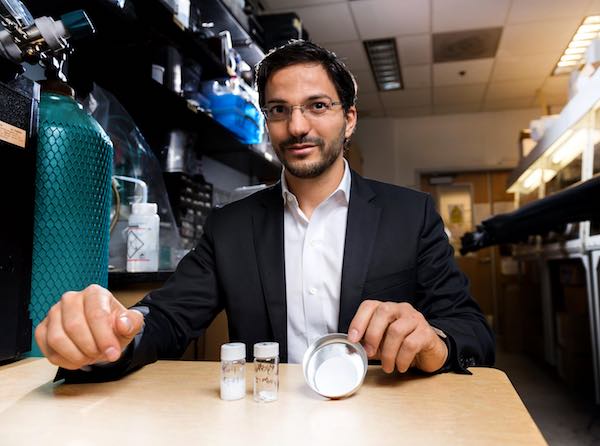
[Image above] Georgia Tech professor Gleb Yushin and a team of scientists has devised a technique to produce oxide nanowires from bulk materials. Credit: Rob Felt; Georgia Tech
An investigation into the defective batteries in Samsung’s Galaxy Note 7 has determined that a damaged separator is likely to have short-circuited the smartphones’ lithium-ion batteries, according to a Chemical & Engineering News article.
Although separators—which physically separate the battery’s electrodes—are a critical safety feature of batteries, these plastic films are becoming thinner and thinner as companies try to pack more power into same-sized batteries. That’s a problem because thin plastic films can more easily become damaged, resulting in explosive battery failures like those that Samsung encountered.
So “companies are moving to mechanically stronger and higher-temperature-performance separators made out of composites of polyethylene or other polymers and ceramics,” battery consultant K.M. Abraham says in the C&EN article.
Ceramics are an ideal material to improve the batteries of tomorrow—which need to last longer, provide more power, and decrease safety risks—because of the materials’ superior temperature resistance, among a host of other coveted properties.
Now researchers at Georgia Institute of Technology (Atlanta, Ga.) have developed a technique that may put ceramic separators at the forefront of the next generation of safer, improved batteries. The team devised a simple method to transform bulk alloy materials into oxide nanowires at room temperature and pressure, without the use of catalysts, toxic chemicals, or expensive processes.
The technique is so simple and inexpensive that the authors think it could propel incorporation of oxide nanowire materials into a variety of technologies, including next-gen batteries, lightweight structural composites, advanced sensors, and electronic devices.
“This technique could open the door for a range of synthesis opportunities to produce low-cost 1-D nanomaterials in large quantities,” Georgia Tech materials science and engineering professor Gleb Yushin says in a Georgia Tech press release. “You can essentially put the bulk materials into a bucket, fill it with a suitable solvent, and collect nanowires after a few hours, which is way simpler than how many of these structures are produced today.”
The team accidently discovered that dissolving a bimetallic alloy—consisting of a reactive metal, such as lithium, and a nonreactive metal—in a solvent dissolves the reactive metal, leaving behind nanoparticles of nonreactive metal.
“Minimization of the interfacial energy at the boundary of the chemical reaction front allows us to form small nuclei and then retain their diameter as the reaction proceeds, thus forming nanowires,” Yushin explains in the release. “By controlling the volume changes, surface energy, reactivity and solubility of the reaction products, along with the temperature and pressure, we can tune conditions to produce nanowires of the dimensions we want.”
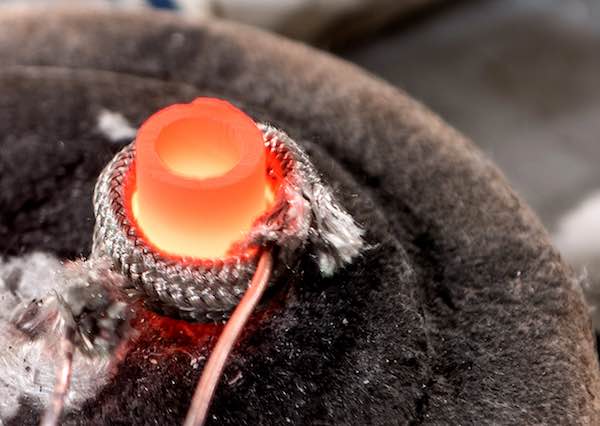
A red-hot crucible containing an alloy of lithium and aluminum. Credit: Rob Felt; Georgia Tech
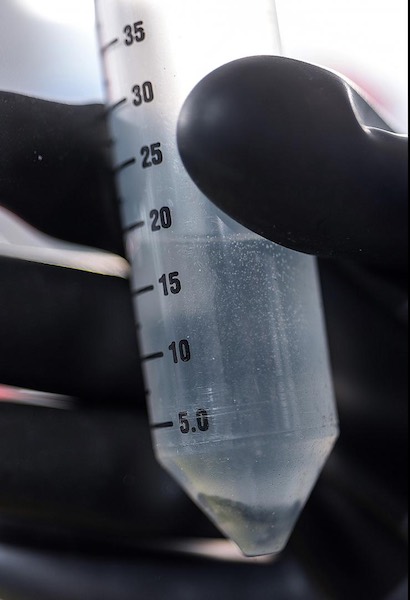
Bulk powders are then dissolved in ethanol to form the nanowires. Credit: Rob Felt; Georgia Tech
The team reports that it can tune nanowires that range in diameter from tens of nanometers up to microns. Nanowires can then be formed into paper-like sheets that could become commonplace and inexpensive materials for safer battery separators.
“Overall, this is a better technology for batteries, but until now, ceramic nanowires have been too expensive to consider seriously,” Yushin says in the release. “In the future, we can improve mechanical properties further and scale up synthesis, making the low-cost ceramic separator technology very attractive to battery designers.”
Beyond the technique’s simplicity and low cost, the process also is green—the dissolved reactive metal can be recovered from the solvent and reused, and the reaction produces hydrogen gas that can be collected and used as an alternative fuel.
The team reports it has produced lab-scale quantities of oxide nanowires from lithium-magnesium and lithium-aluminum mixes so far, and it also continues work to produce nanowires from other mixes as well. But the scientists say that scale-up should be no problem. “With this technique, you could potentially produce nanowires for a cost not much more than that of the raw materials,” Yushin adds in the release.
The report, published in Science, is “Transformation of bulk alloys to oxide nanowires” (DOI: 10.1126/science.aal2239).