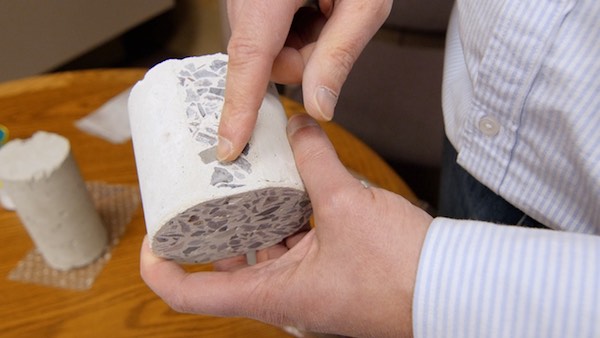
[Image above] This concrete, processed with a low-temperature solidification technique, stores carbon dioxide. Credit: Cameron Bowman; Rutgers University
Like many of us humans, most materials have goals to become stronger, lighter, cheaper, and greener (#newyearsresolutions).
But it’s not easy. So what if, instead of redesigning each individual material to conform to those demanding specifications, we could rethink a single processing method to improve various different materials?
Almost a decade ago, scientists Richard Riman and Vahit Atakan invented just such a technology, called reactive hydrothermal liquid-phase densification (rHLPD)—or, more simply put, low-temperature solidification.
Riman is an ACerS Fellow, Distinguished Professor of Materials at Rutgers University, and holds numerous patents, leading to his recent induction into the National Academy of Inventors. He founded companies Solidia Technologies and RRTC Inc., which develop eco-friendly cement/concrete and advanced composites, respectively. Atakan is a former Rutgers student and is now chief scientist at Solidia.
Their patented energy-efficient technology relies upon low-temperature, water-based reactions to form bonds within materials “based on principles of hydrothermal reaction, infiltration, reactive crystallization, and liquid-phase sintering” according to a paper published in the Journal of the American Ceramic Society last year.
“Typically, we don’t go any higher than 240ºC (464ºF) to make the composite materials,” Riman says in a Rutgers University press release. “A lot of these processes are done even at room temperature.”
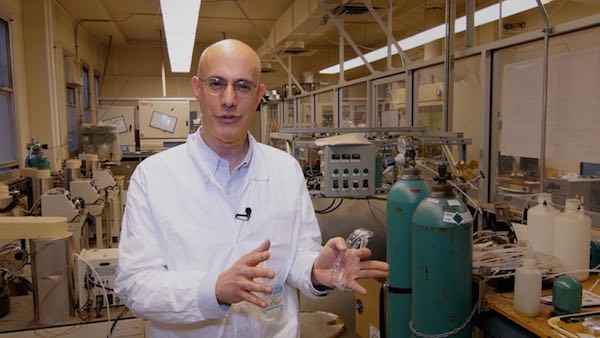
Richard Riman discusses making ceramic materials under sustainable conditions in the lab. Credit: Cameron Bowman; Rutgers University
Processing at low temperatures saves energy during manufacturing and even allows formulation of new combinations of materials that wouldn’t be possible at the higher temperatures required with more traditional processing techniques.
According to the Rutgers release, the tech has enabled formation of more than 30 materials, including carbon-dioxide storing concrete and various composites of metals, polymers, and/or ceramics.
With light yet strong attributes, such materials are perfectly suited to reduce the weight of materials used in vehicles that travel on roads, skies, and space, in addition to almost any other application you can imagine. Eventually, lighter materials improve the performance and/or reduce the energy input required for that final application, such as propelling a vehicle.
In the automotive world, incorporating materials with less weight is a big deal. Stringent regulations boosting fuel economy and consumer demand for higher performance are driving automakers towards alternative materials and advanced manufacturing techniques to lightweight vehicles. Beyond the automotive industry, almost any other form of transportation can benefit from lighter materials, too.
But lightweighting is just one potential benefit of this low-temperature solidification technique.
In addition to the energy savings from low-temperature manufacturing, such dual action in energy savings and improvement in materials properties make this technique potentially revolutionary for a really wide range of potential materials and subsequent applications. And considering that the composites market is projected to reach a value of $10.6 billion by 2022, the potential is big.
“Ultimately, what we’d like to be able to do is create a ‘Materials Valley’ here, where this technology can start one company after another, small, medium and large businesses,” Riman says in the release. “It’s a foundational or platform technology for solidifying materials that contain ceramics, among other things. They can be pure ceramics, ceramics and metals, ceramics and polymers—a really wide range of composites.”
So while there may not be a single magic technique to make us humans stronger, lighter, cheaper, and greener (yet), such a reality for materials may be closer than you think.