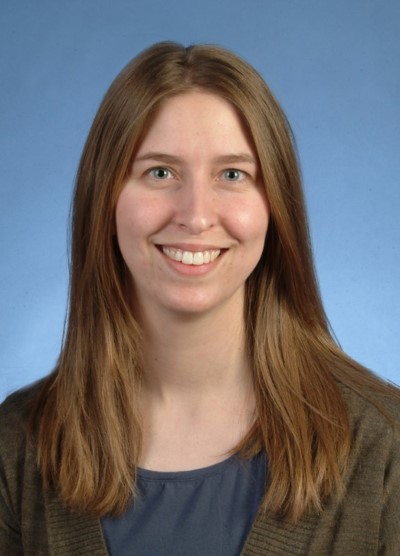
Cathleen Hoel, G.E. Research
Practical considerations for ceramic additive manufacturing from conception to production

David O'Brien, SINTX
Key Steps in Successfully Manufacturing Silicon Nitride
The development, validation, and ongoing improvements of the manufacturing processes in the production of Si3N4 components are presented and discussed. Manufacturing is conducted in a facility specifically dedicated for this purpose using processes designed to yield net shape parts by powder preparation, green start forming (pressing and CNC machining), debinding, sintering, and hot isostatic pressing. These manufacturing methods were industrialized using Taguchi fractional factorial experimental designs. Lean and Six Sigma techniques are used to continually improve the process—increase yields and decrease costs. Over 35,000 medical devices produced by this process have been successfully implanted in humans with positive patient outcomes.
Bio
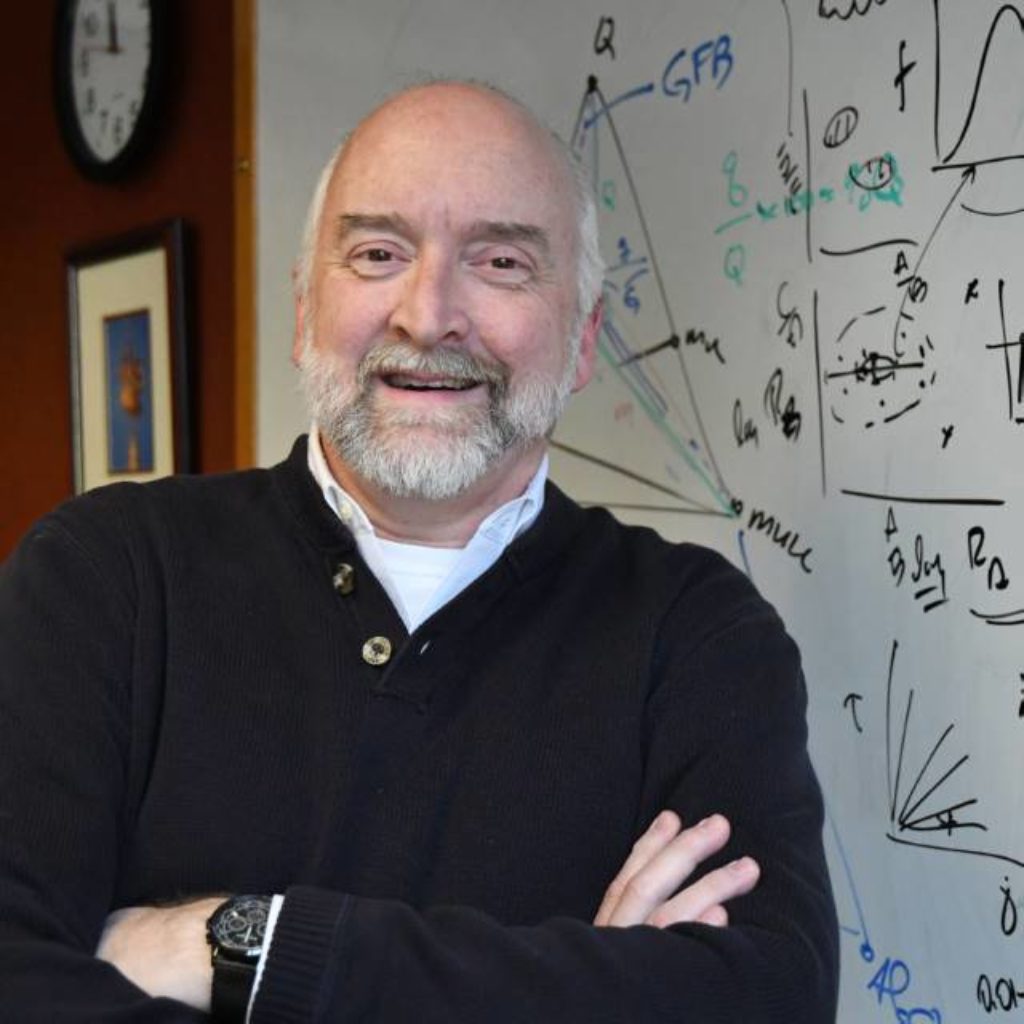
Bill Carty, Alfred University
A Comprehensive Approach to Ceramic Forming using Specific Volume Diagrams: Examples with Extrusion
Specific volume diagrams, when corrected for density (i.e., on a volume basis) can be used to define the “excess” water content necessary to define a process “window.” The excess water amount is defined as the amount over that required to fill the pore volume. The consequence of this approach is that the ceramic material, be it clay, alumina, zirconia, SiC, etc., are all similar when corrected for the density of the powder. Specific examples will be provided for extrusion forming. In addition, the role of the level of dispersion is demonstrated as it controls the packing efficiency of the powder and thus directly impacts the pore volume. In addition, specific defects associated with the location (i.e., water content) within the extrusion window will be discussed.
Ceramics Processing: Traditional Ceramics
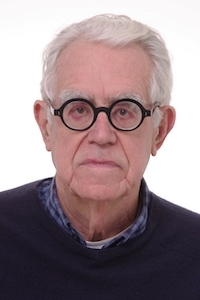
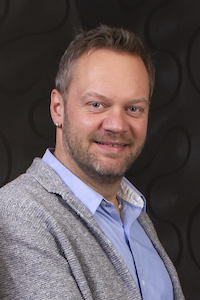
Frank Handle, ECT-KEMA GmbH
Torsten Seidel, ECT-KEMA GmbH
Old basics and new perspectives about extrusion in ceramics
Our paper aims to support the hypothesis that the mastering and implementation of new innovative approaches in the extrusion of ceramic bodies necessitates the sound understanding of basics in material science and process engineering. In principle, most of these basics are known, but they are quite often either ignored or simply forgotten.
Five essential “extrusion basics” will be highlighted in the first part of the paper, in order to show the relevance of paying attention to these in developing new challenging extrusion solutions for advanced ceramics.
This hypothesis—call it credo or business mission—has enabled ECT-KEMA to successfully develop and implement new solutions for the extrusion of ceramic and related bodies.
Five of the new ideas that have been put into practice will be presented in the second part of our paper.
Raw Materials
Matt Creedon, Washington Mills
Electrofusion of Mullite Ceramics
Mullite is widely used in the refractories industry because of its excellent high temperature properties. There are three primary routes to synthesis of mullite ceramics: fusion, sintering, and calcining of natural minerals. Each method has advantages and disadvantages, depending on the application. This paper discusses the fusion process in general and its use in the production of high purity 75% Al2O3 - 25% SiO2 mullite ceramic material. Factors such as cooling time and conditions can have significant effects on crystallite size and purity. In turn, these factors effect crushing, sizing and final performance of the finished mullite ceramic powder and parts. Finally, information about the consistency and quality capability of the fusion process as it applies to this high purity mullite will be presented.
Bio
Charles Compson, Almatis
Alumina: A raw material that is (almost) always behind the scenes
Alumina has been the backbone of the ceramics and refractory industries for more than 100 years. Alumina’s properties have been well documented for decades, used as the example for University education, and the default material for much ceramic research. Despite decades of investigation and application development, alumina continues to find new applications in emerging technologies. Alumina provides mechanical strength to the glass covering your mobile devices, wear resistance to your laminate or hardwood floors and cabinets, a safety barrier in your lithium-ion batteries, thermal conductivity in microelectronics for heat dissipation, and planarized corrosion resistant surfaces for the production of silicon wafer chips. As devices continually become smaller and soon may be printed at home, energy comes in the re-chargeable kind, the world adopts 5G technology, and full-time connectivity is less a trend than a reality, alumina is continuing to play an important role, as both an inert & functional material. In this talk, I will describe some the key roles that alumina has in modern day devices, and the properties that will continue to make it a cornerstone in technology development.
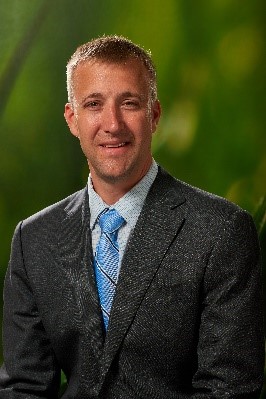