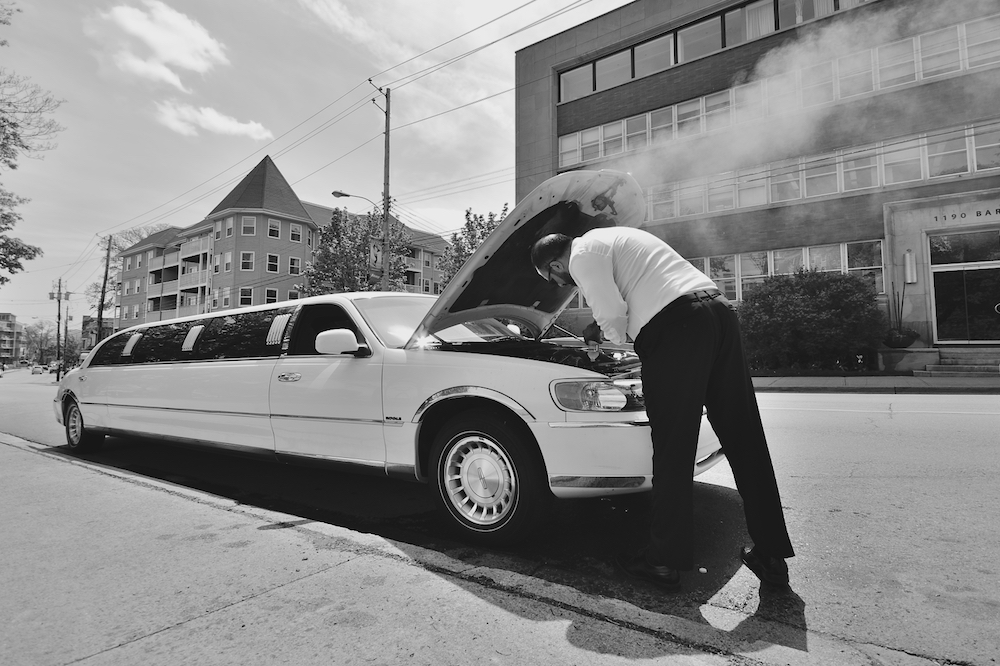
[Image above] Don’t you hate when your car overheats and you have to pull over? Better anti-freeze would improve heat transfer in automobiles and other engines. But making better products does not necessarily require new ideas—sometimes you just need to improve the materials and processes you have. Credit: Paul B, Flickr (CC BY-NC 2.0)
This post was unusually difficult to write. Not because I was uninspired—I faced an overabundance of options.
I spent hours reading the many good articles in the May-June issue of International Journal of Applied Ceramic Technology. As you may know, I have been focusing on ultrahigh-temperature ceramics (UHTCs) in recent posts, and this issue included some articles on that topic. But there were some very interesting articles on other topics as well, such as one on the oxidation of SiCf/SiC, one on fabrication of nanowire SiOC from polymer derived ceramics (PDCs), and one on PDC/filler combinations for coating steel.
With all the great choices, I decided to discuss product development. After all, research moves us toward creating tools and toys to make our lives better. But it is one thing to make a new material or to develop a new production or analysis method—finding ways to improve existing materials and processes is what pays the bills.
While other journals may include engineering and applied science of some ceramics in their aims and scopes, ACT is uniquely focused on research aimed at moving advanced ceramics from the laboratory to the production floor and beyond. And this focus is evident in two papers from the May-June issue that focus on improving effectivity of existing processes.
MAX development: Thermal management in the automotive sector
In the first article, researchers from the SRM Institute of Science and Technology in Kattankulathur, India, evaluated a nanoscale MAX phase compound as an additive to ethylene glycol, a heat transfer fluid often used in automobile engines.
Though ethylene glycol has been used for decades, researchers have sought ways to improve the heat transfer properties while maintaining or ideally reducing its viscosity. Doing so would reduce the energy required to pump the fluid through the cooling loop, thus improving automobile fuel use.
MAX phases are a class of ceramic materials that have the chemical reactivity and hardness of ceramics but thermal conductivity and other properties approaching those of metals. The researchers synthesized a nanoscale MAX (Cr2AlC) and compared the results to other ceramic materials they milled to similar particle size. To keep the comparison as simple as possible, the suspensions were all fabricated without surfactants.
The MAX phase suspensions exhibited favorable results for many of the properties tested. Most importantly, their thermal conductivities were substantially higher than the ethylene glycol and all other suspensions. Furthermore, the suspension was stable through 20 days, which was good given the simplicity of the suspension protocol.
Not all the properties showed similar improvements, though. For example, while MAX-phase suspensions’ viscosities were the lowest at high temperatures compared to all the tested samples, they were higher than that of ethylene glycol at room temperature.
MAX phase suspensions show great potential for improving automotive cooling and other heat transfer systems. We look forward to seeing further work on developing systems for stabilizing the suspensions and for optimizing the viscosity profiles.
The paper, published in International Journal of Applied Ceramic Technology, is “Development of ethylene glycol‐Cr2AlC nanofluid for thermal management in the automotive sector” (DOI: 10.1111/ijac.13253).
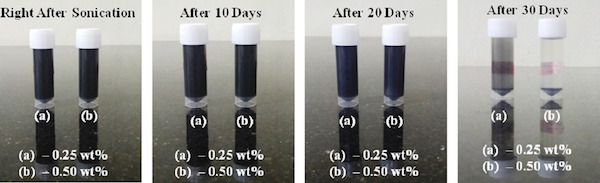
Patterned ceramic tools aid dry cutting
The second paper is elegant in its simplicity. Researchers from Qilu University of Technology (Jinan, China) and Dalian University of Technology (Dalian, China) patterned carbide cutting ceramics using a cost-effective templating technique.
While previous research cited in the article shows patterning of cutting tools (e.g., grooves, divots along the edges or corners) improves cutting performance, most created the patterns after the tool is sintered. The post-sintering patterning process requires expensive techniques, such as laser processing, electric discharge machining, focused ion beam processing, or ultrasonic elliptical vibration devices with diamond tooling.
Instead of the expensive or time-consuming post-processing described above, the Chinese researchers machined a negative template on graphite using simple engraving and milling. The negative template is placed upon the ceramic powders and cold-pressed. This step is then followed by vacuum sintering. The resulting sintered ceramic tool is cut to size and polished.
The researchers used this method to form several different patterns on cutting tools. They began by optimizing the spacing for each pattern. Using the best conditions for each pattern, they compared the performance parameters of the different patterns for dry cutting into hardened steel. They checked, among other things, cutting force, maximum temperature, and smoothness of the cut surface.
The best performing pattern reduced forces up to 24% and the cut steel face roughness was approximately half. These values were compared against a flat ceramic cutting tool (no pattern).
Most interesting, the researchers found the patterning provided a location for carbon to collect. This carbon, which came out of the steel, acted as a dry lubricant and prevented the adhesion of iron to the cutting tool. Because iron adhering to the tool reduced cutting efficiency, the pattern with the greatest amount of collected carbon had the best performance. As a bonus, the best tool also showed the least wear, potentially extending its life.
Though this tool was made in a lab, scaling up the fabrication procedure for mass production should be straightforward. I hope the researchers submit a follow-up article wherein they detail the engineering used to take their bench process into production.
The paper, published in International Journal of Applied Ceramic Technology, is “Experimental investigation of different morphology textured ceramic tools by in‐situ formed for the dry cutting” (DOI: 10.1111/ijac.13372).
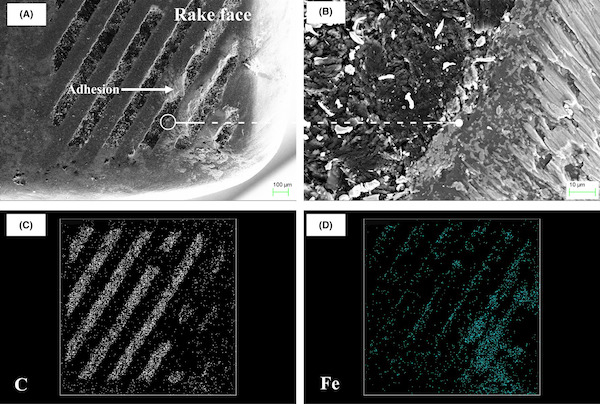